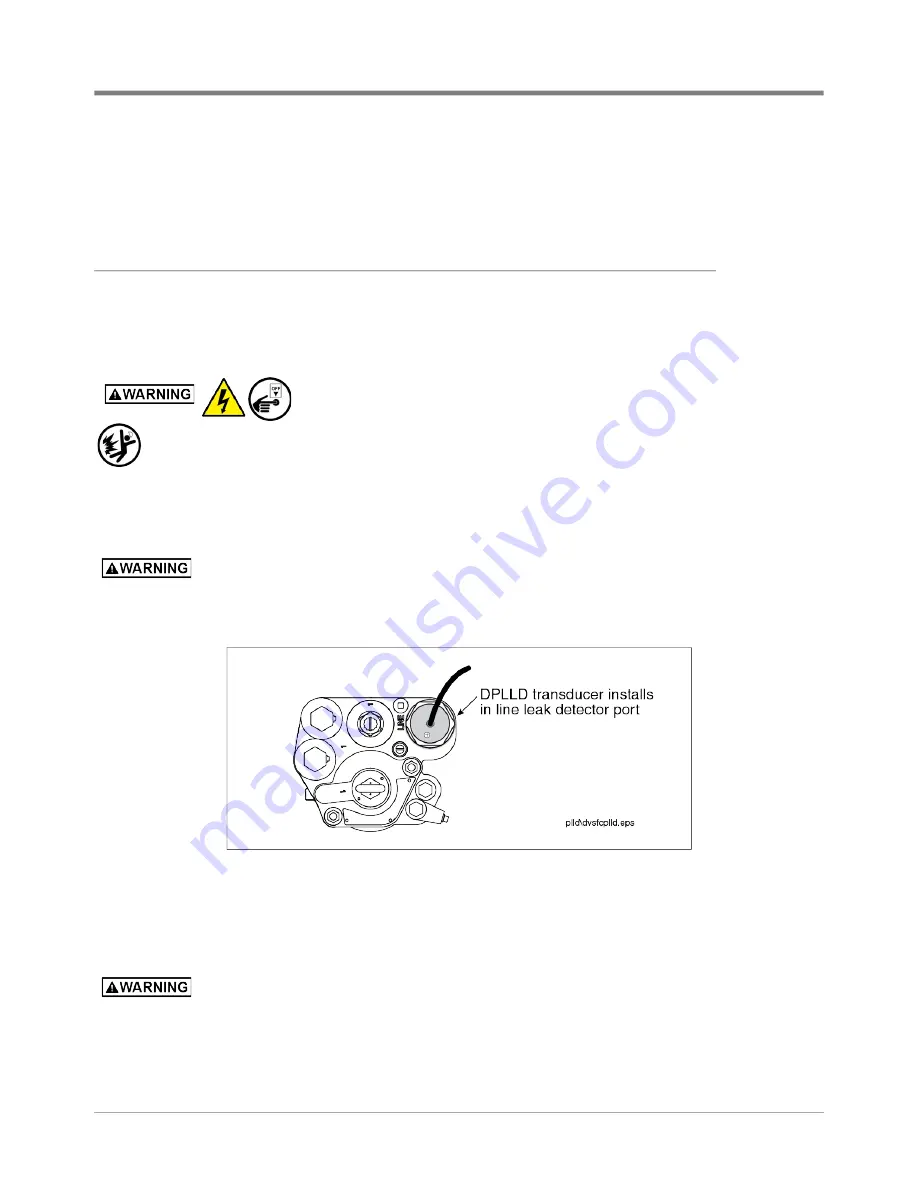
DPLLD Transducer Installation
The Red Jacket Pump
15
tighten the nut to ensure a watertight seal. Connect and seal the pressure transducer wires to the wires from
the TLS console as described in ‘Epoxy Sealing DPLLD Transducer Field Wiring Connections’ on page 21.
5. If applicable, open ball valve down line from the pump. Upon start-up of the pump, check for leaks to ensure
that the system is leak free.
The Red Jacket Pump
The DPLLD transducer mounts directly into the line leak detector pump port. It eliminates the need to break
product lines for installation and service.
Since the DPLLD transducer replaces the existing mechanical device, it is suitable in applications where there is
no sump.
Disconnect, lock out, and tag all AC power to the TLS console, dispens
-
ers and submersible pumps.
When servicing equipment, use non-sparking tools and use caution when removing or
installing equipment to avoid generating a spark.
1. If a ball valve is installed down line from the pump, close it.
2. If the pump does not have a Stage II vapor recovery device installed in the pressurized piping, remove the 2’’
NPT plug from line leak detector port. Install the DPLLD transducer into the 2’’ NPT port (see Figure
12).
Seal the NPT threads only with a UL-Classified, nontoxic pipe sealant suitable for the
fuel involved (for high-alcohol fuel blend applications, Loctite 564 is recommended).
Apply sealant in a manner that prevents it from entering and contaminating hydraulic
cavities.
Figure 12. Locating Discharge Port Plug For Line Leak Transducer
3. If the pump does have a Stage II vapor recovery device installed in the pressurized piping, lubricate the
external o-ring on the SwiftCheck valve using mineral oil or other suitable lubricant and thread the valve into
the Red Jacket leak detector fitting (P/N 038-072) as shown in Figure
10 instead of in the pump’s
leak detector port. Next thread the DPLLD transducer into the 038-072 fitting.
Seal the NPT threads only with a UL-Classified, nontoxic pipe sealant suitable for the
fuel involved (for high-alcohol fuel blend applications, Loctite 564 is recommended).
Apply sealant in a manner that prevents it from entering and contaminating hydraulic
cavities.