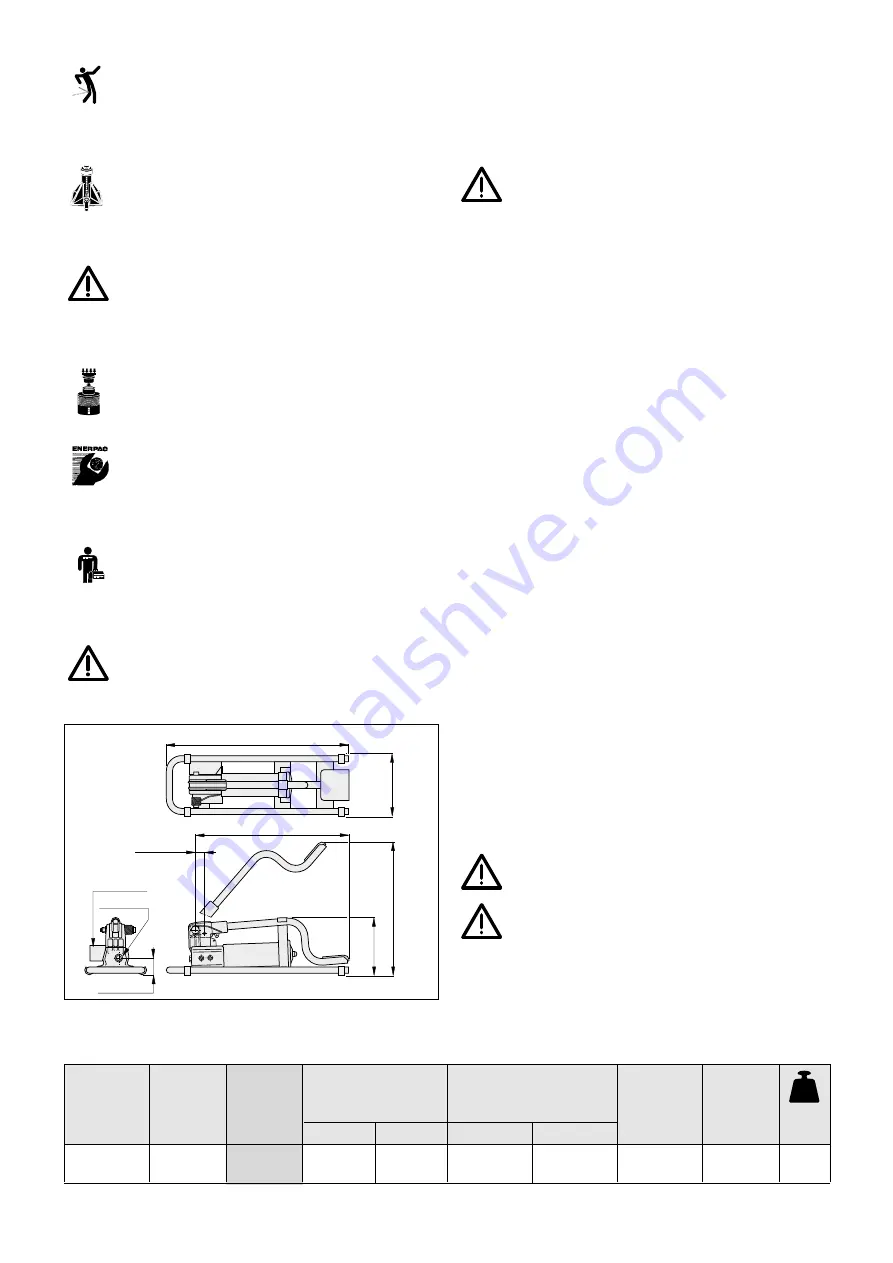
2
WARNING: Only use hydraulic cylinders in a coupled
system. Never use a cylinder with unconnected
couplers. If the cylinder becomes extremely
overloaded, components can fail catastrophically causing
severe personal injury.
