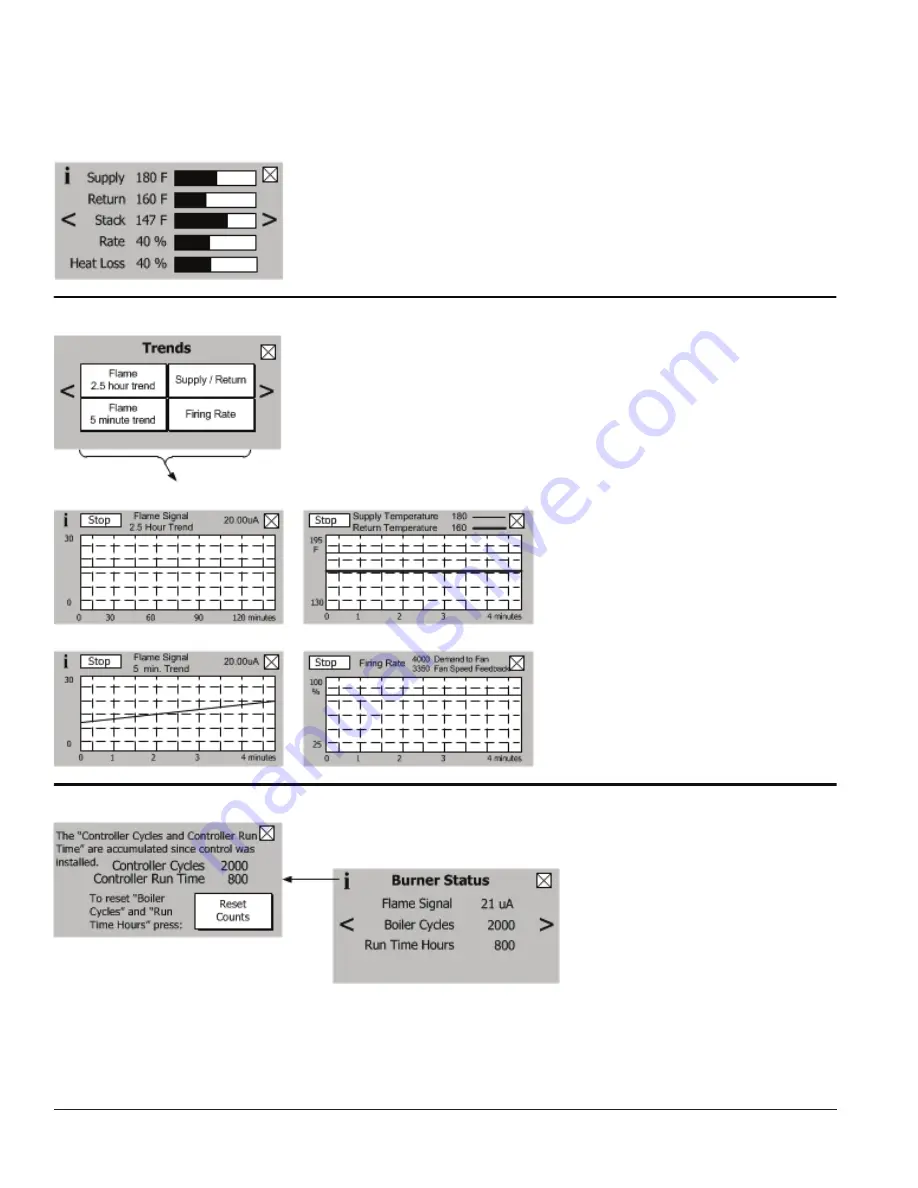
88
106309-03 - 4/19
X. Operation
E. Boiler Sequence Of Operation (continued)
3. Status Screens (continued)
Bargraph Screen
Bargraph Screen
The bargraph screen presents measured values for easy comparison.
Included on this screen is firing rate and when the Zone Panel is connected
the measure Heat Loss. Measured heat loss is the heat rate kbtu/hr sum of
all active (call for heat) zones. This value represents the maximum required
firing rate.
Data Logging
Real time graphic trends allow users to observe process changes over
time providing valuable diagnostic information. For example, flame
current performance over start up periods and varying loads can be an
indication of gas supply issues. Additionally, supply and return tempera
-
ture dual pen trends brings a focused look at heat exchanger and pump
performance. For example, studying a differential temperature trend may
indicate pump speed settings need to be changed.
Trend Screens
NOTE
Firing Rate Trend shows fan demand and
feedback.
Burner Status Screen
Cycles and Hours
Boiler cycles and hours are used to monitor
the boilers overall compatibility to the
heating load. Excessive cycling compared
to run time house may be an indication of
pumping, boiler sizing or adjustment issues.
NOTE
“Boiler Cycle” and “Run Time Hours” are
resettable by selecting the “Reset Counts”
button located on the information screen.
The “Controller Cycles” and “Control
-
ler Run Time” data is not resettable and
remains for the life of the control.
Summary of Contents for Phantom-X Series
Page 49: ...49 106309 03 4 19 VI Water Piping and Trim continued Figure 28 Near Boiler Piping Heating Only...
Page 63: ...63 106309 03 4 19 VIII Electrical continued Figure 40 Ladder Diagram...
Page 64: ...64 106309 03 4 19 VIII Electrical continued Figure 41 Wiring Connections Diagram 2...
Page 73: ...73 106309 03 4 19 IX System Start up continued Figure 47 Operating Instructions...
Page 124: ...124 106309 03 4 19 XIII Service Parts continued...
Page 130: ...130 106309 03 4 19 XIII Service Parts continued...
Page 133: ...133 106309 03 4 19 XIII Service Parts continued 10A 10B 10C 10D 10G...
Page 139: ...139 106309 03 4 19...