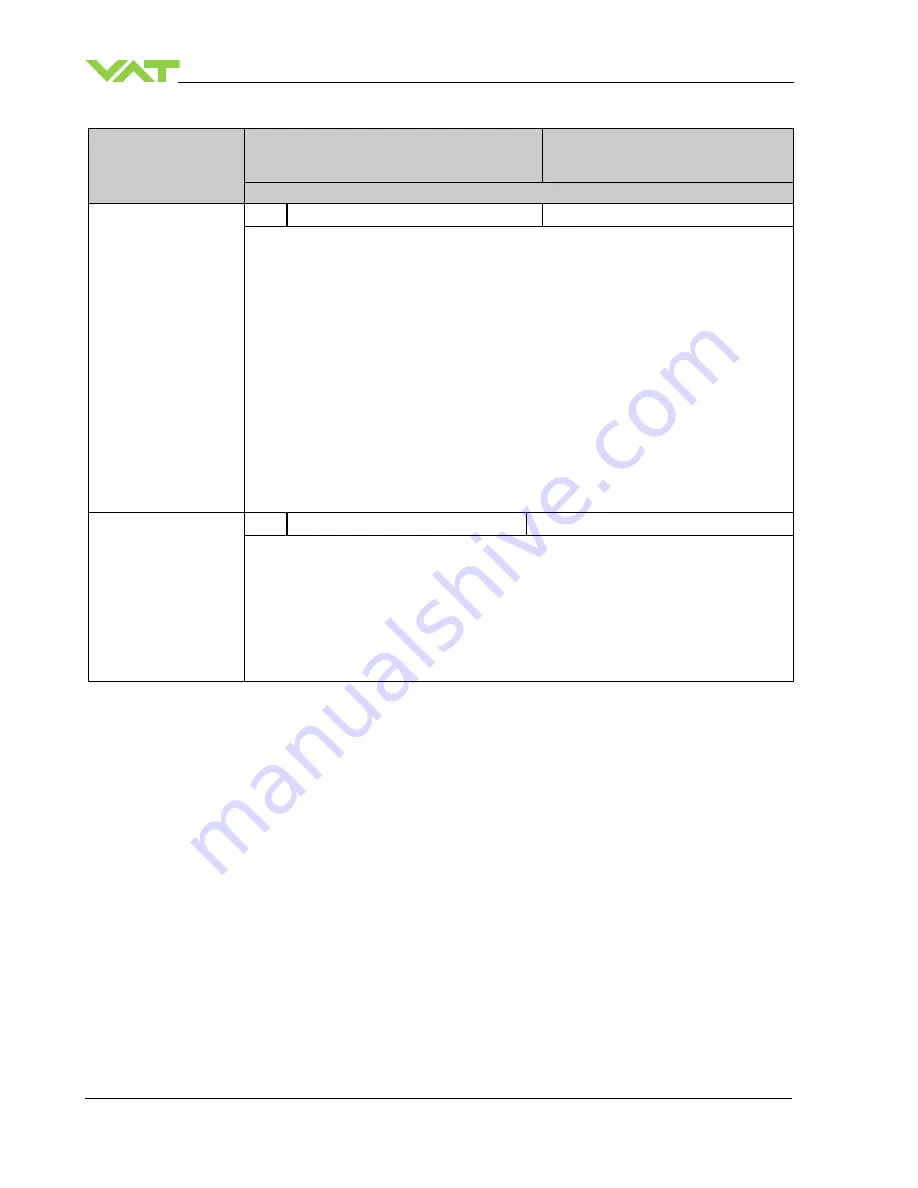
INSTALLATION
Series 590
32/56
Edition 2013-05-13
298292EB
Inquiry function
Command
Acknowledgement
(within 10ms after reception of
command)
Description
WARNINGS
Get
[i:51][CR][LF]
[i:51][abcdefgh][CR][LF]
data length 8 characters
a
0
= no service required
1
= service request, it is indicated when the control unit detects that
motor steps are apparently not effective. This may happen when the valve
is heavily contaminated or the gate seal is heavily sticking. These ‚lost‘ steps
are recognized and will be repeated to attempt target position in the short
term. But in the medium term the valve requires cleaning or inspection.
b
0
= LEARN data set present,
1
= LEARN data set not present
c
0
= power failure battery ready
1
= power failure battery not ready
d
0
= compressed air supply ok
1
= compressed air supply not ok
efgh
reserved, do not use
This function returns warning information about the valve. If a warning is present
countermeasure should be taken. Use RESET command to delete service request bit.
Pay attention:
Without LEARN the valve is not able to run pressure control
ERROR STATUS
Get
[i:52][CR][LF]
[i:52][abcdefgh][CR][LF]
data length 8 characters
a
reserved, do not use
b
1
= sensor 1 signal converter failure
c
reserved, do not use
d
1
= firmware memory failure
efgh
reserved, do not use
This function returns an error code in case of any malfunction of the device otherwise 0 is
returned.
Table 4-8