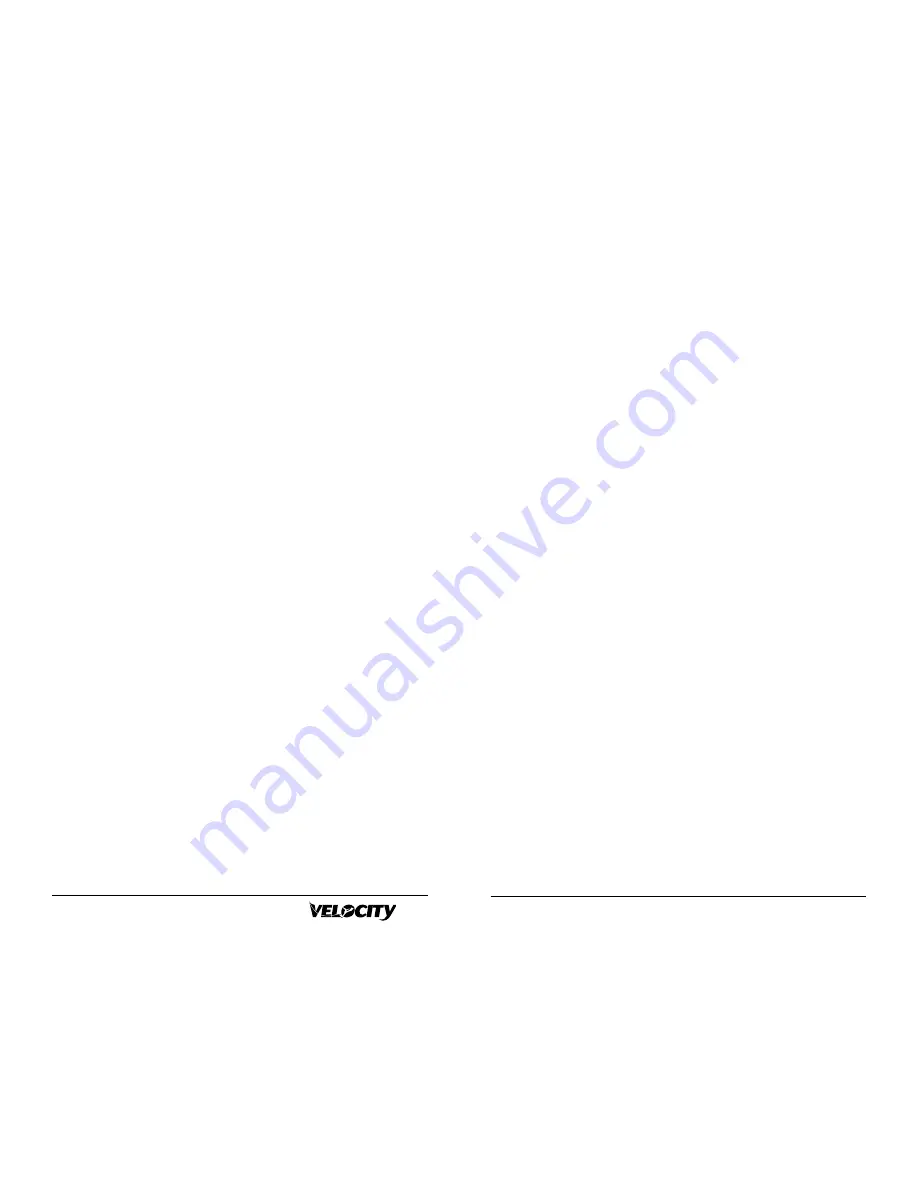
21
O
WNER
’
S
F
LIGHT
M
ANUAL
20
ft. altitude loss).This may be 180 knots/4000 ft. for the high com-
pression IO540.The pilot should determine when it is no longer
feasible to attempt restart, since the best glide angle speeds may
be lower than windmill speeds (best glide distance may be done
with prop stopped).
ENGINE OUT APPROACH
If an engine-out landing is unavoidable, check wind direction,
choose your landing area and establish your glide at 90 to 100
knots. Remember that with the engine out and prop windmilling,
your glide will be considerably steeper than the normal engine-
idle glide that you are accustomed to. If you are radio equipped,
tune in 121.5 and declare an emergency and give your intended
landing site. Set up the forced landing pattern with the landing
brake out, if so equipped, and shoot for the middle 1/3 of the
forced landing area.Turn your electrical power and mags off
before touchdown to minimize any potential fire hazard.
Touchdown as slowly as possible if landing in rough terrain.
INFLIGHT DOOR OPENING
Door opening in flight is a serious emergency. Should the door
come fully open 90° in flight, immediately grab the rail/handle and
pull the door down. Be sure to maintain aircraft control. Do not
be so concerned with closing the canopy that you allow the air-
craft to fly unnecessarily into the ground.
LANDING GEAR EMERGENCIES
The only gear emergency to be considered in a fixed gear
Velocity is a flat tire. Landing with a flat/blown main tire: make a
normal landing touchdown near the side of the runway with the
good tire. Use ailerons to hold the weight off the flat tire. Lower
the nose and use brakes for directional control. Never attempt to
takeoff with a flat tire.
A gear down emergency in the “RG” requires that the pilot
determine if the emergency is:
1) electrically related;
XL
2) hydraulically related; and
3) mechanically related.
If gear fails to retract or extend when the gear switch is
placed in the respective position, (the pump does not run) the first
thing to do is to position the gear switch in the “down” position
and push the momentary “reset” button next to the gear switch.
This will by-pass the normal pressure switches and run the gear
pump motor to purge the pressure switches of any pressure that
might have accumulated due to the aircraft setting in the hot sun
for a period of time and thus the heated hydraulic fluid causing
both pressure switches to activate.
If gear fails to lock down, check circuit breaker if pump has
failed to operate, and gear down lights to determine if a light has
failed. If all check OK, cycle the “dump” valve to release hydraulic
pressure to the electric pressure switches in the system. If the gear
still fails to operate, place gear switch in “down” position, pull gear
circuit breaker and place the dump valve in the ìdownî position.
The gear should free fall in about 7 to 10 seconds to the down and
locked position. If your down lights are wired to the gear circuit
breaker, re-set the circuit breaker long enough to verify “gear
down”. If either gear light fails to light, a visual check of the main
gear overcenter linkage is in order.The nose gear overcenter can
be verified by reaching over the extended center console and
“feeling” or “helping” if necessary the nose gear linkage to lock. A
1” hole can be drilled just below the O.C. linkage in the pilot side
center console (keel) for an easy check of the O.C. linkage.
If the gear pump continues to run but the gear does not
extend, pull circuit breaker and proceed with dump valve as above.
If a mechanical problem is causing a gear to “hang up”, deter-
mine the cause and do what is necessary to “break loose” whatev-
er is causing the hang-up. A sudden pull-up (slow to maneuvering
speed) may be necessary to free a stuck wheel or a jammed cable.
A gear up landing should be made as a last resort. Once gear down
lights are indicated, re-position the dump valve to the normal posi-
tion.This will “lock” hydraulic pressure in the system.
Summary of Contents for XL RG
Page 1: ......