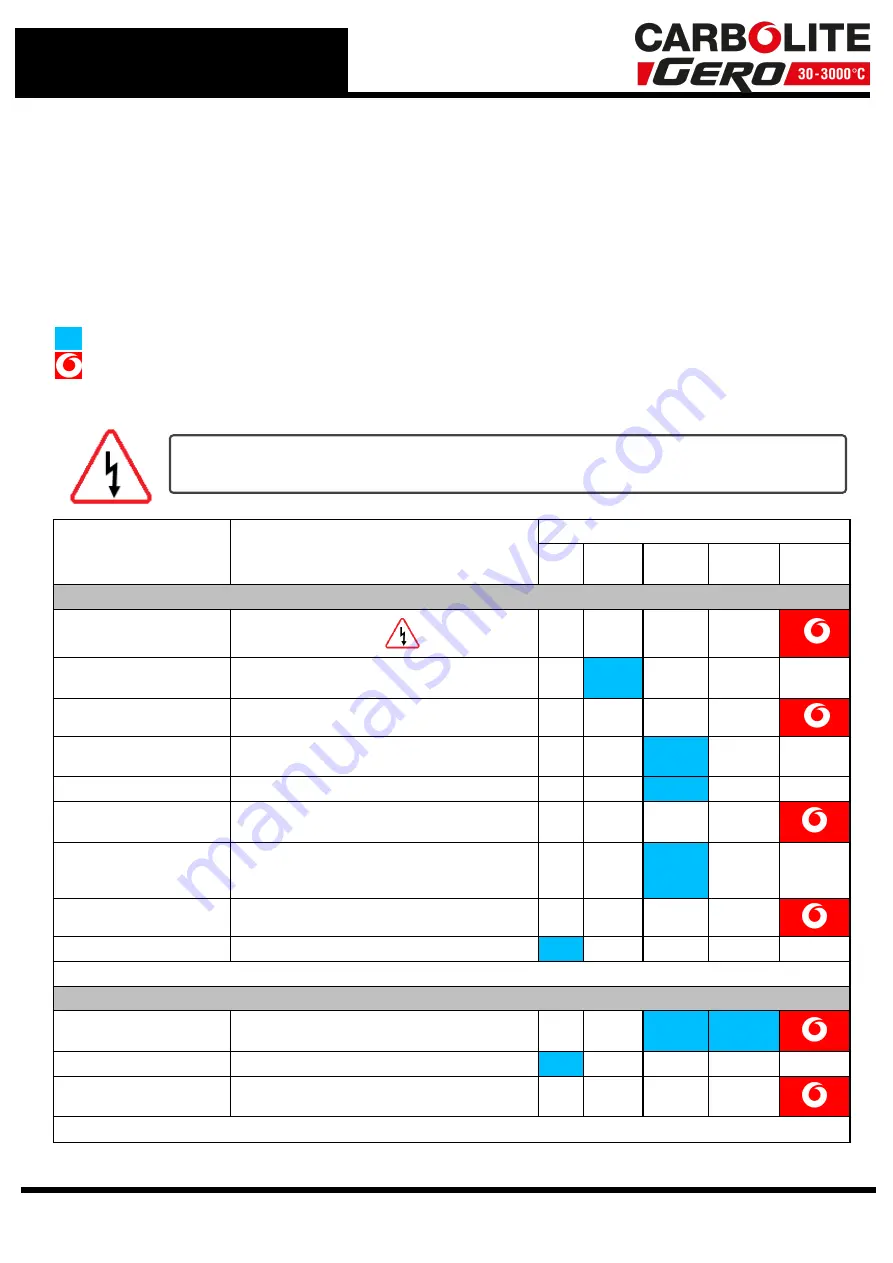
5.0
Maintenance
5.1
General Maintenance
Preventive rather than reactive maintenance is recommended. The type and frequency
depends on the product use; the following are recommended.
5.2
Maintenance Schedule
CUSTOMER
QUALIFIED PERSONNEL
DANGER! ELECTRIC SHOCK
. Risk of fatal injury. Only electrically
qualified personnel should attempt these maintenance procedures.
Maintenance
Procedure
Method
Frequency
Daily Weekly Monthly
Bi-
Annually
Annually
Safety
Over-Temperature Safety
Circuit
Electrical measurement
Door Plug
Visual inspection, checking the seal and whether
it is free of any damage
Door Plug
Replacement where necessary
Extraction Pipe
Check that the connection is tight, and clean out
the pipe if necessary
Electrical Safety (external)
Visual check of external cables and plugs
Electrical Safety (internal)
Physically check all connections and cleaning of
the power plate area
Gas Safety (external)
Visually check that all pipework is in place and
free of damage. Physically check that all con-
nections are tight
Gas Safety (internal)
Leak test the gas system
Cooling Fans
Check whether the cooling fans are working
Function
Temperature Calibration
Tested using certified equipment, frequency
dependent on the standard required
Operational Check
Check that all functions are working normally
Operational Check
Thorough inspection and report incorporating a
test of all functions
46
Summary of Contents for CARBOLITE GERO CAF G5
Page 63: ...Fig 3 Front Tube Seal Assembly Fig 4 Door Arm Assembly 63 ...
Page 64: ...Fig 5a Camera Mounting Bracket Fig 5b Lens and Camera Assembly 64 ...
Page 65: ...Fig 5c Sliding the Camera Mounting Bracket Assembly onto the Door Arm 65 ...
Page 66: ...Fig 5d Securing the Camera Mounting Bracket Assembly to the Door Arm 66 ...
Page 67: ...Fig 5e Mounting the Lens and Camera Assembly 67 ...
Page 68: ...Fig 5f Lens and Camera Assembly in Position 68 ...
Page 69: ...Fig 6a Rear View of the Standard CAF G5 Furnace Showing Brick Box Assembly 69 ...
Page 71: ...Fig 7 Front Tube Seal Position 71 ...
Page 72: ...Fig 8 Tube End Seal Assembly Tightening Sequence Fig 9 Work Tube Front Support 72 ...
Page 73: ...Fig 10 Fitting the Door Arm Assembly Fig 10a Adjusting the Door Arm Assembly 73 ...
Page 74: ...Fig 11a Furnace Case and Controls 74 ...
Page 75: ...Fig 11b Gas Inlet Pipe Fig 12 Positioning the Furnace 75 ...
Page 77: ...Fig 13c Loading Samples into the Work Tube 77 ...
Page 78: ...Fig 16 File Folder 78 ...
Page 79: ...Fig 17 Door Arm Assembly Exploded View 79 ...
Page 82: ...SST DT HT FT Fig 18 Report Sheet Page 2 Side View Plan View Fig 19 Formed Wire Sample 82 ...
Page 83: ...Fig 20 Sample Carrier Sample Tiles and Sample Positions 83 ...
Page 84: ...Fig 21a Coal and Coke Test Piece Mould Fig 21b Biomass Test Piece Mould and Hand Press 84 ...
Page 85: ...Fig 22 Sample Loading Tool Fig 23 Camera Ethernet Connection 85 ...
Page 86: ...Fig 24 LED Driver Connection 86 ...
Page 87: ...Notes Service Record Engineer Name Date Record of Work ...