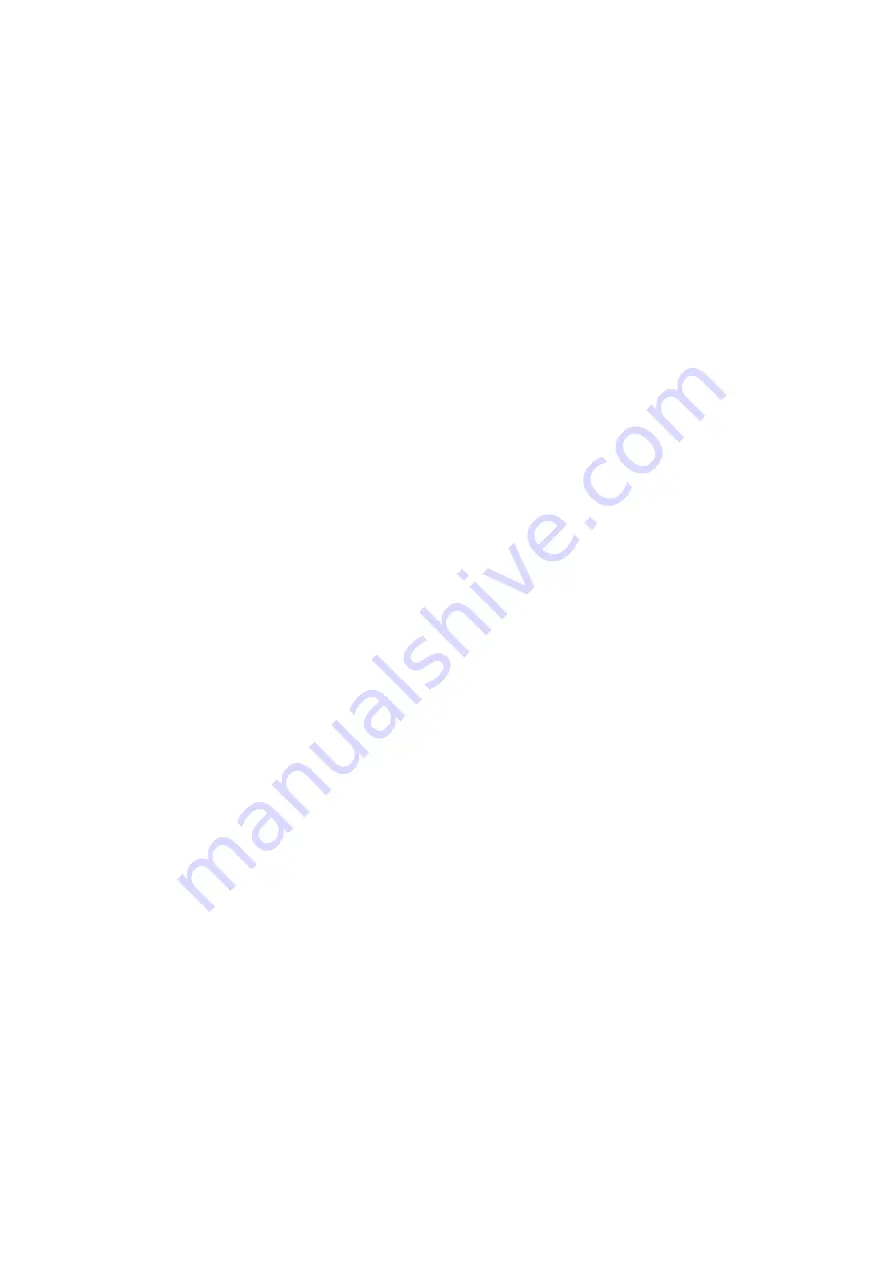
7 cutwater (leading edge of the volute) is worn
remove pump casing as indicated in section 13.2. Build up the cutwater with weld and shape it to restore the original profile. If cutwater
is severely worn, replace the casing.
8 suction strainer, where applicable, may be clogged
remove obstructions.
9 excessive suction lift
reduce suction lift.
10 air entering through seal
disassemble seal and clean it (see sect. 13.6); if the problem persists, change the seal.
11 impeller clogged by foreign matter
check state of impeller through the inspection cover (26) (fig. 9), or remove the pump casing as described in section 13.2.
14.2 PUMP DOES NOT DELIVER LIQUID
12 pump does not prime
see causes given in point 14.1.
13 head required by the system is greater than the rated head of the pump
revise system design or select a different pump.
14 excessive flow resistance along suction line
revise distribution of elbows, valves, constrictions etc. ; where necessary, increase diameter of pipework.
15 impeller clogged by foreign matter
check state of impeller through the inspection cover (26) (fig. 9), or remove the pump casing as described in section 13.2.
16 suction/delivery pipes may be obstructed or clogged
locate the obstructed or clogged area and clean.
14.3 THE PUMP DOES NOT DELIVER ENOUGH LIQUID
17 air leaks in suction line
check joints are airtight and inspect suction pipe.
18 impeller and/or wear plate may be worn
replace them by disassembling the pump as described in sections (13.2; 13.3, 13.4).
19 diameter of the suction pipe too small
replace suction pipe.
14.4 THE PUMP DOES NOT PROVIDE ENOUGH PRESSURE
20 viscosity of the liquid is higher than expected
contact VARISCO once you have measured the viscosity of the liquid. Viscosity for centrifugal pumps should not exceed 50 cSt.
Check for other possible causes: see point 5 in section 14.1, and section 14.2.
14.5 THE PUMP ABSORBS TOO MUCH POWER
21 rotation speed too high
check correct rotation speed.
22 pump operates under conditions that are different from those specified in the contract
check operating conditions of pump and compare them to those on the pump’s nameplate.
23 density of the liquid is higher than expected
measure density of the liquid and compare it with the agreed value.
24 incorrect unit alignment
check unit is correctly aligned as described in section 10.
25 there may be friction inside the pump between rotating and non-rotating components
disassemble pump casing as described in section 13.2 and check for scratches on surfaces.
26 foreign matter in impeller
check state of impeller through the inspection cover (26) (fig. 9), or remove the pump casing as described in section 13.2.
14.6 THE PUMP VIBRATES AND IS NOISY
27 pump is operating with a flow rate that is too low
check settings of the valves in the system and readings on the pressure and vacuum gauges.
28 pump or pipework is not fixed securely
make sure system pipework is correctly clamped.
29 pump cavitates
see section 14.2
Check possible causes: see section 14.1.
30 foreign matter in impeller
check state of impeller through the inspection cover (26) (fig. 9), or remove the pump casing as described in section 13.2.
14.7 THE PUMP JAMS
31 mechanical breakdown
check shaft, couplings, motor or engine, pulleys and belts, gearboxes etc. for breakages.
32 foreign matter in impeller
check state of impeller through the inspection cover (26) (fig. 9), or remove the pump casing as described in section 13.2.
11