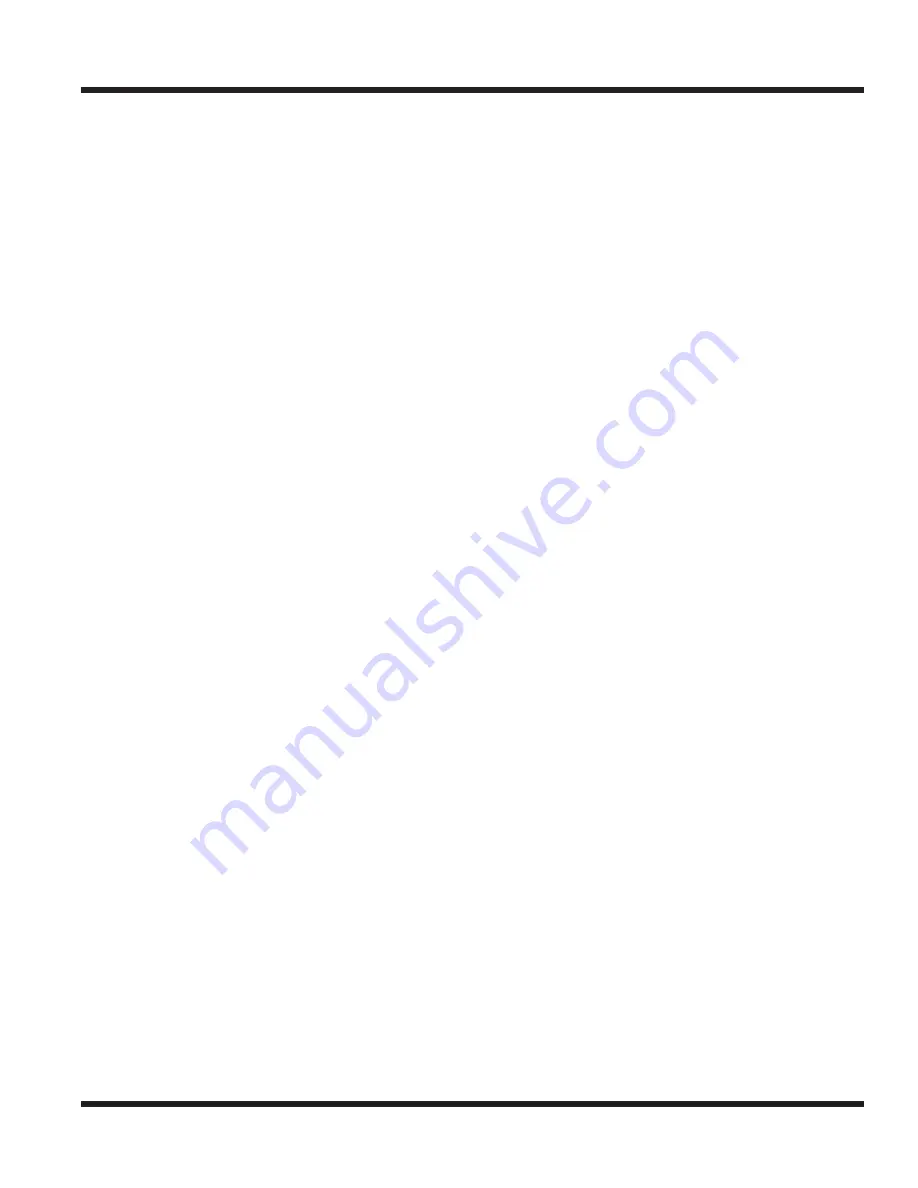
SPECIFICATIONS
Specifi cations - 43
ENGINE
Manufacturer . . . . . . . . . . . . . . . . . . . . . . . . . . . . . . . Vanguard
Model Number. . . . . . . . . . . . . . . . . . . . . . . . . . . . . . . . 543477
Type . . . . . . . . . . . . . . . . . . . . . . . . . . . . . . . . . . Gasoline
Cylinders . . . . . . . . . . . . . . . . . . . . . . . . . . . . . . . . . . . . 2
Displacement . . . . . . . . . . . . . . . . . . . . . . . . . . . . . . . . 895 cc
Engine Gross HP . . . . . . . . . . . . . . . . . . . . . . . . . . . . . . . . 31
Operating Range (RPM) . . . . . . . . . . . . . . . . . . . . . . . . . . .1500-3650
Cooling System . . . . . . . . . . . . . . . . . . . . . . . . . . . . . . Air Cooled
ELECTRICAL
Battery . . . . . . . . . . . . . . . . . . . . . . . . . . . . 450 Cold Cranking Amps
Voltage . . . . . . . . . . . . . . . . . . . . . . . . . . . . . . . . . . 12 Volts
Alternator. . . . . . . . . . . . . . . . . . . . . . . . . . . . . . . . . . 50 Amp
POWER TRAIN
Type . . . . . . . . . . . . . . . . . . . . . . . . . . Hydrostatic (All Wheel Drive)
Hydrostatic Transaxle (2) . . . . . . . . . . . . . . . . . . . . . . . . . . Peerless
Fwd Speed (High)* . . . . . . . . . . . . . . . . . . . . . . . . . .10 mph (16.1 kph)
Fwd Speed (Low)* . . . . . . . . . . . . . . . . . . . . . . . . . . 5.2 mph (8.4 kph)
Brakes . . . . . . . . . . . . . . . . . . . . . . . . . . . . . . . . Hydro-Dynamic
Hydraulic Oil Filtration . . . . . . . . . . . . . . . . . . . . . . . 10 Micron & 25 Micron
CONTROLS & INSTRUMENT PANEL
Steering . . . . . . . . . . . . . . . . . . . . . . . . . . . . . . . . . . Power
PTO (Power Take Off) . . . . . . . . . . . . . . . . . . . . . . . . . .Electric w/brake
Throttle Control . . . . . . . . . . . . . . . . . . . . . . . . . . . . . . . .Cable
Directional Control . . . . . . . . . . . . . . . . .
S
peed,
D
irection,
L
ift,
A
uxiliary (S.D.L.A)
Control Orientation . . . . . . . . . . . . . . . . . . . . . . . . . . . . . . . Hand
Gauges . . . . . . . . . . . . . . . . . . . . . . . . . Tachometer/Hour Meter, Volt
Parking/Emergency Brake . . . . . . . . . . . . . . . . . . . . . . . . . Band Brake
OTHER FEATURES
Turning Radius . . . . . . . . . . . . . . . . . . . . . . . . . . . . . 43” (109 cm)
Standard Tires . . . . . . . . . . . . . . . . . . . . All Terrain (22 x 12-8) (56 x 30-20 cm)
Optional Tires . . . . . . . . . . . . . . . . . . . . . . Turf (22 x 11-10) (56 x 28-26 cm)
Optional Tires . . . . . . . . . . . . . . . . . . . . . . Bar (21 x 11-8) (53 x 58-20 cm)
Headlight . . . . . . . . . . . . . . . . . . . . . . . . . . . . . . Halogen (55 watt)
Attachment System . . . . . . . . . . . . . . . . . . . . . . . . . . . Ventrac Mount
SPECIFICATIONS
* May vary based on tire size, type, and in
fl
ation.