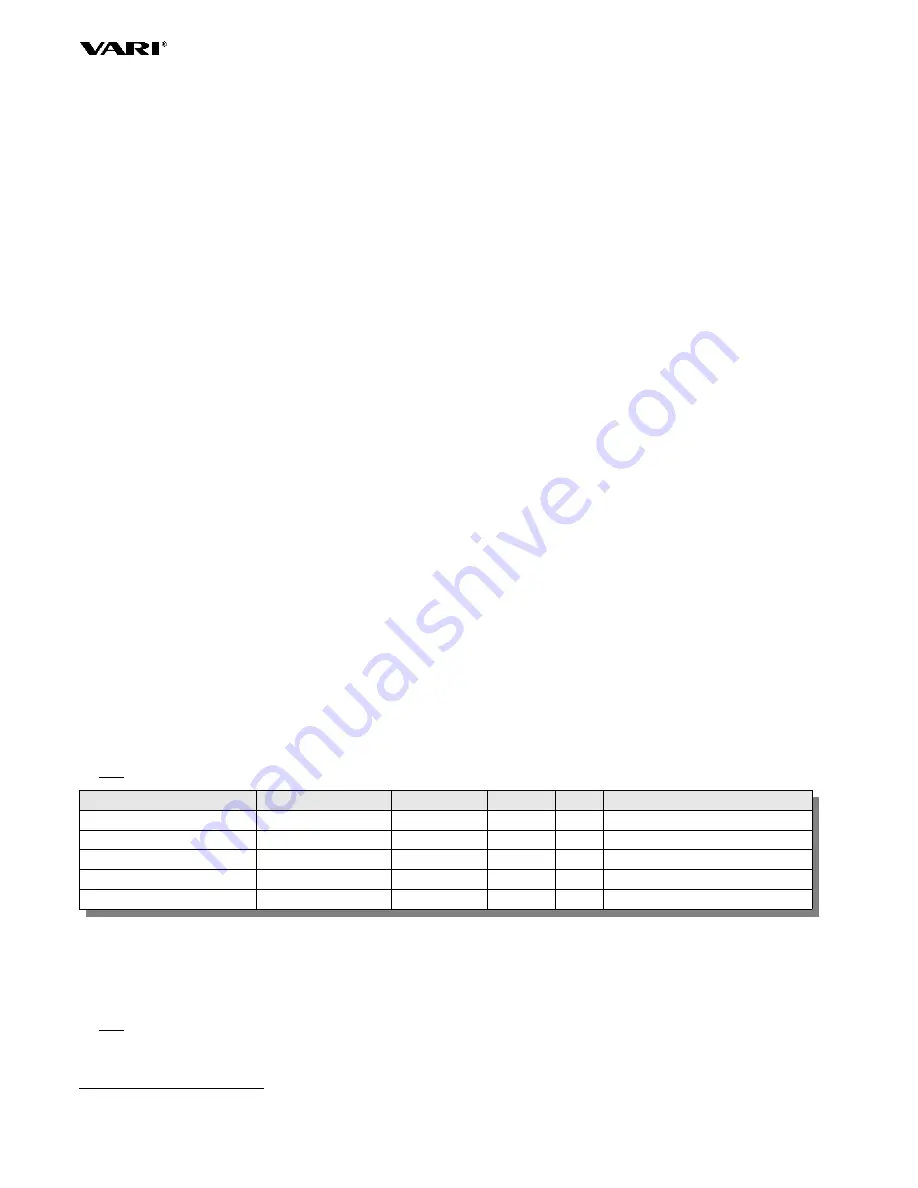
3.
The cut brushes keeps catching on the side screen
(because the stand is too thick).
➢
Stop the cutter and turn the engine off. Dismount the side screen and put it in a safe place, out of the cut area, so that it cannot be stolen.
2.5 Maintenance, servicing and storage
The weight of the cutter requires two persons for carrying out its maintenance and adjustment.
In order to be happy with our product in the long-term, it is necessary to give it adequate maintenance and servicing care. Regular maintenance reduces
deterioration and ensures proper functioning.
Follow all instructions concerning maintenance and adjustment schedule. It is recommended that you keep a record of the amount of its working time and
conditions (for service needs). It is recommended to let one of our authorised service centres take care of the after-season maintenance, as well as regular maintenance
if you are not sure about your technical skills.
