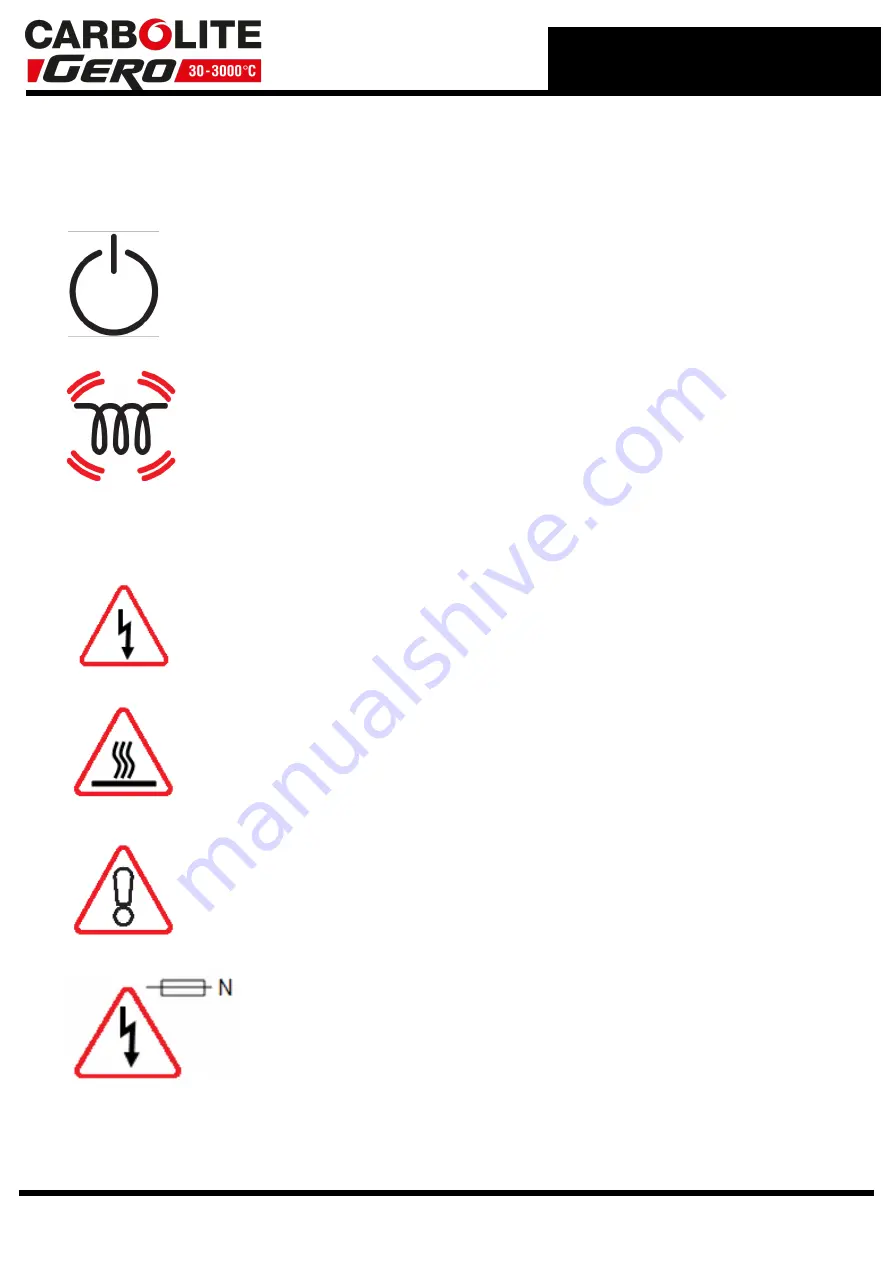
1.0
Symbols and Warnings
1.1
Switches and Lights
Instrument switch: when the instrument switch is operated the
temperature control circuit is energised.
Heat light: the adjacent light glows or flashes to indicate that power
is being supplied to the elements.
1.2
General Warnings
DANGER – Electric shock. Read any warning printed next to this
symbol.
WARNING: Risk of fatal injury.
DANGER – Hot surface. Read any warning printed next to this
symbol.
WARNING: All surfaces of a product may be hot.
DANGER – Read any warning printed next to this symbol.
Caution – Double Pole/Neutral Fusing
5
1.0 Symbols and Warnings
Summary of Contents for CARBOLITE GERO AAF-BAL 11/17
Page 43: ...9 0 Wiring Diagrams 43 9 0 Wiring Diagrams ...
Page 50: ......
Page 51: ...Notes Service Record Engineer Name Date Record of Work ...