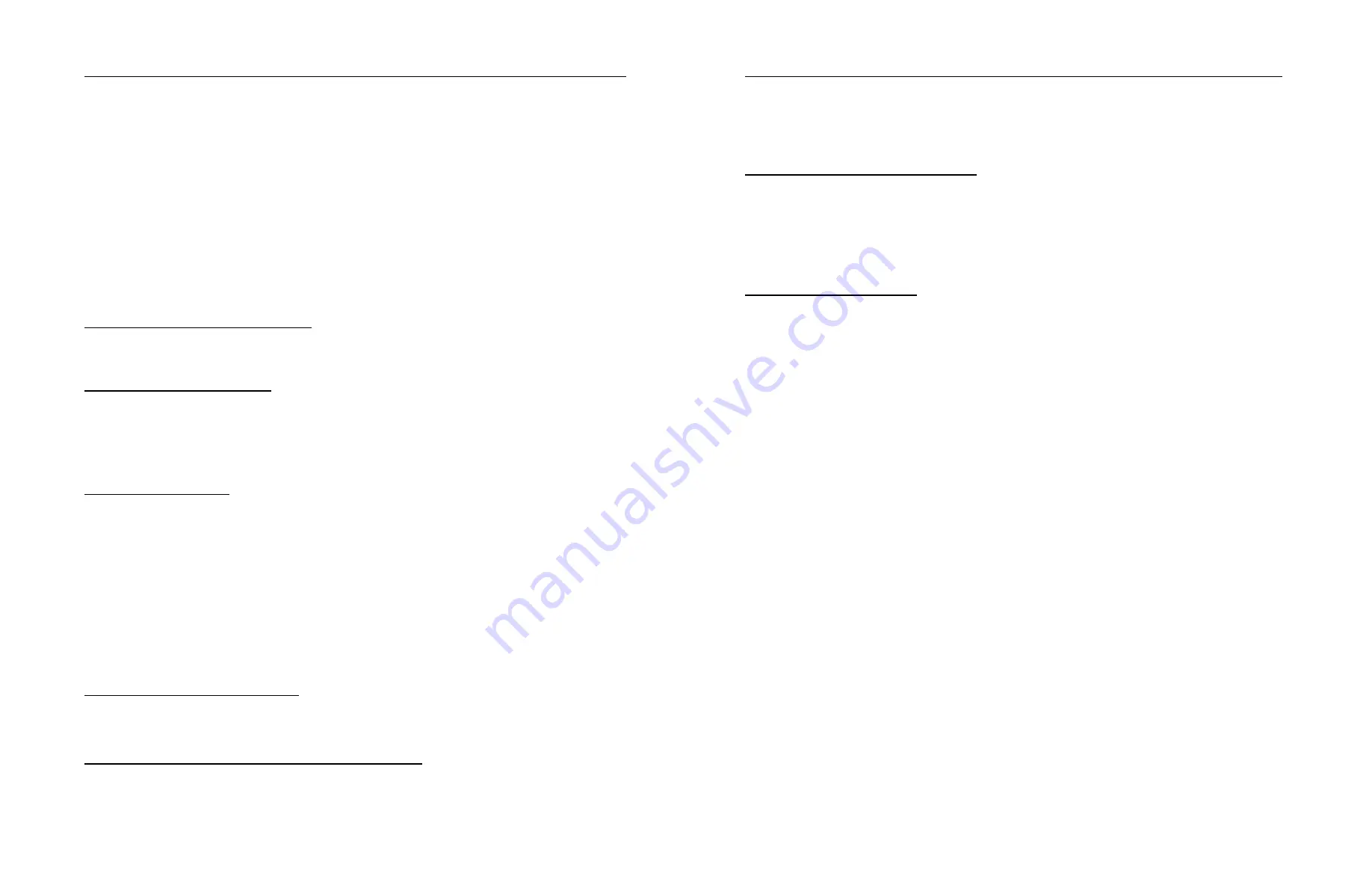
SECTION 7
RV-8/8A
7-9
8s7-1r11 06/13/11
Dimple the ribs with a hand squeezer. The 0.063 main spar channel is too thick to dimple so it is machine
countersunk. Make another 0.032 test patch with a #40 dimple, and use it to adjust your micro stop until the
countersink in the spar is just deep enough.
