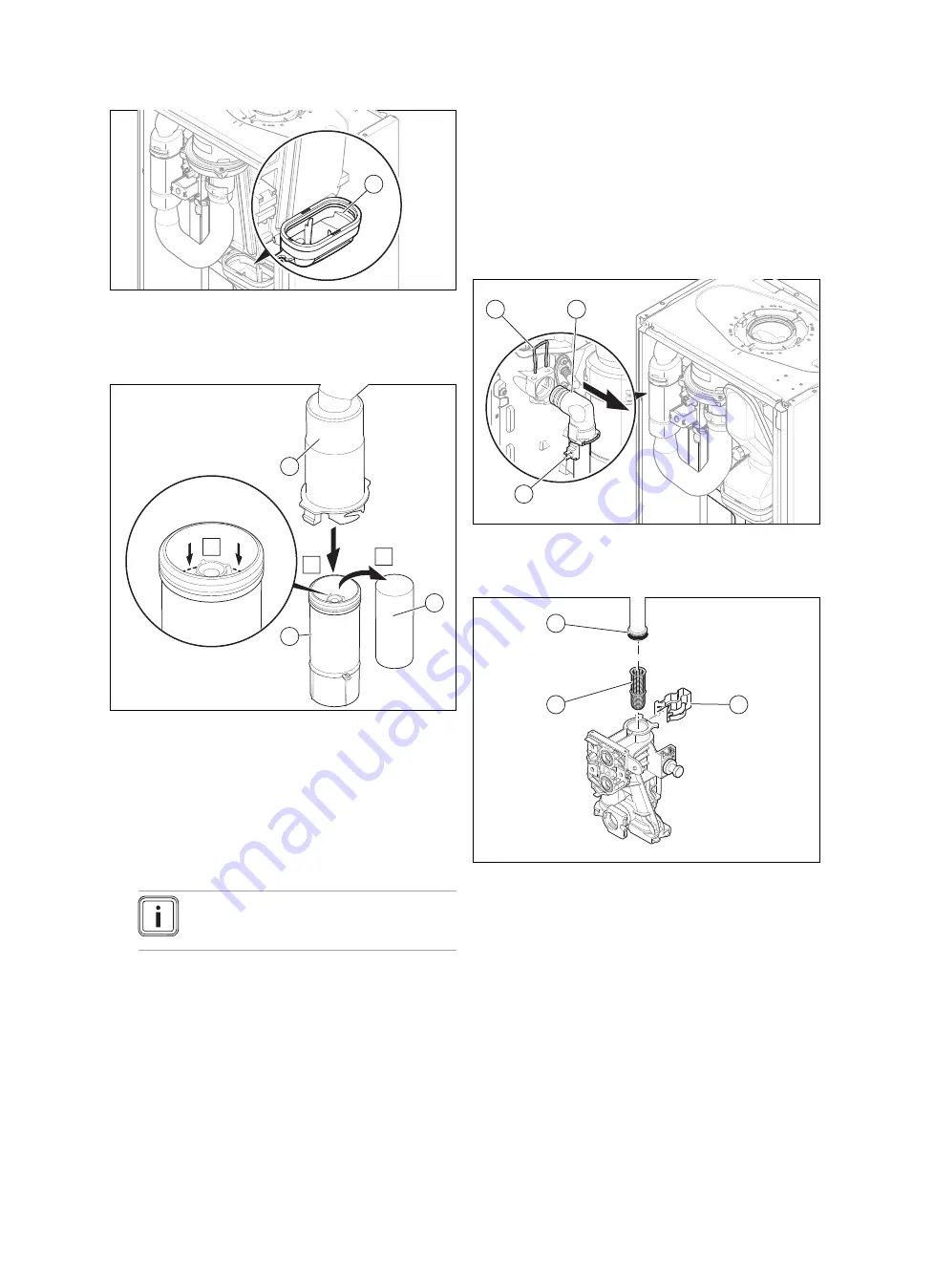
Inspection and maintenance 11
0020224355_00 HOME Installation and maintenance instructions
25
1
5.
Using water to clean the condensate tray
(1)
.
◁
The water runs out into the condensate siphon.
11.10 Cleaning the condensate siphon
C
2
3
1
A
B
1.
Unclip the lower section of the siphon
(1)
from the up-
per section of the siphon
(2)
.
2.
Remove the float
(3)
.
3.
Flush out the float and lower section of the siphon with
water.
4.
Fill the lower section of the siphon with water up to 10
mm below the upper edge of the condensate drain pipe-
work.
5.
Reinsert the float
(3)
.
Note
Check whether the float is present in the
condensate siphon.
6.
Clip the lower section of the siphon
(1)
into the upper
section of the siphon
(2)
.
11.11 Cleaning the filter in the cold water inlet
1.
Close the main cold water supply line.
2.
Drain the product on the hot water side.
3.
Remove the connection piece from the connection for
the product's cold water supply.
4.
Clean the filter in the cold water inlet without removing
it.
11.12 Cleaning the heating filter
1
3
2
1.
Drain the product. (
→
Page 26)
2.
Remove the temperature sensor
(3)
.
3.
Remove the upper clip
(1)
.
3
2
4
4.
Remove the lower clip
(2)
.
5.
Remove the supply pipe
(3)
.
6.
Remove the heating filter
(4)
and clean it.
7.
Reinstall the components in the reverse order.
Summary of Contents for home combi
Page 51: ......