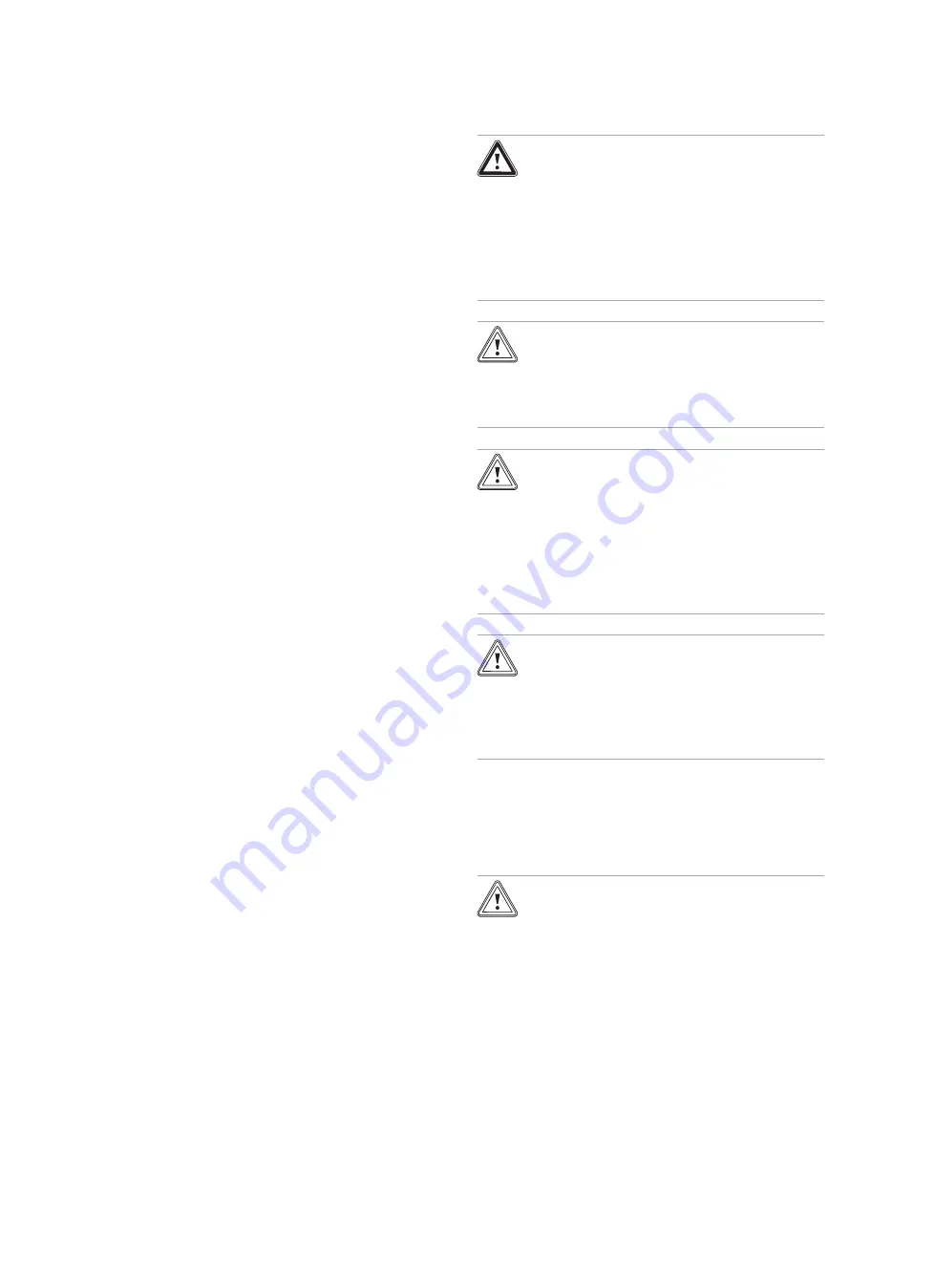
5 Installation
14
Installation and maintenance instructions ecoTEC plus 0020261188_00
Wiring diagram (
→
Page 47)
5.4
Requirements
▶
Make sure that the existing gas meter is capable of
passing the rate of gas supply required. (
→
Page 53)
▶
If the hydraulic circuit contains a pump other than the one
for the product, only start up the product if a sufficiently
dimensioned low loss header is installed between the
heat generator circuit and the heating circuit or the cylin-
der charging circuit.
Low loss header (
→
Page 13)
▶
If the product's pump is the only circulation pump in the
hydraulic circuit, check whether the product's feed head
is sufficient for the installation. (
→
Page 27)
▽
If this is not the case, use an appropriately designed
low loss header and circulation pump.
▶
Ensure that the installation has the following compon-
ents:
–
A gas stopcock for the unit
–
A filling/draining device in the heating installation
▶
With older installations in particular, install a magnetic
filter at the heating circuit return in order to protect the
product against dirt from the installation.
–
Ensure that there is sufficient dimensioning in order
to prevent it from blocking quickly and to prevent high
pressure losses.
5.4.1
Information on liquefied petroleum gas
operation
In the as-delivered condition, the product is preset for opera-
tion with the gas group indicated on the data plate.
If you have a product that has been preset for operation with
natural gas, you must convert it to run on liquid gas. You will
need a conversion set for this. The conversion procedure is
described in the manual supplied with the conversion set.
5.4.2
Purging the liquid gas tank
If the liquid gas tank is not purged properly, this may result in
ignition problems.
▶
Ensure that the liquid gas tank has been purged properly
before installing the product.
▶
If required, contact the filler or the liquid gas supplier.
5.4.3
Using the correct gas type
Using the incorrect gas type may cause fault shutdowns in
the product. Ignition and combustion noise may occur in the
product.
▶
Only use the gas type listed on the data plate.
5.5
Connecting gas and water
Danger!
Risk of explosion or scalding caused by
incorrect installation.
Mechanical stresses in the connection pipes
may lead to leaks.
▶
Make sure that the connection pipes are
free from mechanical stress when they
are installed.
Caution.
Risk of material damage due to heat trans-
fer during soldering.
▶
Only solder connectors if the connectors
are not yet screwed to the service valves.
Caution.
Risk of material damage caused by
residues in the pipelines.
Welding remnants, sealing residues, dirt or
other residues in the pipelines may damage
the product.
▶
Flush the heating installation thoroughly
before installing the product.
Caution.
Risk of material damage caused by
changes to the pipes that have already
been connected.
▶
Only bend connection pipes if they have
not yet been connected to the product.
Seals made of rubber-like materials may be subject to plastic
deformation, which can lead to pressure losses.
▶
Use fibre seals.
5.5.1
Gas connection
Caution.
Risk of material damage due to the gas
leak-tightness test.
At a test pressure of >11 kPa (110 mbar), gas
leak-tightness tests may cause damage to
the gas valve assembly.
▶
If, during gas leak-tightness tests, you
also place the gas pipes and the gas valve
assembly in the product under pressure,
use a max. test pressure of 11 kPa
(110 mbar).
▶
If you cannot limit the test pressure to
11 kPa (110 mbar), close any gas stop-
cocks that are installed upstream from the