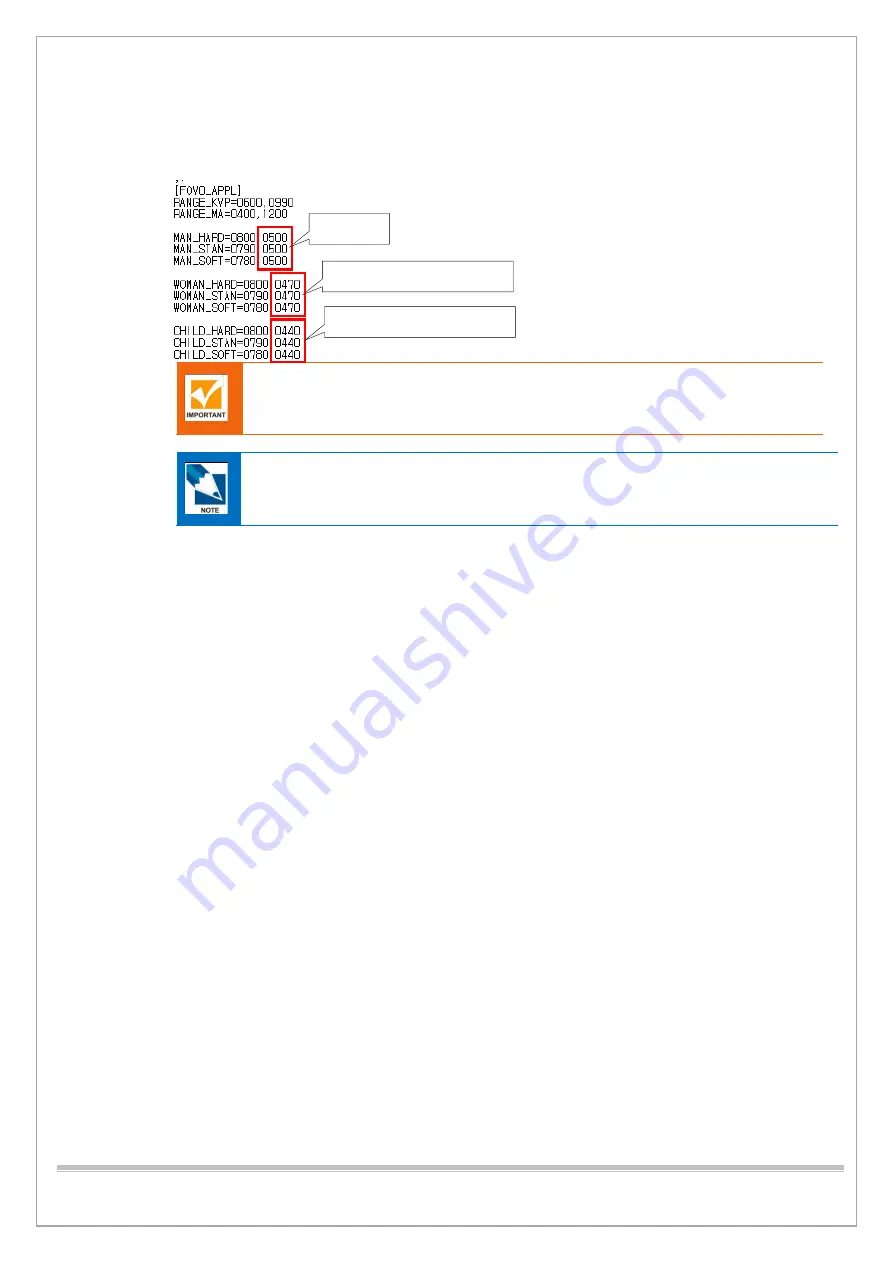
Smart Plus (PHT-35LHS)
Technical Manual
VT-TECH-Smart Plus-001
75 / 188
COPYRIGHT© 2018 VATECH
.
ALL RIGHTS RESERVED
9) Type the mA value that meets the standard of the Background Level in the Green section. For
Woman, subtract 0.3mA from the mA in Man mode and for Child, subtract 0.6mA from the mA in
Man mode and type the value in the section.
•
Do not change the kVps.
•
Make sure that each FOV (FOV 0, FOV 1, FOV 2) has the same values.
By MAN_HARD=0800, 0500, ‘0800’ means 80kVp and ‘0500’ means 5.0mA.
10) Save and exit PwrParam_CBCT.ini.
ex) 5.0mA
ex) 4.7mA = 5.0mA - 0.3mA
ex) 4.4mA = 5.0mA - 0.6mA
Summary of Contents for Smart Plus PHT-35LHS
Page 1: ...Technical manual Model PHT 35LHS Version 1 16 English...
Page 2: ......
Page 190: ...www vatech com...