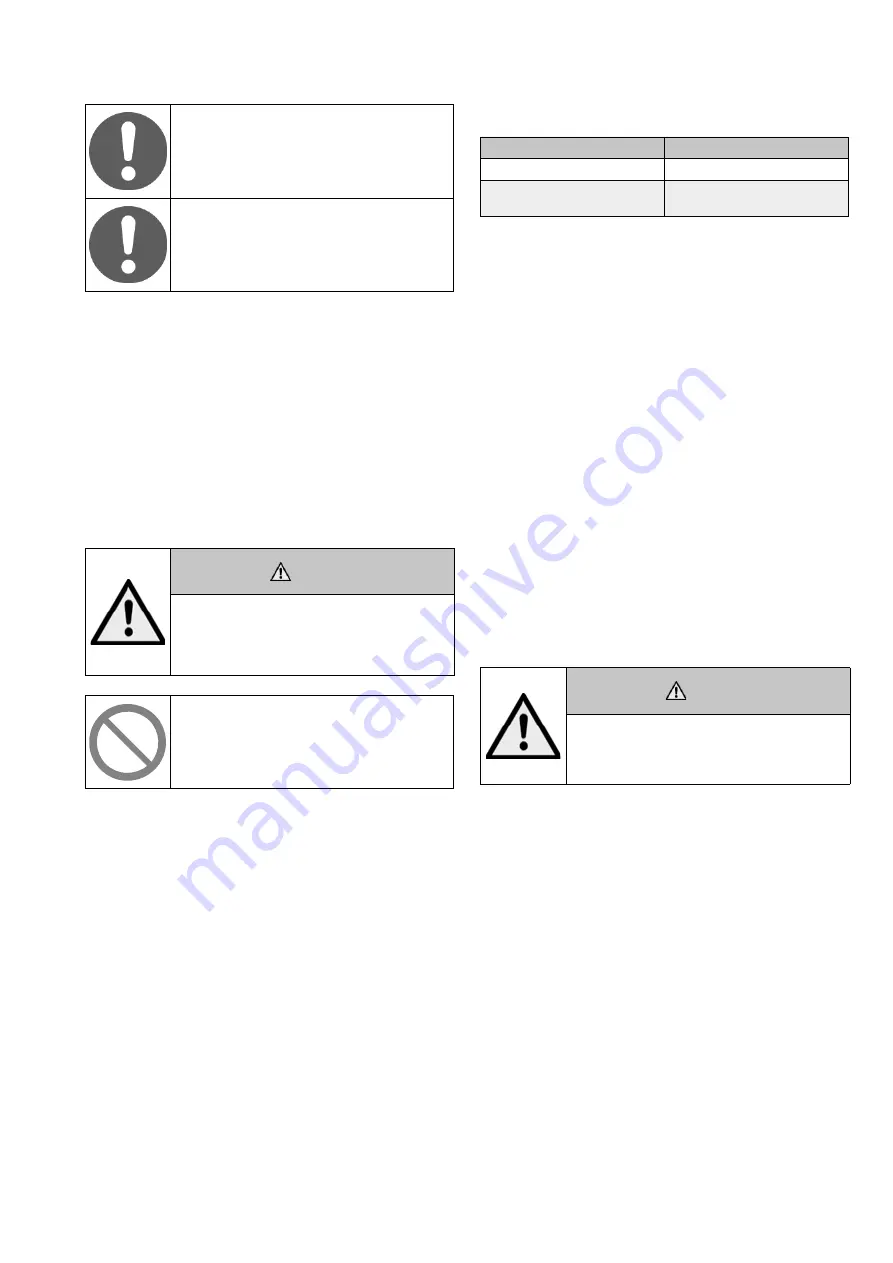
11
4EXP70EN - 9/2023
The maximum filling air pressure for the dampener
is 6 bar (0,6 MPa).
In case the process pipeline pressure is changed readjust
the dampener pressure.
When a dampener is decommissioned, dispose the parts
according to the local regulations and the instructions given
by the part or device manufacturer.
Collect and dispose dangerous process media, so that people
and environment are not endangered. Follow the local
regulations.
Servicing and Maintenance
6.2 General maintenance and checks
WARNING!
High pressure injection hazard.
Isolate the dampener completely from the process,
depressurise and drain it before changing the hoses.
Follow the factory safety regulations.
Do not step on the dampener installed in horizontal or
angled position.
Only personnel with appropriate training are allowed to
service the dampeners.
Check the condition of the dampener regularly. When the
dampener actuates flawlessly, periodic inspection is the only
mandatory maintenance task. Do not neglect it as hoses wear
over time depending on conditions and process.
Scheduled maintenance
Include the dampeners in your factory maintenance program.
Maintenance tasks and service intervals are offered as a
guideline in Table 4. Schedules will vary with applications.
Table 4.
Maintenance schedule.
Maintenance task
Frequency & advice
Check the dampener pressure.
Every month.
Check the dampener doesn’t hit
anything and there’s no leakage.
Every month.
Spare parts
To ensure correct and quick delivery of spare parts, the order
must contain the following information:
• Dampener type number as in type plate (example:
FPD65-10-0-2-NR)
• Spare part name and quantity (example: Damping Hose,
1 piece)
You can order the spare parts from Valmet's Flow Control
offices, distributors or agents. Contact information is available
at https://contact.neles.com/
It is recommended to keep 1 set of hoses and clamps as spare
parts at your factory warehouse. For part numbers refer to
figures 1 and 2.
6.3 Changing the hoses
To change the hoses, the dampener needs to be removed
from the pipeline. Part numbers refer to
Figures 1 and 2.
WARNING!
High pressure injection hazard.
Do not disconnect a pressurized dampener from the
pipeline for any reason.
Removing the hoses
1. Shut down the pump and lock it to OFF position.
2. Depressurise and drain the pipeline according to factory
specific orders.
3. Depressurise the dampener with the valve (part 7) on the
hose flange.
4. Loosen the flange connections and lift the dampener
to a suitable working surface. Use lifting equipment on
dampeners weighing over 25kg.
Summary of Contents for Flowrox Expulse Series
Page 17: ...17 4EXP70EN 9 2023...
Page 18: ...4EXP70EN 9 2023 18...
Page 19: ...19 4EXP70EN 9 2023...