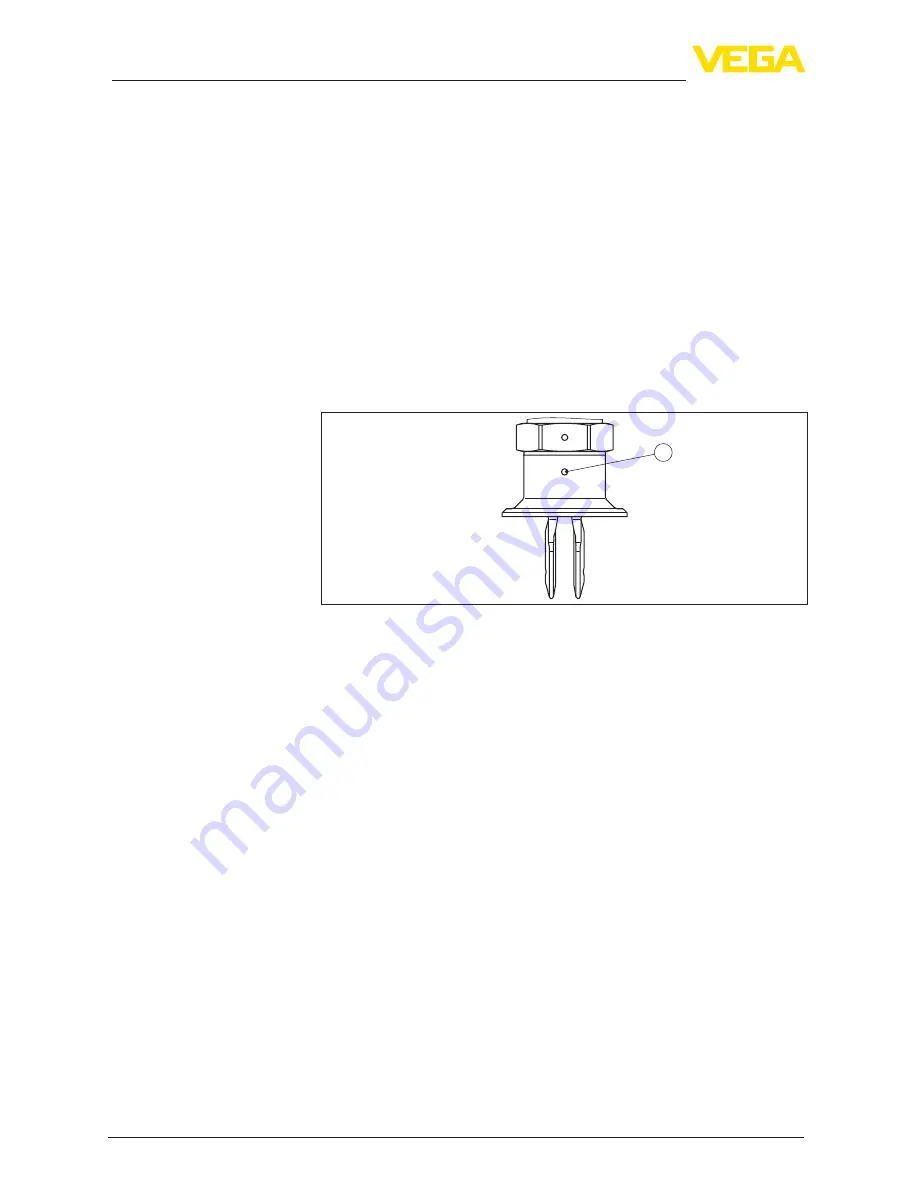
14
4 Mounting
VEGASWING 61 • - transistor (NPN/PNP)
29225-EN-161125
4.2 Mounting instructions
VEGASWING 61 has a defined thread starting point. This means
that every VEGASWING 61 is in the same fork position after being
screwed in. Remove therefore the supplied seal from the thread of
VEGASWING 61. This seal is not required when using a welded
socket with O-ring in front.
Keep in mind that this welded socket is not suitable for coated instru-
ment versions.
Screw VEGASWING 61 completely into the welded socket. The
later position can be determined already before welding. Mark the
appropriate position of the welded socket. Before welding, unscrew
VEGASWING 61 and remove the rubber ring from the welded socket.
The welded socket has a marking (notch). Weld the socket with the
notch facing upward, or in case of pipelines (DN 32 up to DN 50),
aligned with the direction of flow.
1
Fig. 7: Marking on the welded socket
1 Marking
In case of horizontal mounting in adhesive and viscous products,
the surfaces of the tuning fork should be vertical in order to reduce
buildup on the tuning fork. On the screwed version you will find a
marking on the hexagon. With this you can check the position of the
tuning fork when screwing it in. When the hexagon touches the seal,
the thread can still be turned by approx. half a turn. This is sufficient to
reach the recommended installation position.
In the case of flange versions, the fork is aligned with the flange holes.
When used in adhesive and viscous products, the tuning fork should
protrude into the vessel to avoid buildup. For that reason, sockets
for flanges and mounting bosses should be avoided when mounting
horizontally.
If VEGASWING 61 is mounted in the filling stream, unwanted false
measurement signals can be generated. For this reason, mount
VEGASWING 61 at a position in the vessel where no disturbances,
e.g. from filling openings, agitators, etc., can occur.
To make sure the tuning fork of VEGASWING 61 generates as little
resistance as possible to product flow, mount the sensor so that the
surfaces are parallel to the product movement.
Welded socket
Adhesive products
Inflowing medium
Product flow