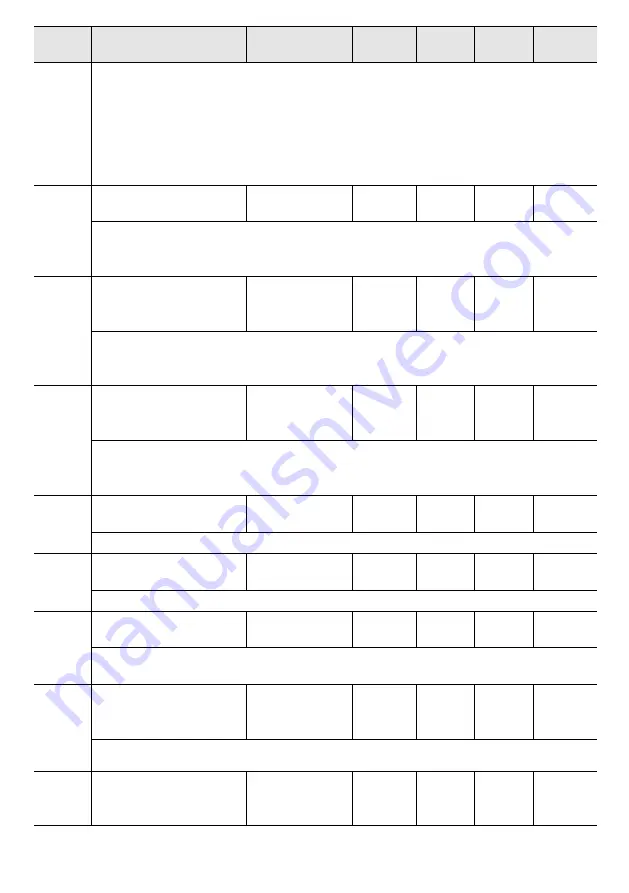
25
Function
code
Parameters
Range
Default
Unit
Address
Effective
way
The model tracking attenuation coefficient is reduced, the position setting section is easy to
overshoot and the overshoot becomes larger, and if the setting is too small, the position oscillation
is easily caused. When it is increased, the position overshoot is reduced, but when it is too large,
the position is easy to rebound, resulting in the positioning time changing. Long, it is
recommended to keep the value unchanged at 100 in general use
Pn243
Model tracking control
speed feedforward gain
0~1000
100.0
%
0x0243
INST
The feedforward gain of the model tracking speed is reduced, the response is slower, but it is not
easy to produce position overshoot and overshoot, and too small is easy to cause a long position
deviation ending time
Pn244
Model tracking control
forward torque feedforward
gain
0~1000
100.0
%
0x0244
INST
Positive position command, this parameter is used when adjusting the positive response
separately. When the value is increased, the torque feedforward rises faster, which can shorten the
positioning time appropriately.
Pn245
Model tracking control
reverse torque feedforward
gain
0~1000
100.0
%
0x0245
INST
Negative position command. Use this parameter when adjusting the negative response separately.
When the value is increased, the torque feedforward rises faster, which can shorten the positioning
time appropriately.
Pn246
Model 2 tracking control
gain
1~2000
50.0
1/s
0x0246
INST
Used when the model tracking is effective, the second gain
Pn247
Model 2 tracking control
Attenuation coefficient
50~200
100.0
%
0x0247
INST
Used when the model tracking is effective, the second gain
Pn249
Speed/Torque Feedforward
Selection
0x00~0x01
0
-
0x0249
INST
0-do not use model tracking control and external speed and torque feedforward at the same time
1-use model tracking control and external speed and torque feedforward simultaneously
Pn250
Instructions
of
external
encoders under full closed
loop control mode
0~3
0
-
0x0250
RST
0-0-do not use full closed loop function 1-use in standard running direction 2-use in reverse
running direction
Pn252
Motor
load
division
coefficient while tuning 1
cycle under full closed loop
0~100
20
%
0x0252
INST
Summary of Contents for SD700-110D series
Page 8: ...4 ...
Page 14: ...10 1 10 Position Control Wiring Diagram ...
Page 15: ...11 1 11 Speed Control Wiring Diagram ...