Dimple the 0.040 rear spar and “touch up" the dimpled holes slightly with a sharp deburring bit or microstop
countersink. This "touch up" operation removes just a small amount of metal to make the skin dimple fit better and is
not critical, so it can be done by eye. Use your test patch to test the depth. The usual tendency is to remove too
much metal, so use a light touch.
Drill the W-423 splice plates for installation of the platenuts. Deburr all holes. Dimple the screw holes and the rivet
holes for the rib and the platenut attachment. The holes for attaching to the rib and skin can be slightly reamed (like
the rear spar) to gain a better fit between the skin, the splice plate, and the rib.
Cleco the main skins to the wing skeleton. The skins overlap, outboard skin over inboard. This means that the
doubled skins will protrude above the aft edge of the tank skin at the spar. File the corners of these skins, starting at
a point 3 or 4 inches from the corner, making each of them progressively thinner toward the edge. This will form a
sort of “scarf joint” and lower the forward edge, making a clean joint with the tank skin. It is NOT necessary to scarf
the whole width of the skin, just the corner.
This is the point of no return; the point where things start going together permanently. Make a close inspection to
assure everything is clean and proper before continuing.
ASSEMBLING THE WING LEADING EDGE
Rivet the Leading Edge Assembly by fitting the skin into the cradle and then clecoing in the ribs and the W-423
splice plate. After making sure that the holes at the aft end of the ribs are exactly aligned, rivet the aft most rivets on
the top and bottom using a rivet squeezer. Finish the riveting by working from the rear towards the L.E. one hole at a time.
INSTALLING THE LEADING EDGE
Install the leading edge assembly on the wing skeleton. While the main skins are off, there is room to reach in and
rivet the rib flanges to the spar web. This will require an offset rivet set. Remember the outboard W-709 and W-712
ribs are both riveted together in assembly with the W-706A spar web. After riveting the ribs to the spar, rivet the
spanwise row of rivets, top and bottom, along the main spar web, using a rivet squeezer.
Install the fuel tank on the wing, with screws in every other hole, top, bottom and around the leading edge. Install
about half the bolts in the Z-brackets.
RIVETING THE TOP SKINS
With the outboard leading edge riveted in place and the tank installed it is time to rivet the top main skins. While it is
possible for one person to install the first set of main skins, it is much easier with two. Rivet the W-702 inboard skins
first, because the outboard skins overlap them.
Begin by clecoing the inboard skin in position (wing walk doublers, too) and start riveting. To assure maximum skin
tightness, rivet from the center rib of each skin outward towards the root and tip. Do this on both the inboard and
outboard skins, saving the double row of rivets at the lap joint until last.
Many builders find that they can get a nicer skin finish (especially when they are using less experienced helpers) if
they back-rivet the wing skins. Use a large bucking bar laid over the rivet on the outside of the skin, and drive the
head on the rivet from the inside using an extended back-rivet set available from some suppliers.
When the top main and leading edge skins are riveted on, remove the wing from the stand and put it on a padded
worktable, top down. Block the wing so it doesn't rock around on the table.
If you are installing leading edge landing lights (p/n LL DW-01 in Van's Accessories Catalog) it is easiest to do it
now, before the bottom skins are permanently installed.
INSTALLING THE AILERON BRACKETS
Assemble the W-413 and W-414 Aileron bracket assemblies as shown on DWG 10A. Install them on the rear spar
by lining up the matched holes, drilling, deburring, and riveting.
INSTALLING THE FLAP BRACE AND AILERON GAP FAIRINGS
Drill, deburr, dimple where required, and rivet the W-721 flap brace (DWG 14A) to the rear spar.
RV-8/8A
SECTION 7
7-10
8s7-1r11 06/13/11
QUICKBUILDER’S NOTE
:
The W-721 must be attached to the rear spar with blind rivets. See the note on DWG
14A, Section B-B’.
Drill the W-724 aileron gap fairing (DWG 13A) to the rear spar. Drill, deburr, and dimple where required, and rivet
the W-724 aileron gap fairing to the rear spar.