WARNING: BE SURE SETUP IS STABLE BEFORE
LIFTING LOAD. Cylinders should be placed on a flat
surface that can support the load. Where applicable,
use a cylinder base for added stability. Do not weld or
otherwise modify the cylinder to attach a base or other
support.
Avoid situations where loads are not directly centered
on the cylinder plunger. Off-center loads produce
considerable strain on cylinders and plungers. In
addition, the load may slip or fall, causing potentially
dangerous results.
Distribute the load evenly across the entire saddle
surface. Always use a saddle to protect the plunger.
IMPORTANT: Hydraulic equipment must only be
serviced by a qualified hydraulic technician. For repair
service, contact the Authorized ENERPAC Service
Center in your area. To protect your warranty, use only
ENERPAC oil.
WARNING: Immediately replace worn or damaged
parts by genuine ENERPAC parts. Standard grade
parts will break causing personal injury and property
damage. ENERPAC parts are designed to fit properly and
withstand high loads.
CAUTION: Always use the handle to carry the pump.
Carrying the pump by the hose may damage the hose
and/or the pump.
3.0 DESCRIPTION
The P-392FP is a two-speed pump which can be used to
power single-acting cylinders and tools with an oil capacity up
to 490 cm3. It has an internal pressure relief valve for overload
protection. For dimensions see Figure 1. Figure 2 shows the
specifications of the pump.
WARNING: The P-392FP is operated with a non-
vented reservoir. If the reservoir is subjected to
high pressure, the casing may rupture, causing
personal injury and/or equipment damage. NEVER
attempt to return more oil to the reservoir than it is
capable of holding.
4.0 INSTALLATION
4.1 Connecting the Pump
1. Thread hose into pump outlet. Use 1 1/2 wraps of Teflon tape
(or suitable thread sealant) on hose fitting, leaving the first
complete thread free of tape to ensure that tape does not
shed into hydraulic system, causing damage. Trim loose
ends.
2. Install a pressure gauge in-line from the pump for added
safety and better control.
3. Connect the hose(s) to your cylinder or tool.
NOTE:
For single-acting cylinders, connect one hose from
the pump to the cylinder. For double-acting cylinders,
connect two hoses. Connect one hose from the pressure
port of the pump to the pressure port of the cylinder.
Connect another hose from the retract port of the pump to
the retract port of the cylinder.
4.2 Pump Venting
The P-392FP is operated with a non-vented reservoir. If the
reservoir is subjected to high pressure, the casing may
rupture, causing personal injury and/or equipment damage.
NEVER attempt to return more oil to the reservoir than it is
capable of holding.
5.0 OPERATION
5.1 Before Using the Pump
1. Check all system fittings and connections to be sure they
are tight and leak free.
2. Check oil level in reservoir before operating pump. See
paragraph 7.1 "Adding Oil to the Pump" on page 3.
CAUTION: NEVER add extensions to pump handle.
Extensions cause unstable pump operation.
WARNING: In certain situations the pump handle
can "kick back". Always keep your body to the side
of the pump, away from the line of force of the
handle.
NOTE: To reduce handle effort at high pressure, take short
strokes. Maximum leverage is obtained in the last 5° of stroke.
®
187 [7.36"]
52 [2.04"]
3/8"-18NPT
433 [17.05"]
193 [7.60"]
600 mm [23.6 inch]
504 [19.8"]
30 [1.18"]
Release valve
FIGURE 2 - SPECIFICATIONS
Figure 1
Single-
Acting
Usable Oil
Capacity
cm
3
[in
3
]
Used
with
cylinder
Pressure Rating
bar [psi]
Model
Number
Oil Displacement
per Stroke
cm
3
[in
3
]
Max.
Handle
Effort
kg
[lbs]
Piston
Stroke
mm
[inch]
1st stage 1st stage
2nd stage
2nd stage
kg
[lbs]
492
[30]
15
[220]
700
[10,000]
11,26
[.687]
2,47
[.151]
42
[93]
25,4
1.00
7,0
[15.4]
P-392FP