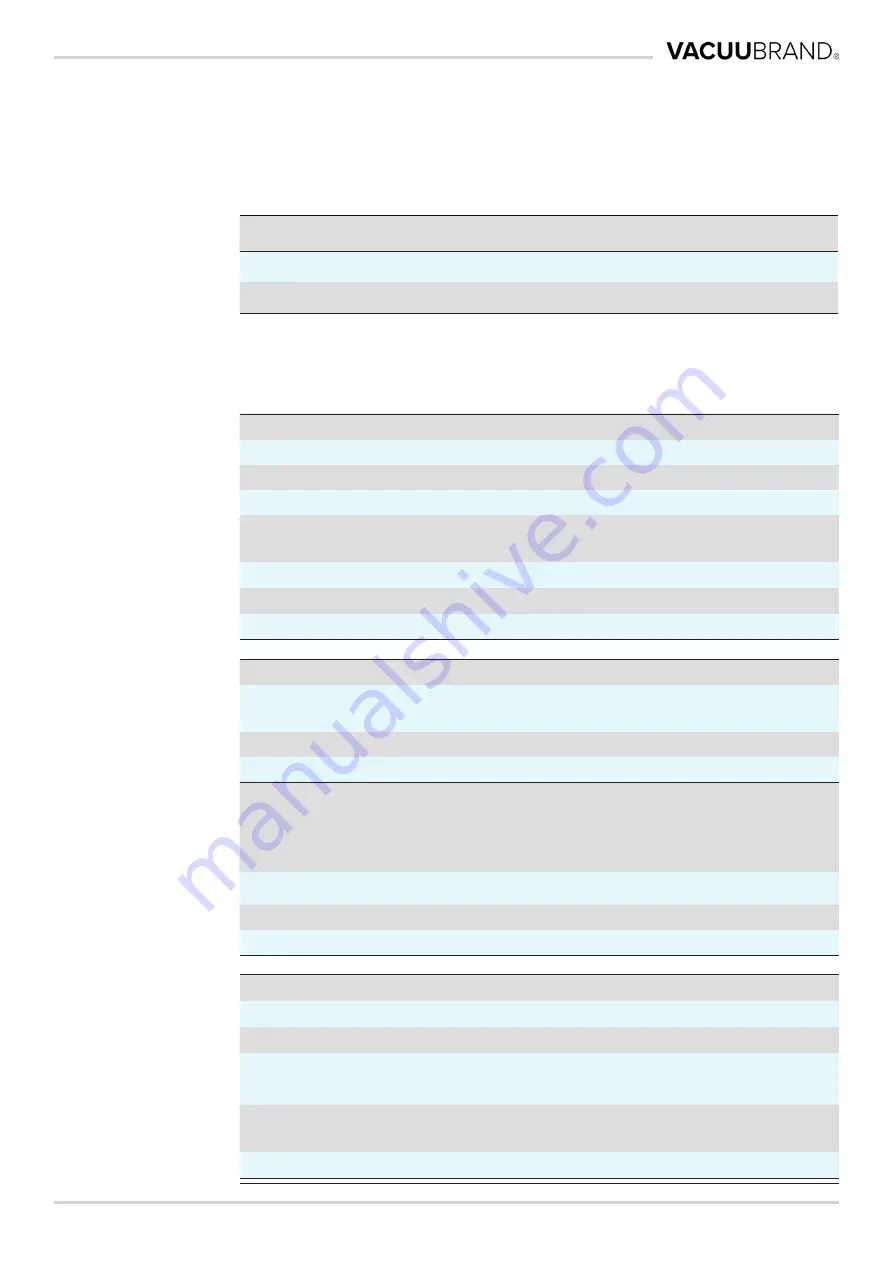
78
20901544_E12C+16C_NT Vsel_V1.2_260922
Appendix
8
8 Appendix
Appendix
8.1
8.1 Technical information
Technical information
Chemistry diaphragm pump series
ME 16C VARIO NT select
MD 12C NT VARIO select
MV 10C NT VARIO select
8.1.1
8.1.1 Technical data
Technical data
Ambient conditions
(US)
Ambient temperature, max.
10
–
40 °C
50‑104 °F
Working temperature
10‑40 °C
50‑104 °F
Storage/transport temperature
‑10‑60 °C
14‑140 °F
Max. altitude
2000 m
above sea level
6562 ft
above sea level
Relative humidity
30‑85 %, non‑condensing
Pollution degree
2
Protection class
IP 40 / IK 08
Operating conditions
(US)
Maximum admissible media temperature (gas), non‑explosive atmo
‑
sphere:
Short term
80 °C
176 °F
Continuous operation
40 °C
104 °F
ATEX approval if the ATEX
marking is shown on the rating
plate
Inner part (pumped gases)
II 3/‑ G Ex h IIC T3 Gc X
Internal Atm. only
Tech.File: VAC‑EX02
Maximum admissible media temperature (gas),
`
atmosphere:
Short term
(< 5 minutes)
40 °C
104 °F
Continuous operation
40 °C
104 °F
Connections
Vacuum, inlet
Small flange KF DN 25
Gas ballast GB
Gas ballast valve, manual
Inert gas adapter – OPTION
Small flange GB NT KF DN 16
Hose nozzle GB NT DN 6/10
Venting valve (venting with in
‑
ert gas) – OPTION
Silicone rubber hose 3/6
Exhaust gas, outlet EX
Hose nozzle DN 15
Technical data