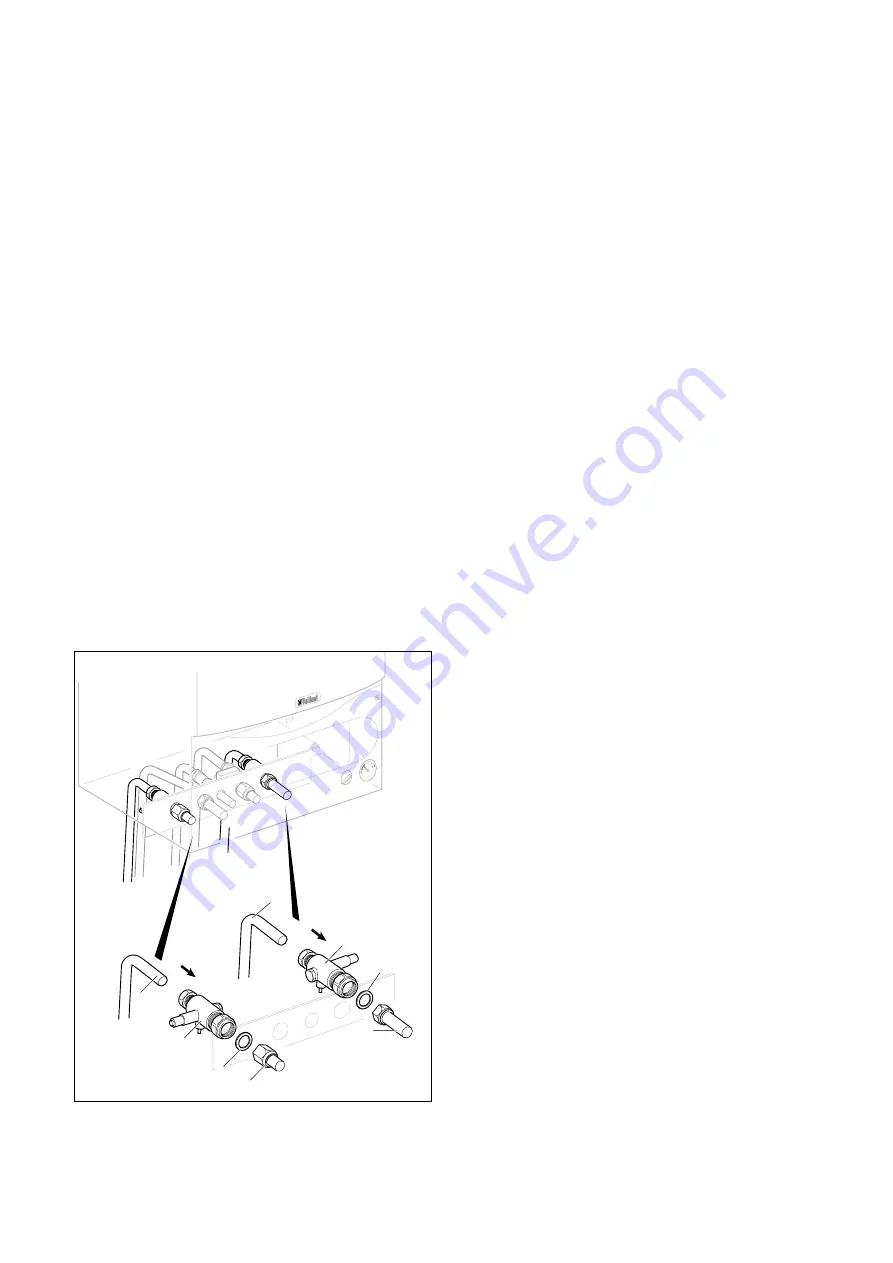
Boiler Installation Sequence 5
Instructions for installation and servicing aquaPLUS VUI 362-7
17
5.9 Central heating flow and return pipework
Before connecting the heating circuit to the boiler
appliance, all pipework and radiators must be
thoroughly flushed to remove any installation debris.
• Connect the central heating flow (6) and return (1)
service valves to the appliance (8 and 3) with the
washers provided (2 and 7) and tighten the nuts.
Ensure that the valve spindles face downwards and
the drain points face to either side of the boiler.
• Connect the 22 mm copper pipe tails to the service
valves as shown in the illustration and tighten the
nuts.
• Connect the central heating pipework to the flow (9)
and return (4) tails.
Pressure Relief Valves (central heating and domestic
hot water)
Connect discharge pipes not less than 15 mm diameter
to the outlet of these valves.
The discharge pipework should be as short as possible
and installed with a continuous fall away from the boiler.
The pipes should terminate in a position which ensures
that any discharge of water or steam from the valves
cannot create a hazard to persons in or about the
premises, or cause damage to any electrical
components or external wiring, and the point of
discharge should be safe and clearly visible.
Fig. 5.8: Central heating flow and return pipework aquaPLUS
I
0
9
1
2
8
7
6
3
4
5.10 Connect the flue system to the boiler
• Refer to separate air/flue duct installation instructions
included with the boiler.
Supplied by HeatingSpares247.com