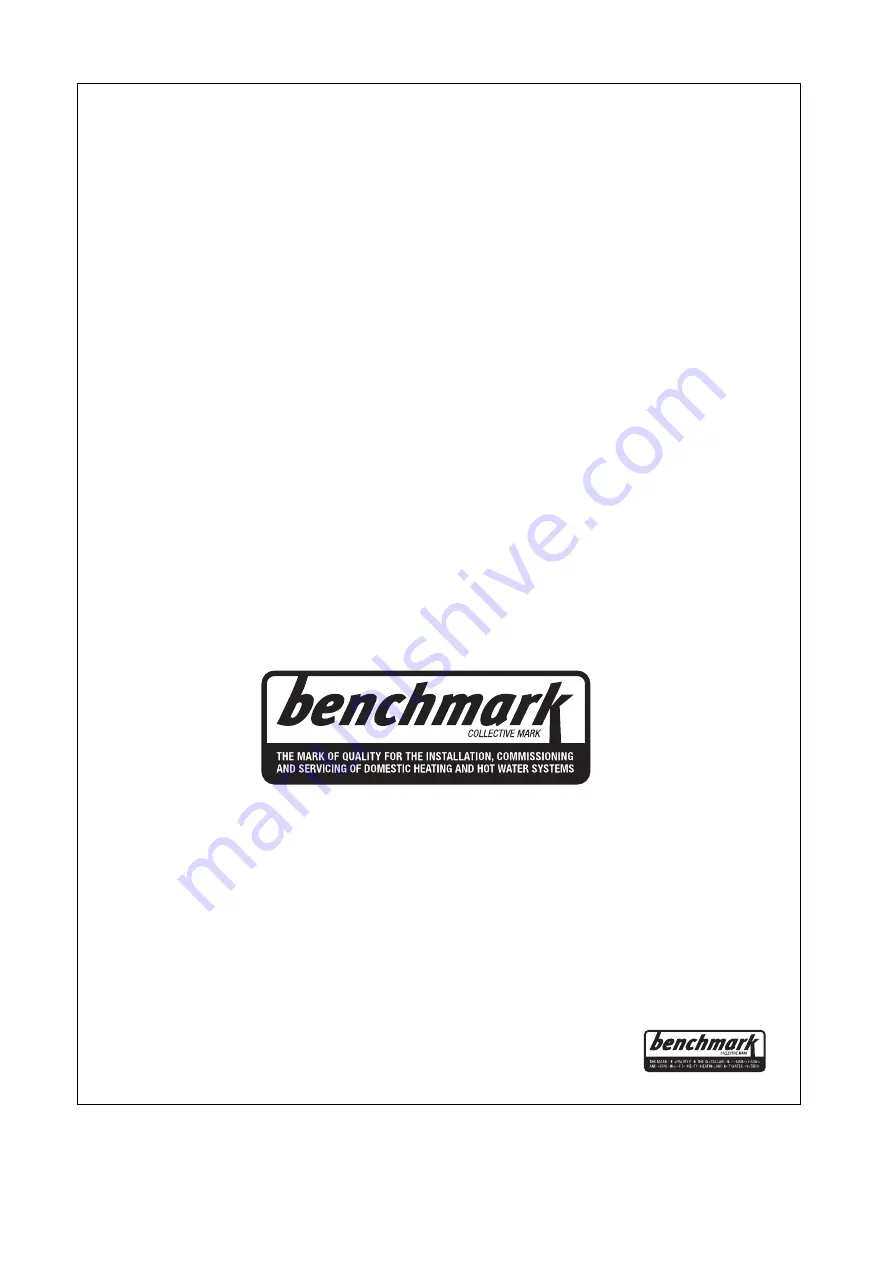
58
Installation and maintenance instructions ecoTEC exclusive 0020193966_04
I
Commissioning Checklist
© Heating and Hotwater Industry Council (HHIC)
www.centralheating.co.uk
* All installations in England and Wales must be notified to Local Authority Building Control (LABC) either directly or through a
Competent Persons Scheme. A Building Regulations Compliance Certificate will then be issued to the customer.
www.hhic.co.uk
Benchmark Commissioning &
Warranty Validation Service Record
It is a requirement that the boiler is installed and commissioned to the manufacturers’
instructions and the data fields on the commissioning checklist completed in full.
To instigate the boiler warranty the boiler needs to be registered with the
manufacturer within one month of the installation. The warranty rests with the
end-user (consumer), and they should be made aware it is ultimately their
responsibility to register with the manufacturer, within the allotted time period.
It is essential that the boiler is serviced in line with the manufacturers’
recommendations, at least annually. This must be carried out by a competent Gas
Safe registered engineer. The service details should be recorded on the Benchmark
Service and Interim Boiler Work Record and left with the householder. Failure to
comply with the manufacturers’ servicing instructions and requirements will invalidate
the warranty.
This Commissioning Checklist is to be completed in full by the competent person who commissioned the boiler as a means of demonstrating
compliance with the appropriate Building Regulations and then handed to the customer to keep for future reference.
Failure to install and commission according to the manufacturers’ instructions and complete this Benchmark Commissioning Checklist will invalidate the
warranty. This does not affect the customer’s statutory rights.