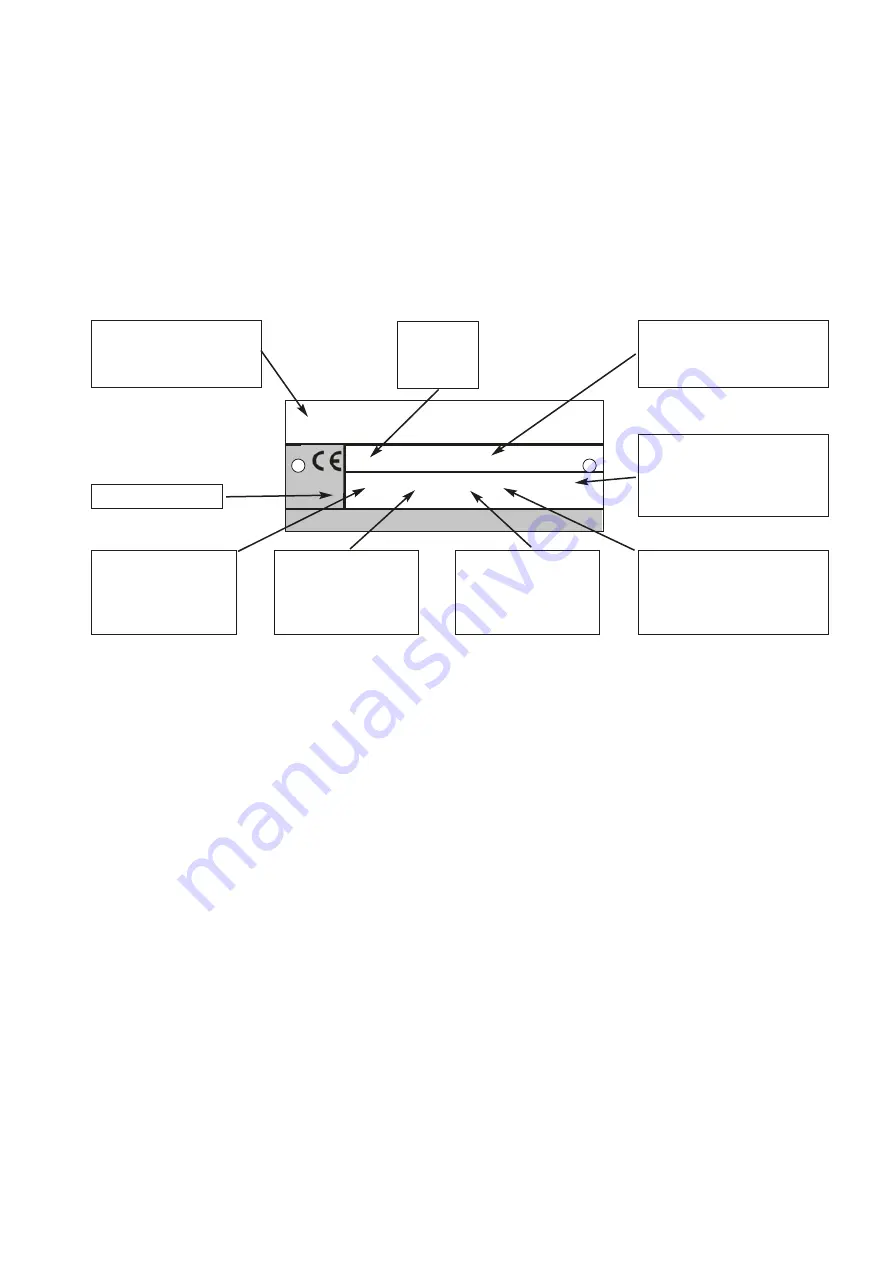
1
IDENTIFICATION
1.1
Manufacturer
VARISCO S.p.A. - Terza Strada, 9 - Zona Ind. Nord - 35129 PADOVA - ITALY
1.2
Type of pump
Horizontal self-priming centrifugal pump with open impeller for handling liquids containing solids in suspension. These pumps can operate
satisfactorily with liquids containing air or dissolved gases.
1.3
Model
The model is given on the pump nameplate.
1.4
Year of manufacture
The year of manufacture is given on the pump nameplate.
1.5
Instruction book identification
Edition 2001
Rev.: 01
Code 400
1.6
Nameplate information
Ratings refer to testing with water at 20°C and with a density of 1,000 kg/m
3
1.7
Field of application
Pumps are suitable for handling liquids of viscosity up to 50 cSt containing solids in suspension. They are used in industry, civil engineering,
shipbuilding, waste water treatment, construction and agriculture.
1.8
In case of breakdown
Call the following number:
+39 049 82 94 111
2
WARRANTY
-
VARISCO S.p.A. warrants that only top-quality materials are used in the construction of their pumps and that machining and assembly are
carried out to high standards.
-
The company also warrants units supplied, in conformity with general terms of sale, against defective materials or faulty workmanship for
a period of one year from the material's date of delivery unless specifically stated otherwise in writing.
- The warranty is not valid if the unit has been tampered with by third parties.
-
Replacement of parts or of the unit itself can only be carried out after careful examination in an authorized workshop by qualified
personnel. The unit should be sent carriage paid.
-
This warranty does not cover materials subject to deterioration or normal wear and tear (seals, diaphragms, pressure and vacuum gauges,
rubber or plastic items, etc.), electrical material, or damage caused by misuse or improper handling of the unit by the end user.
-
Materials replaced under warranty become the property of VARISCO S.p.A..
3
GENERAL INSTRUCTIONS
The goods must be examined on arrival to ascertain any damage, particularly that incurred in transit. Also check that the goods correspond
exactly to the description on the transport documents. Any damage or differences must be reported to the forwarding agent straight away
on the transport document, and reported to the Manufacturer by means of registered letter with advice of delivery within seven days, or
they will not be acknowledged. Always quote the pump type printed on the relevant nameplate, or the serial number.
The pumps must be used only for applications for which the Manufacturer has specified:
- construction materials
- operating conditions (pressure, speed, temperature, etc.)
- fields of application
For any applications not contemplated by the Manufacturer, contact VARISCO S.p.A.'s Servicing Department - Tel.
+39 049 82 94 111
TYPE
indicates the model of the
pump and/or pump unit
TYPE
MATR.
ITEM
m
3
/h (max)
m (max)
kW
RPM (max)
kg
MATR.
this is the
pump serial
number
ITEM
this is the number with which the
pump is associated in the agreement
documents (not always indicated)
kg
this is the weight of the pump
and/or pump unit, not including
the weight of water in the pump
casing and diesel fuel in the tank
Year of manufacture
m
3
/h
(max)
this is the pump's
maximum flow rate,
measured at top speed
(rpm)
m
(max)
this is the pump's
maximum working
pressure, measured at
top speed (rpm)
kW
this is the maximum
power that can be
applied to the pump at
top speed (rpm)
RPM
(max)
this is the pump's maximum
operating speed. The pump
must
never
be allowed to exceed this
speed
4