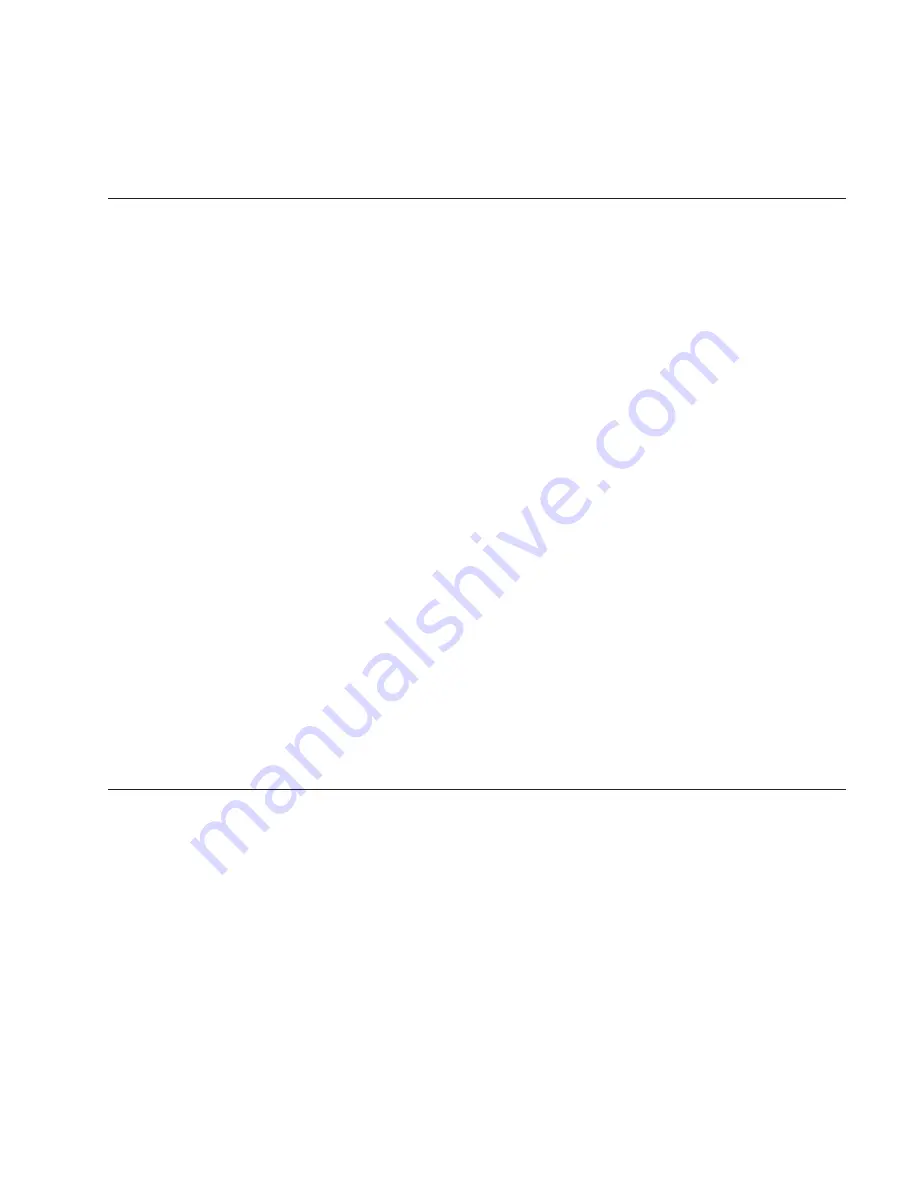
v
Prohibited Action
Explosion-Causing Condition
Open drain or fill plug while pump is
Overpressure plus strong oxidizer
under vacuum, especially when it is hot
Contaminate pump with explosive vapors,
Lower explosive threshold of gas mixtures
powders, or reactive materials
Remove, defeat, or override safety counter-
Overtemperature, overpressure, more
measures such as pressure and thermal
combustible mixtures
switches and valve sequencer interlocks
Machine or weld without removing all oil
Source of ignition
or solvent residue in pump
Use unsuitable pumping fluid especially
Lower explosive threshold of gas mixture
in large pumps
Systems larger than 10 inches must be designed with pressure relief devices to provide safe pres-
sure relief from internal explosions. Always recognize that safety devices can fail or malfunction. Pro-
vide redundant protection by installing devices having different failure modes, failure mechanisms,
and failure causes. Be certain that exhaust duct materials are capable of withstanding the corrosivity,
temperature, and pressure of exhausted products.
c. Pressure – Pumps and their components are designed for vacuum service; they are not designed
to be pressurized which could cause them to burst possibly expelling shrapnel at lethal velocities.
Serious accidents have been caused by intentional pressurization of vacuum systems and their
components. Never pressurize any part of a vacuum system for test or any other purpose.
Always provide pressure relief when designing diffusion pumps into systems and ensure that pres-
sure relief motion is limited to safe envelopes. Never permit the following:
Prohibited Action
Result
Block inlet and vent of liquid nitrogen
LN
2
trap and/or lines burst
trap and lines
Close isolation valves at inlet and discharge
Water turns to steam and bursts coils
of main watercooling coils and pump is
reheated
Pressurize pump body
Body of pump bursts
Hole through vacuum wall
Loss of structural integrity of wall
Summary of Contents for VHS-6
Page 27: ...Replacement Parts 5 2 ...
Page 28: ...Replacement Parts 5 3 ...