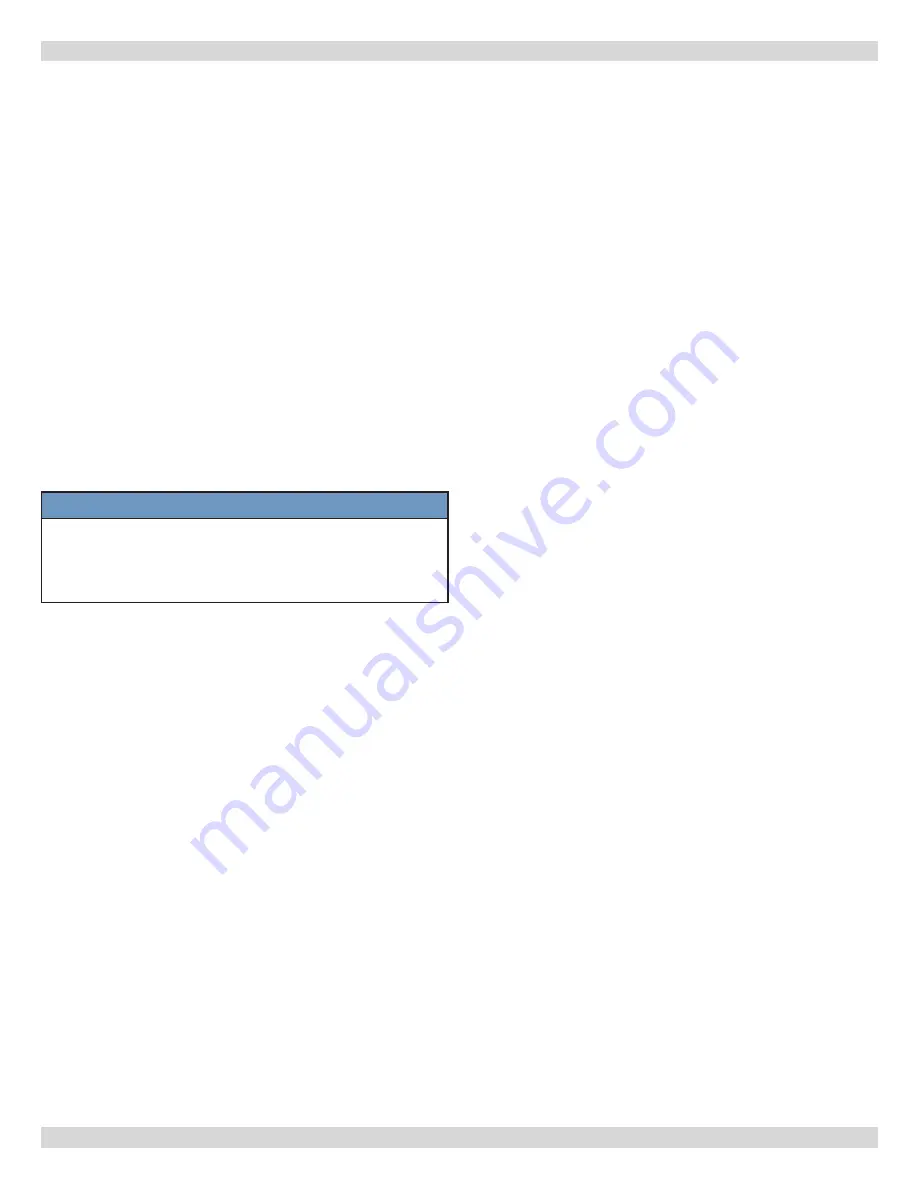
28
Filling Boiler With Water And Purging Air For Systems
With Conventional Closed Type Expansion Tanks
Refer to diagrams on “Near Boiler Piping” on pages 9 and
10 for more information.
1.
Close all zone service valves on supply and return
piping. Close expansion tank service valve. Drain
expansion tank. Open feed valve and fill boiler with
water. Hold relief valve open until water runs air free
for five seconds to rapidly bleed air from boiler, let
relief valve snap shut.
2.
Open zone service valve on supply pipe for first zone.
Open purge valve on first zone. Feed water will fill
zone, pushing air out purge valve. Close purge valve
when water runs air free. Close zone service valve.
3.
Repeat step 2 for remaining zones.
4.
Open expansion tank service valve and tank
vent. Fill tank to proper level and close tank vent.
Remove handle from expansion tank service valve so
homeowner doesn’t accidentally close it.
5.
Open all service valves. Any air remaining trapped
in return lines between service valves and boiler will
push towards expansion tank when boiler is placed in
operation.
6.
Inspect piping system. Repair any leaks immediately.
11 - STARTUP
Water Treatment And Freeze Protection
Filling Boiler With Water And Purging Air For Systems
With Diaphragm Type Expansion Tanks
Refer to the appropriate diagrams “Near Boiler Piping” on
pages 10 and 11.
1.
Close all zone service valves on supply and return
piping. Open feed valve and fill boiler with water. Verify
air vent is open. Hold relief valve open until water runs
air free for five seconds to rapidly bleed air from boiler,
let relief valve snap shut.
2.
Open zone service valve on supply
pipe for first zone.
Open purge valve on first zone. Feed water fills zone,
pushing air out purge valve. Close purge valve when
water runs air free. Close zone service valve.
3.
Repeat step 2 for all remaining zones.
4.
Open all service valves. Any air remaining trapped
in return lines between service valves and boiler
are pushed towards air vent when boiler is placed in
operation.
5.
Inspect piping system. Repair any leaks immediately.
NOTICE
Do not use stop leak compounds or other chemicals
not listed in this manual. Repair leaks in threaded
connections of aluminum boiler sections. Aluminum
threads do not seal themselves.
6.
Systems with automatic fill valves and leaks will cause
excessive fill water. This water contains oxygen.
Excessive oxygen will cause the aluminum boiler to
corrode over time. All system leaks should be repaired
immediately.