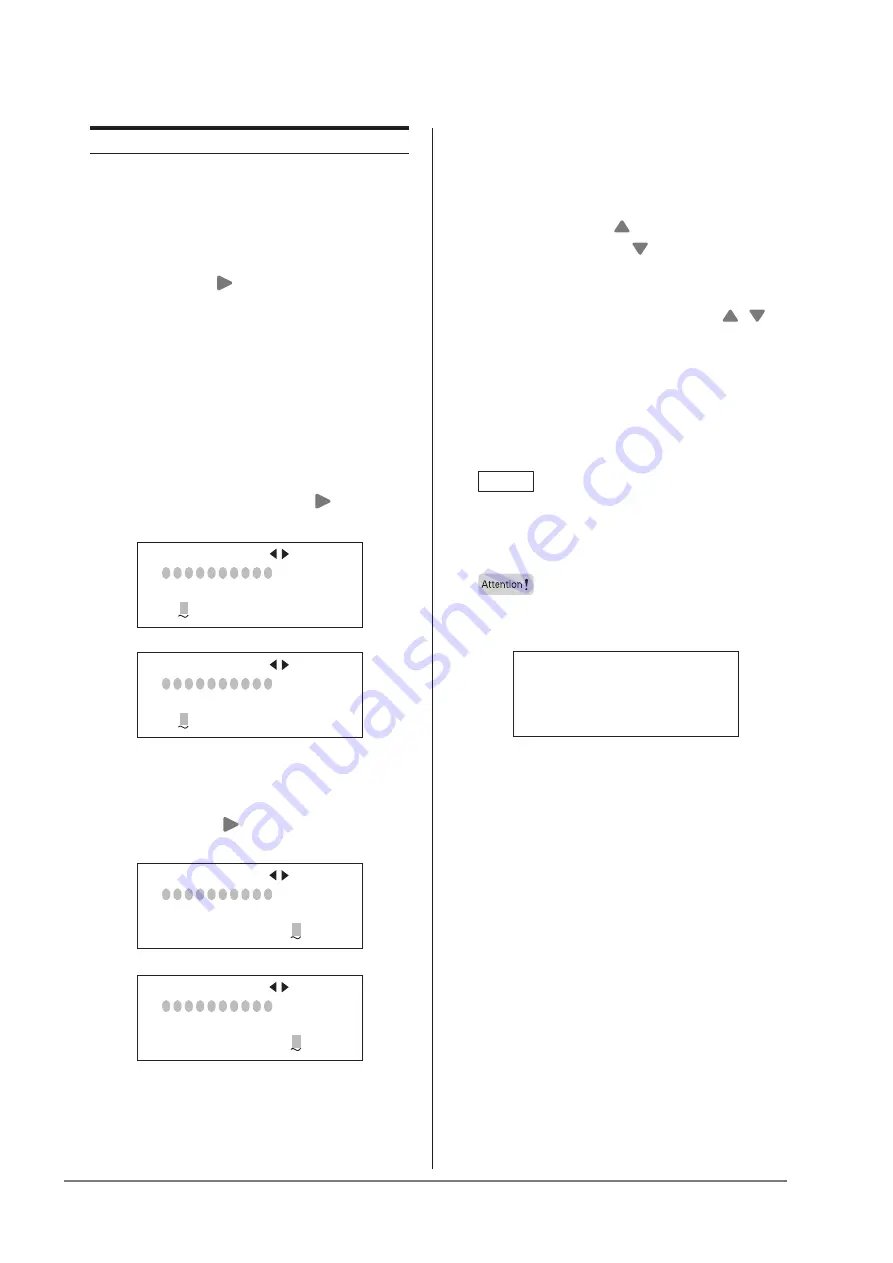
V-460/610 Series Operating Instructions Ver.2.04E
36
[ 0
x
]▼▲Dec/Inc Move
HT
xx
O
C
x
.
x
s CT
xx
O
C
(
The mark “
〜
” under the cursor indicates it is blinking.
)
[ 0
x
]▼▲Dec/Inc Move
HT
xx
O
F
x
.
x
s CT
xx
O
F
(
The mark “
〜
” under the cursor indicates it is blinking.
)
[ 0
x
]▼▲Dec/Inc Move
HT
xx
O
C
x
.
x
s CT
xx
O
C
(
The mark “
〜
” under the cursor indicates it is blinking.
)
[ 0
x
]▼▲Dec/Inc Move
HT
xx
O
F
x
.
x
s CT
xx
O
F
(
The mark “
〜
” under the cursor indicates it is blinking.
)
WARNING!
COOL TEMP IS TOO
HIGH.
SET COOL TEMP LOWER.
8-4-7 Set cooling temperature
1
■
How to change cooling temperature
of the currently displayed operation
pattern:
>> Press the button. The below display
will be shown on the screen.
-----> Go to procedure 2.
■
How to change heating time of the
operation pattern NOT currently
displayed:
>> Refer to
“8-4-2 Select the desired
operation number.”
After selecting the
desired number, press the button and
go to procedure
2
.
2
The cursor will blink at the first digit of
“HT.” Press to move the cursor to the
first digit of cooling temperature.
When the cursor is at this position, adjust
the cooling temperature by pressing:
Ɣ8SEXWWRQ
to increase the value.
Ɣ'RZQEXWWRQ
to decrease the value.
7KHYDOXHZLOOLQFUHDVHRUGHFUHDVHLQÛ&
RUÛ)LQFUHPHQWE\SUHVVLQJWKH
/
button once. If you hold the button in, the
numeric value will increase or decrease
continuously. Use this method when
making wide range changes in setting.
>6HWWLQJUDQJHÛ&Û)aXSWRWKHVHW
heating temperature]
TIPS
If cooling temperature is set extremely
high, the strong and beautiful seal
cannot be made.
Please set the sufficient cooling
temperature for your film.
Attention
When cooling temperature is set too
high, the following warning is displayed
on the screen for 4 seconds.
Summary of Contents for V-460 Series
Page 61: ...V 460 610 Series Operating Instructions Ver 2 04E 61 ...
Page 66: ...V 460 610 Series Operating Instructions Ver 2 04E 66 12 Electric diagram 110V ...
Page 67: ...V 460 610 Series Operating Instructions Ver 2 04E 67 220V ...
Page 68: ...V 460 610 Series Operating Instructions Ver 2 04E 68 13 Piping diagram V 460 610 series ...
Page 69: ...V 460 610 Series Operating Instructions Ver 2 04E 69 V 460 610C series ...
Page 75: ...V 460 610 Series Operating Instructions Ver 2 04E 75 ...