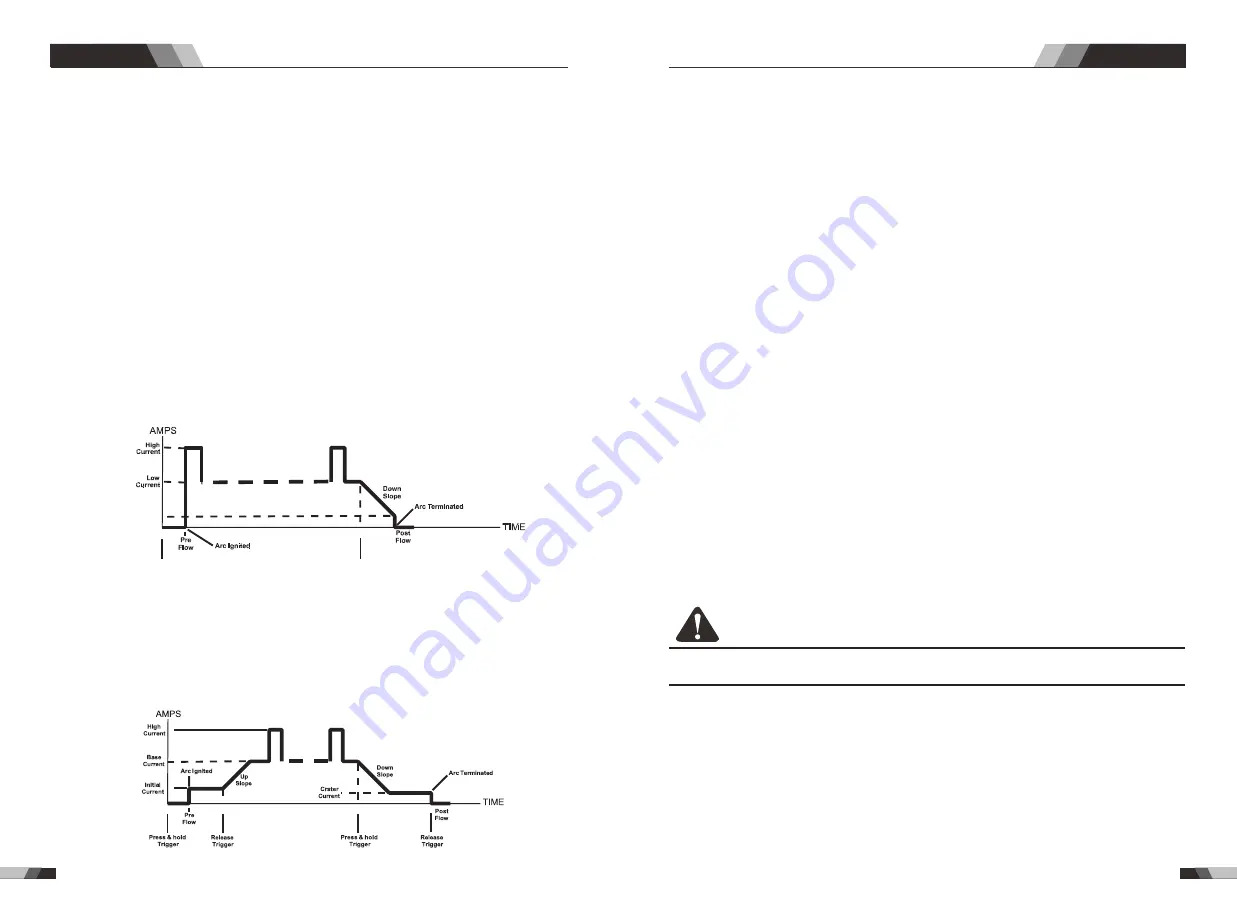
49
50
Operation
Operation
AC/DC WIG SERIES EQUIPMENT
AC/DC WIG SERIES EQUIPMENT
Minimum
Current
Press & hold
Trigger
Release
Trigger
Note: that when operating in GTAW (HF and LIFT TIG modes), the power source will
remain activated until the selected down slope time has elapsed
4T Latch mode this mode of welding is mainly used for long welding runs to reduce
operator fatigue. In this mode the operator can press and release the torch trigger and
the output will remain active. To deactivate the power source, the trigger switch must
again be pressed and released, thus eliminating the need for the operator to hold the
torch trigger.
11. Trigger Mode Control Button (HF TIG and LIFT TIG Mode only)
The trigger mode control is used to switch the functionality of the torch trigger between
2T and 4T.
output to be active.
Press and hold the torch trigger to activate the power source (weld). Release the torch
trigger switch to cease welding.
2T Normal Mode In this mode, the torch trigger must remain pressed for thewelding
8. Frequency Indicator (Hz)
Frequency indicator, when the setting programm in pulse frequency ,this indicator will
be on.
10. Thermal Overload Indicator Light
This welding power source is protected by a self resetting thermostat. The indicator will
illuminate if the duty cycle of the power source has been exceeded. Should the thermal
overload indicator illuminate the output of the power source will be disabled. Once the
power source cools down this light will go OFF and the over temperature condition will
automatically reset. Note that the mains power switch should remain in the on position
such that the fan continues to operate thus allowing the unit to cool sufficiently. Do not
switch the unit off should a thermal overload condition be present.
9. Power ON Indicator
The POWER ON indicator illuminates when the ON/OFF switch is in the ON position and
the correct mains voltage is present.
12. Process Selection Button
The process selection control is used to select the desired welding mode. Two modes
are available, GTAW (TIG), and MMA (Stick) modes.
13. Programming Parameter Indicators
These indicator lights will illuminate when programming.
14. Positive Welding Terminal
Positive Welding Terminal. Welding current flows from the Power Source via heavy
duty bayonet type terminals. It is essential, however, that the male plug is inserted
and turned securely to achieve a sound electrical connection.
and turned securely to achieve a sound electrical connection.
15. Negative Welding Terminal
Negative Welding Terminal. Welding current flows from the Power Source via heavy
duty bayonet type terminals. It is essential, however, that the male plug is inserted
16. Shielding Gas Outlet
The Shielding Gas Outlet located on the front panel is a fast connection of a suitable
TIG Torch.
CAUTION
Loose welding terminal connections can cause overheating and result in the male plug
being fused in the terminal.
18. Power switch
before using the machine. Pull the switch to the closure state of “AN” to operate the
machine, and pull the switch to “AUS” after use. Turn off the power input, and the machine
will stop operating.
19. Gas input port
The gas port is connected with the gas valve output port. After connection, check whether
there is gas leakage.
17. 5 Pin Control Socket
The 5 pin receptacle is used to connect a trigger switch or remote control to the welding
Power Source circuitry:
To make connections, align keyway, insert plug, and rotate threaded collar fully clockwise.