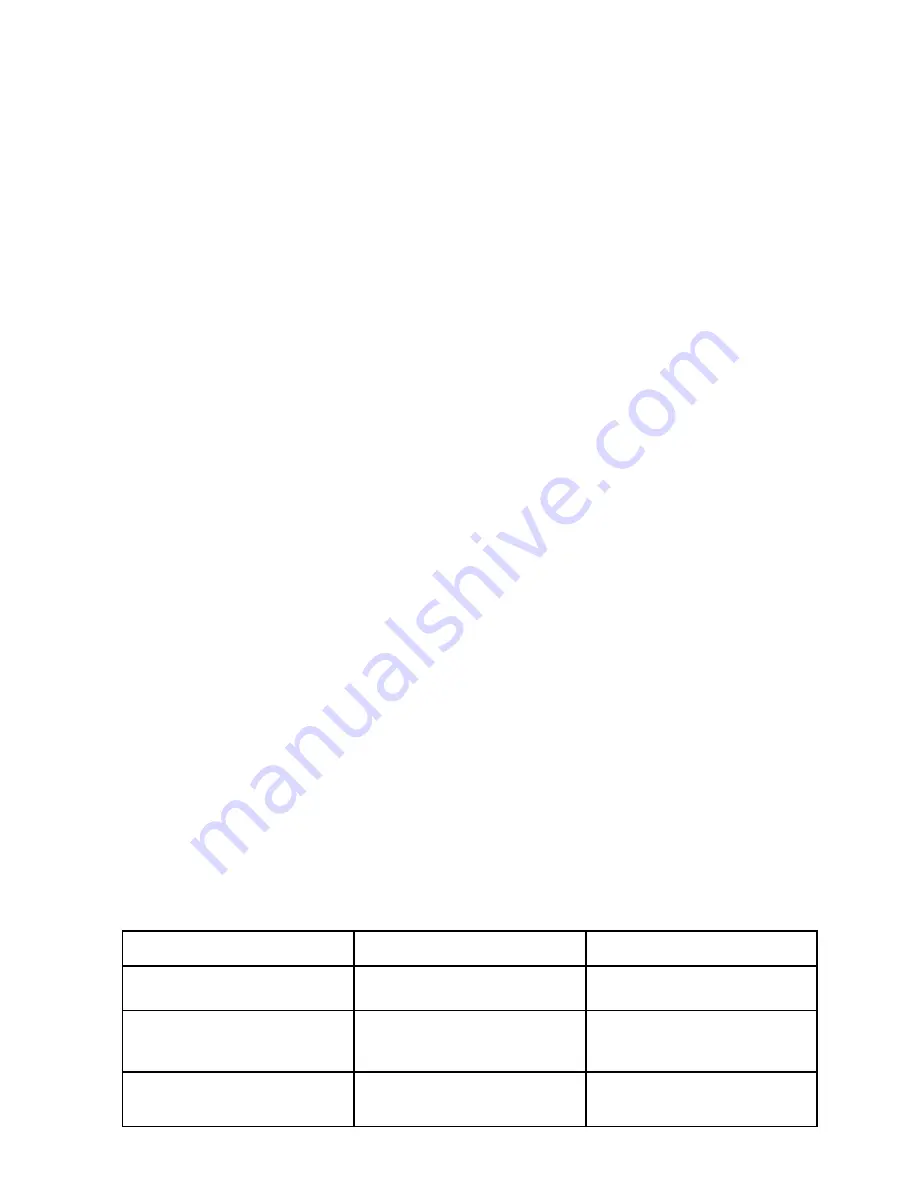
Stability during use, transportation, assembly, testing, and foreseeable breakdowns:
The D-100 and D-1000 dryers are designed and expected to be inherently stable under all foreseea-
ble conditions of use, assembly, testing, etc., so long as the procedures listed in this manual are fol-
lowed. Be certain that your workbench, table, or stand can safely support the weight of your ma-
Safe handling, transport, and storage:
Unplug your dryer and allow it to cool before storing. When handling or transporting your machin-
ery, be aware of the following weights and dimensions:
D-100: Assembled — 89 lbs (40.4 kg); 46” x 24” x 24” (119 x 61 x 61 cm)
Boxes: #1 – 57 lbs (25.9 kg); #2 – 14 lbs (6.4 kg); #3 – 18 lbs (8.2 kg); Boxes on skid: 115 lbs
(52.2 kg)
D-1000: Assembled — 116 lbs (52.6 kg), 46” x 32” x 24” (119 x 81 x 61 cm)
Boxes: #1 – 38 lbs (17.2 kg); #2 – 43 lbs (19.5 kg); #3 – 35 lbs (15.9 kg); Boxes on skid: 137 lbs
(62.1 kg)
Adjustment and Maintenance:
In the event of a malfunction or breakdown:
Safety during adjustment and maintenance
Before beginning any maintenance or adjustment procedures on your dryer:
If the machine’s heater has been ON, shut the heat control OFF, but allow the belt to continue
running for 10 -15 minutes, or until the heater has cooled to 300°F (149
°
C) or lower
. If the belt
is stopped while the heater is hot, belt damage will occur.
Switch machine OFF and disconnect from power before beginning any adjustment or mainte-
nance.
Do not attempt any maintenance while machine is powered.
Do not run machine with panels or guards removed.
Periodically check ink temperature on garments exiting machine. See page 11, “Operation
Tips.” Readjust temperature control as necessary to maintain correct temperature for your appli-
cation.
Occasionally, check belt tracking and adjust if necessary. See page 9, step 12.
Chains in chain drives can loosen over time; occasionally check the tension on the chain in your
machine.
Allow heater to cool, then shut off machine and disconnect from power as described above in
“Safety during adjustment and maintenance.”
Follow the troubleshooting chart below
If the chart does not resolve the trouble, contact Vastex for additional assistance.
Symptom Possible
Cause
Solution
No functions operate
Machine unplugged
Building wiring fault
Make sure machine is plugged in.
Have wiring checked.
Belt does not move
Belt circuit fuse(s) blown
Speed control faulty
Belt motor faulty
Check or replace fuse(s).
Replace. Contact Vastex.
Replace. Contact Vastex.
No heat
Faulty heater control
Faulty heater assembly
Replace. Contact Vastex.
Replace. Contact Vastex.
Pg. 3
Summary of Contents for D-100
Page 16: ......