INSTALLING THE PITOT LINE AND WIRES
Install the pitot line and fittings shown on DWG 15A. Install SB437-4 snap bushings in the 7/16" holes for the Pilot line in W-
710 and W-711. Put the low profile face of the bushing on the flange side of the rib, to ease access to the skin rivets later.
Complete the stall warning assembly instructions OP46-04 Steps 1-7 and OP46-05 Steps 1-6. Complete OP46-06
Steps 1-7 when installing the electrical system.
Double check that you have done everything else inside the wing that you wish to do such as installing wiring for
wing tip lights, installing a wing leveler servo, etc., before closing up the wing. If you have not decided on some of
these items, riveting the bottom skins can wait until much later in the project.
RIVETING THE BOTTOM SKINS
The bottom skins are riveted while the wing lies top down on the bench. Begin with the inboard skin and rivet it to
the rear spar, between the inboard wing walk ribs. This means pulling the skin back until you can reach the rear
spar with a bucking bar. While it is possible for one person to rivet the bottom skins working solo if they use some
sort of tape/rope/clamp system to peel the skin back, many builders find the job easier with a helper.
Be careful when pulling the skin back. If you try to bend it too sharply, you will get an unsightly, and irreparable, kink.
Work in an “L” pattern, riveting toward the tip along the rear spar, then about halfway up the wing rib. Before the
skin is riveted all the way to the main spar, move to the next bay and repeat the process. After the second bay is
partially riveted, complete the first. Riveting gets much easier as you move forward, because of the improved
access through the larger holes in the ribs and the inspection openings. Once the inboard skin is riveted, the
outboard is installed the same way, beginning on the inboard rib and working toward the tip. Leave the inboard line
of rivets that joins the two skins only (no rib) until last. Those rivets can be reached through the access holes.
Lay the skin back down after every bay or so and check to see that all the holes in the skin and the skeleton still
align and that the skin is not “creeping” outboard.
Drill the access panels to the bottom of the wing. Install the platenuts in the wing skin as shown in Section A-A', DWG 17A.
AILERONS
The construction technique for RV-8/8A ailerons (DWG 13A) is similar to that of the elevators. The aileron uses ribs
at the ends only; light angle stiffeners support the rest of the skin. The A-710 skin stiffeners are provided with the
rivet holes pre-punched but not cut to length. The aileron skin is punched to match. These are match-drilled much
like the stiffeners in the empennage. Cut and trim the stiffeners as shown on the drawing. Locate the stiffeners on
the inside of the A-801-1PP rear aileron skin and drill.
Dimple the stiffener angles and skin. After priming (if desired), rivet the stiffeners onto the skin, preferably using the
backriveting method described in Section . Following this, complete the trailing edge bend using the homemade
bending brake used on the empennage. The bent skins must be straight up to the radius and the radius must be
between 3/32” to 1/8”. Match the degree of bend to the full size end view drawings. The upper and lower skin
should just touch the spar when placed in position.
The A-403PP aileron spar is not symmetrical; the top and bottom flanges are bent to different angles. Check and
label each spar for top, bottom, inboard and outboard. Make the A-408 aileron spar reinforcement brackets from
supplied .040” material. Match-drill using spar holes as a guide and cleco as you go. Cleco the A-406-1 and A-407
aileron brackets in place and drill #12 for attach bolts. Label the parts, disassemble, deburr & prime as desired.
Making sure that you leave the holes that will later attach the ribs empty, rivet the A-408 aileron spar reinforcement
brackets on the spar along with the K1000-3 plate nut.
The wide tabs on the top of the A-704 nose ribs have no pre-punched holes, they will be match drilled from the nose
skin. Flute the center of the tab slightly to remove any distortion from the manufacturing process. Use the nose
skin holes as a check for straightness. Cleco and match drill the nose ribs to the spar.
Look closely! The A-705 aileron ribs are NOT symmetrical, so be sure you have them installed correctly. The
tooling holes are nearer the bottom of the aileron. Cleco and match drill the A-705 main ribs to the spar.
Cleco the A-802PP leading edge skin and the A-801-1PP trailing edge skin to the spar with the A-409