Check the nuts tightening the upper disc blades and nuts tightening the lower disc to the flange before each cutter use.
2.5.1 Travelling wheels
Travelling wheels create an important part of the cutter. Wheels carry the whole weight of the cutter, transfer engine power, and push the cutter into mesh.
Wheels have tyre tubes, which can be easily removed, in case of a defect, due to split rims connected with several bolts.
2.5.1.1 Tyre pressure
Tyre pressure has to be controlled in order to secure proper functioning and long life of the wheels, especially the tyres. Check the pressure before you start
using the cutter. Fill the pressure to
MAX
before putting the cutter out of service for a longer period of time. Keep equal pressure in right and left wheels - it helps
the cutter to keep a straight track.
Do not exceed the maximum tyre pressure – you risk a tyre explosion!
➢
MAX
imum (
recommended
) tyre pressure:
23 PSI
(
160 kPa
or
1,6 bar
or
1,57 atm
or
0,16 MPa
)
➢
MIN
imum
50
allowed tyre pressure:
18 PSI (124,1 kPa
or
1,24 bar
or
1,22 atm
or
0,124 MPa)
In case of permanent tyre pressure release, check and repair possible tyre defect.
Seek authorised service in case you lack appropriate manual skills.
2.5.2 Machine lubrication
Follow basic hygienic rules and environmental laws when working with lubricants.
Seek authorised service in case you lack appropriate manual skills.
Smooth and easy movement of all mechanical parts requires adequate lubrication. Several drops of oil are usually sufficient (e.g. Bicycle oil). The gearbox is
filled with sufficient amount of oil during manufacturing and it does not require filling during the whole machine life.
2.5.2.1 Engine oil exchange
Follow the engine user manual instructions. If you use the cutter in a dusty environment, shorten the exchange period by half. When pouring the oil out of the
engine tilt the cutter on its filler and oil dipstick side or dismantle the whole engine.
Seek authorised service in case you lack appropriate manual skills.
2.5.2.2 Lubricating points
There is no need to dismount any covers from the machine when lubricating the cables on the handlebars. You can reach other lubricating points after dismounting
the plastic covers. You can use any kind of engine, transmission or spray oil. Any kind of lubricant grease for water pumps is fully sufficient. For its application,
however, it is usually necessary to dismantle the appropriate sliding sealing.
Note:
When using graphite grease, the seasonal lubrication intervals can be extended up to
25 hours
.
Lubricating point – description
Seasonal interval
After the season
Lubricant
Picture
Note
Bowden cables
min 2x (5 drops)
yes
oil
Pict.9
Cable entrance into cable housing
Disc drive pulley casing
every 10 hours (2 drops)
yes
oil/grease
Pict.6
After nut and washer dismounting.
Wheel drive clutch pulley
every 10 hours (2 drops)
yes
oil/grease
Pict.7
Contact area with frame.
Cam
every 10 hours (2 drops)
yes
oil
Pict.8
Bolted connections
-
yes
grease
-
Handlebars and side screen attachment
Tab. 5: Lubricating intervals
2.5.3 Work blades service and exchange
Seek authorised service in case you lack appropriate manual skills.
If the work blades are deteriorated or damaged and causing cutter vibrations, it is necessary to renew or exchange the blades
51
.
Note:
he manufacturer bears no responsibility for damages caused by/on the cutter in case of a botched-up blades repair or when original parts are not used. A
sign identifying the manufacturer is imprinted in the blade and it is used as a proof of a genuine part.
The cutter must be secured from unexpected spontaneous movement and stand on a safe pad to allow adequate access to the blade.
50
Tyre pressure lower than minimum damages the tyre construction and shortens its life.
51
The blades are double-sided; they can be turned around if necessary. The blades must never be damaged.
20
Summary of Contents for BDR-620
Page 2: ......
Page 13: ...BDR 620 BDR 620B 13...
Page 14: ...14...
Page 25: ...BDR 620 BDR 620B 25...
Page 26: ...26...
Page 35: ...BDR 620 BDR 620B 3 5 5 10 2x 5 5 5 20 6 3 5 6 7 35...
Page 38: ...38...
Page 39: ...40...
Page 50: ...BDR 620 BDR 620B 51...
Page 51: ...52...
Page 56: ......
Page 57: ......
Page 58: ......