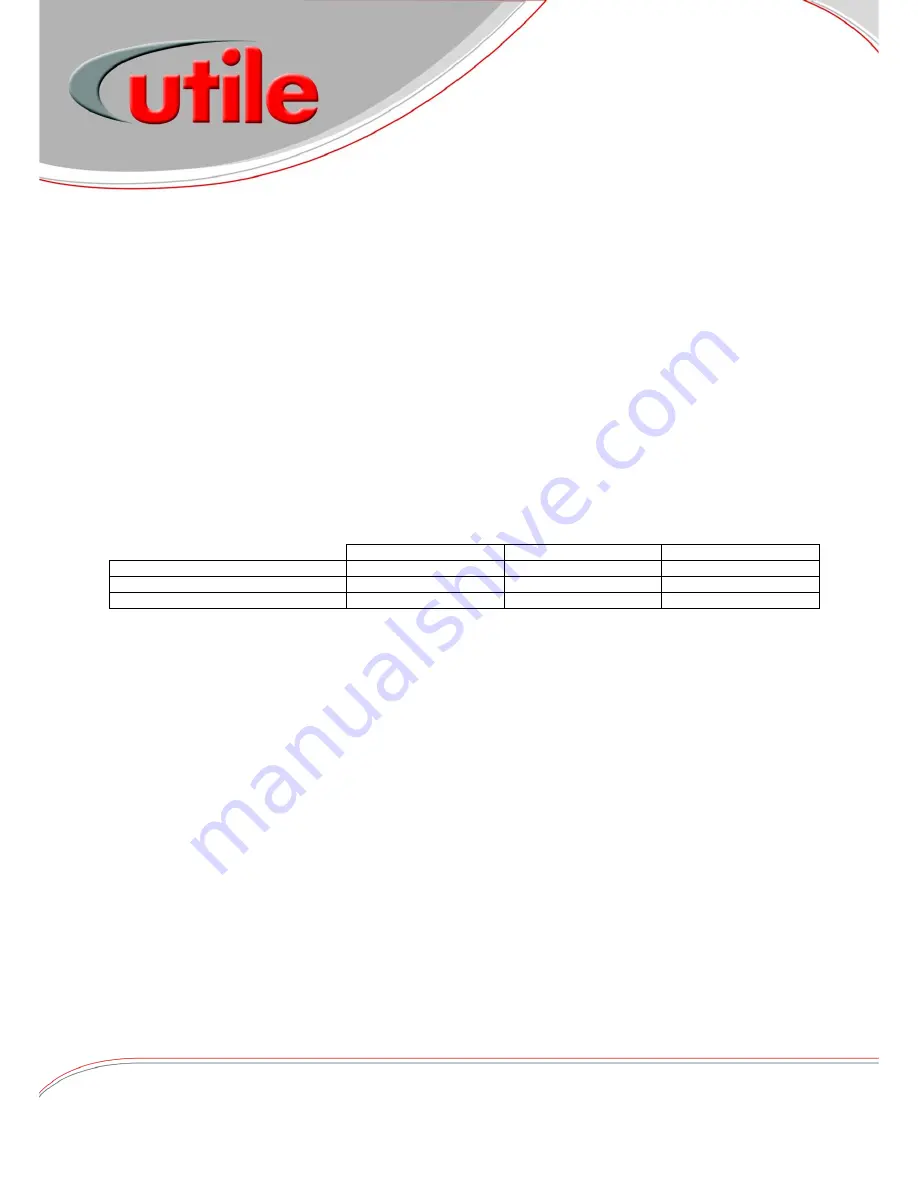
GAS COMPRESSORS / BOOSTERS
GAS & AIR MIXING SYSTEMS
AIR BLOWERS & VACUUM PUMPS
The Utile Engineering Co. Ltd.
Irthlingborough, Northamptonshire, NN9 5UG, ENGLAND
Telephone: + 44 (0) 1933 650216 Facsimile: + 44 (0) 1933 652738 Email: sales@utileengineering.com
www.utileengineering.com
13
IC182
5.
Removal of Bearings and Seals
With the rear end coverplate (3) already removed as described in 2 for blade inspection.
5.1
Using a two-leg pulley drawer the roller bearing inner race (23) can be removed from the shaft.
5.2
Should the seal sleeve (9) show signs of wear, then it can be removed by careful machining.
5.3
The bearing seal (21) and roller bearing outer race (23) can be pressed out of the coverplate for inspection.
5.4
Inspect the bearing, renew if it shows any signs of wear or pitting.
5.5
Examine the bearing seal (21) and renew if the wiping lip is worn or damaged.
With the drive end coverplate (2) already removed complete with rotor as described in 4 for cylinder renewal.
5.6
Using a two-leg pulley drawer the roller bearing inner race (22) can be removed from the shaft.
5.7
Should the seal sleeve (9) show signs of wear, then it can be removed by careful machining.
5.8
The bearing seal (21) and roller bearing outer race (22) can be pressed out of the coverplate for inspection.
5.9
Examine the bearing seal (21) and renew if the wiping lip is worn or damaged.
6.
Reassembly Procedure
This section only applies when using original bore size or replacement cylinder. Before commencing reassembly ensure that
all components are perfectly clean and oilways are clear. Lightly smear the shaft with oil to assist assembly.
The correct clearances for these machines are: -
L95HP
L130HP
L175HP
Drive End Coverplate / Rotor
0.25mm / 0.30mm
0.25mm / 0.30mm
0.25mm / 0.30mm
Rear End Coverplate / Rotor
0.10mm / 0.13mm
0.10mm / 0.13mm
0.10mm / 0.13mm
Rotor / Cylinder
0.10mm
0.10mm
0.10mm
Reassembly should start with the preparing of the rotor and shaft assembly by the fitting of the replacement seal sleeve (if
required) and the inner races of the both roller bearings.
6.1
The seal sleeve (9) are retained on the clean shaft using LOCTITE 648 adhesive or equivalent, and should be
pushed hard against the rotor face. It is essential that the width of the seal sleeve is identical to the one it is
replacing or internal clearances may be effected causing serious machine damage.
6.2
Both roller bearing inner races can now be fitted onto the shaft ensuring the bearings and any shims are fitted to
the correct ends.
Starting at the drive end
6.3
Position the bearing seal (21) into position in the coverplate (2) ensuring that the tension spring is facing the rotor.
6.4
Press the outer race of roller bearing (22) into position in the coverplate (2).
6.5
Lay the rotor/shaft assembly on the bottom of the cylinder (1), ensure the cylinder is orientated correctly.
6.6
Ease coverplate (2) onto the rotor/shaft.
6.7
The whole bearing assembly can be locked onto the shaft with the locknut (28). Set clearance.
6.8
When fitting the mechanical seal (20), wipe over the shaft with soapy water to assist the assembly, the seal can
then be eased onto the shaft and pushed against the locknut. Replacement seal seats should be lubricated for
easier fitting in the end cap.
6.9
The end cap (3) can now be fitted with the gasket (45) and any appropriate shims.
6.10
Fit new o-rings (24) into the coverplate grooves. If coverplate gasket (45) has been replaced, it is essential that
they are the same thickness as the originals, otherwise internal clearances will be affected and could cause serious
damage. Lightly smear the gasket with oil before replacing.
6.11
Place drive coverplate assembly onto cylinder (1) via location dowel and bolt with six screws (30) and with
coverplate gaskets (45) in place.
6.12
Check rotor / cylinder clearance.
Change Bearings and Seals,
Reassembly Procedure