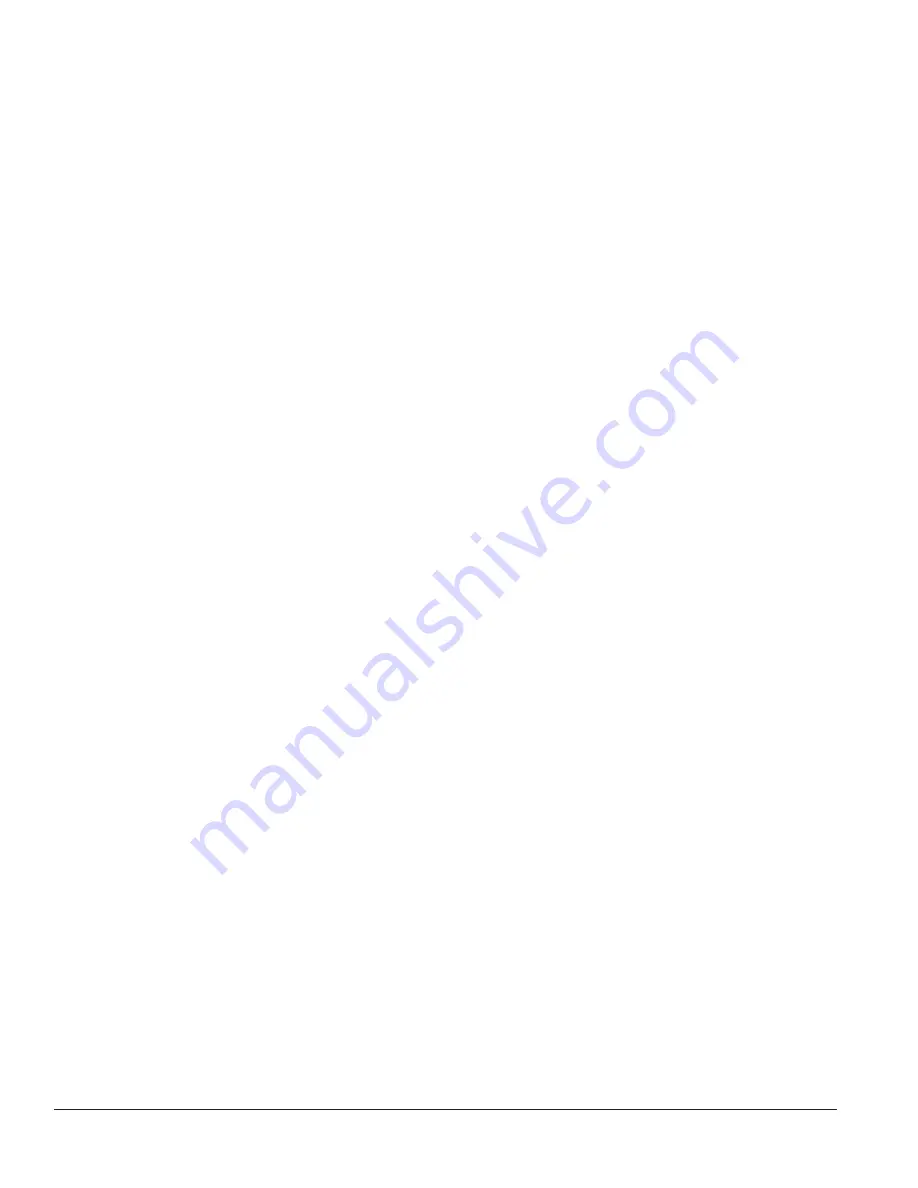
84
106309-03 - 4/19
8. DHW Two boiler Start
When the Indirect Water Heater (IWH) parameter is
set to “Primary Piped” and the DHW Two Boiler Start
parameter is set to “Enabled” two boilers are started
without delay in response to a DHW call for heat.
This feature allows rapid recovery of large IWH’s and
multiple IWH’s.
9. Optimized Boiler Modulation
Boiler firing rate is managed to increase smoothly
as boilers are started. For example, when a second
boiler is started the initial firing rate is 100%/2 or 50%,
when the third boiler is started the firing rate starts at
200%/3 or 66%. After the initial start, the Sequence
Master develops a unison firing rate demand based on
it’s setpoint and sensed header temperature.
10. Modulating Condensing Boiler Control
During low loads, the Sequence Master limits firing
rates to a ‘Base Load Common Rate” to ensure peak
modulating condensing boiler operating efficiency.
Lower firing rates boost efficiency by helping increase
the amount of flue gas water vapor condensation. The
Control maintains a “Base Load Common Rate” until
the last lag boiler is started. At this point, the “Base
Load Common Rate” is released to allow boilers to
modulated as required to meet heat load.
X. Operation
D. Multiple Boiler Control Sequencer (continued)
11. Advanced Boiler Sequencing
After there is a Call For Heat input, both header water
temperature and boiler firing rate percent are used to start
and stop the networked boilers. The control starts and
stops boilers when the water temperature is outside the
user selected “Diff Above” and “Diff Below” settings.
Also, in order to minimize temperature deviations, the
control adjusts the number of boilers running based
on the firing rate. This combination allows the boilers
to anticipate slow load changes before they disrupt
water temperature yet still respond quickly to sudden
load changes. These special sequencer features help
reduce energy wasting system temperature swings and
the resulting unnecessary boiler cycling.
12. Stop All Boilers
All boilers are stopped without delay if the Call for
Heat input is removed, or, if the header temperature
is higher than 195°F (90.6°C) (field adjustable).
Summary of Contents for Phantom-X Series
Page 49: ...49 106309 03 4 19 VI Water Piping and Trim continued Figure 28 Near Boiler Piping Heating Only...
Page 63: ...63 106309 03 4 19 VIII Electrical continued Figure 40 Ladder Diagram...
Page 64: ...64 106309 03 4 19 VIII Electrical continued Figure 41 Wiring Connections Diagram 2...
Page 73: ...73 106309 03 4 19 IX System Start up continued Figure 47 Operating Instructions...
Page 124: ...124 106309 03 4 19 XIII Service Parts continued...
Page 130: ...130 106309 03 4 19 XIII Service Parts continued...
Page 133: ...133 106309 03 4 19 XIII Service Parts continued 10A 10B 10C 10D 10G...
Page 139: ...139 106309 03 4 19...