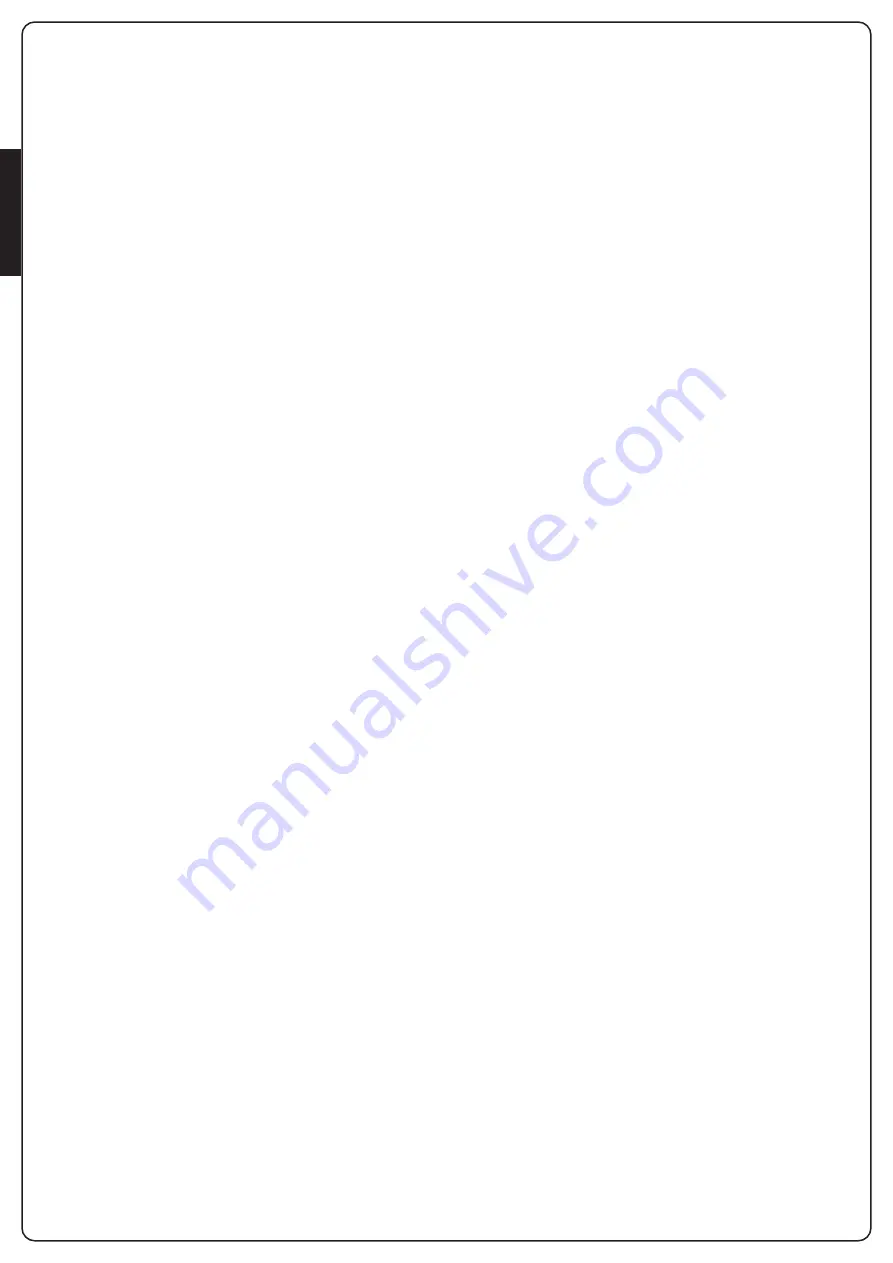
ENGLISH
- 64 -
13 - OPERATION DEFECTS
This paragraph shows some possible operation defects, along
with their cause and applicable remedy.
OVERLOAD led is on
It means that there is an overload on accessory power supply.
1.
Remove the extractable part containing terminals K1 to K10.
OVERLOAD led will switch off.
2.
Remove the overload cause.
3.
Reinsert the terminal board extractable part and check that
this led is not on again.
Too long pre-blinking
When a Start command is given and the blinker switches on
immediately but the gate is late in opening, it means that the
setup cycle count down expired and the control unit shows that
service is required.
Error 1
The writing
Err1
appears on display when you exit from
programming:
It means that changed data could not be stored.
This kind of defect has no remedy and the control unit must be
sent to V2 S.p.A. for repair.
Error 2
When a Start command is given and the gate does not open and
the display shows
Err2
It means that mosfet test failed.
This kind of defect has no remedy and the control unit must be
sent to V2 S.p.A. for repair.
Error 3
When a Start command is given and the gate does not open and
the display shows
Err3
It means that the photocell test failed.
1.
Be sure that no obstacle interrupted the photocell beam
when the Start command was given.
2.
Be sure that photocells, as enabled by their relevant menus,
have been installed actually.
3.
If you have external photocells, be sure that Foto menu item
is on
CF.Ch
.
4.
Be sure that photocells are powered and working; when you
interrupt their beam, you should hear the relay tripping.
5.
Ensure the photocells are connected correctly, as shown in the
dedicated section on page 49
Error 5
Once given a start control, the gate does not open and the display
shows
Err5
It means that the test of the safety edges failed.
Check that the menu of the test of safety edges (
Co.tE
) have
been set correctly.
Check that the safety edges enabled from the menu are installed.
Error 8
When executing a self-learning function the control is refused and
the display shows
Err8
It means that the setting of the control unit is not compatible with
the requested function. In order to execute the self-learning it
is necessary that the Start inputs are enabled in standard mode;
to survey the currents of the motor it is also necessary that the
length of the opening and closure are at least of 7,5 seconds.
Error 9
When you are trying to change the control unit setups and the the
display shows
Err9
It means that programming was locked by means of the
programming lock key CL1+ (code 161213).
To change the settings it is necessary to insert in the connector of
the ADI interface the same key used to activate the programming
lock, and unlock the device
Error 90
When there is an attempt to start an operational cycle without
having yet performed the initialisation procedure, the message
Er90
appears.
Perform the initialisation procedure.
Error 91
If, during the initialisation procedure, the control unit fails the
exterior photocell test, the display shows the message
Er91
Check the photocell connected to the PHOTO input is working.
PLEASE NOTE: This abnormality does not delete data
acquired using the initialisation procedure
Error 92
If, during the initialisation procedure, the control unit detects an
obstacle during movement of the gates, the display shows the
massage
Er92
Ensure there are no obstacles within the gate movement area and
repeat the initialisation procedure.
Error 93
If, during the initialisation procedure, the display shows the
massage
Er93
, this means the SLAVE motor is connected with
incorrect polarity.
Check the SLAVE motor connection and repeat the initialisation
procedure.
Error 94
If, during the initialisation procedure, the control unit fails to
detect the presence of the SLAVE motor, but the operator has
indicated this to be present, the display shows the message
Er94
Check the SLAVE motor connection and repeat the initialisation
procedure.
Summary of Contents for ZORUS
Page 2: ...165 306 250 62 46...
Page 33: ...ENGLISH 65...
Page 36: ...ENGLISH 68...
Page 37: ......
Page 38: ......