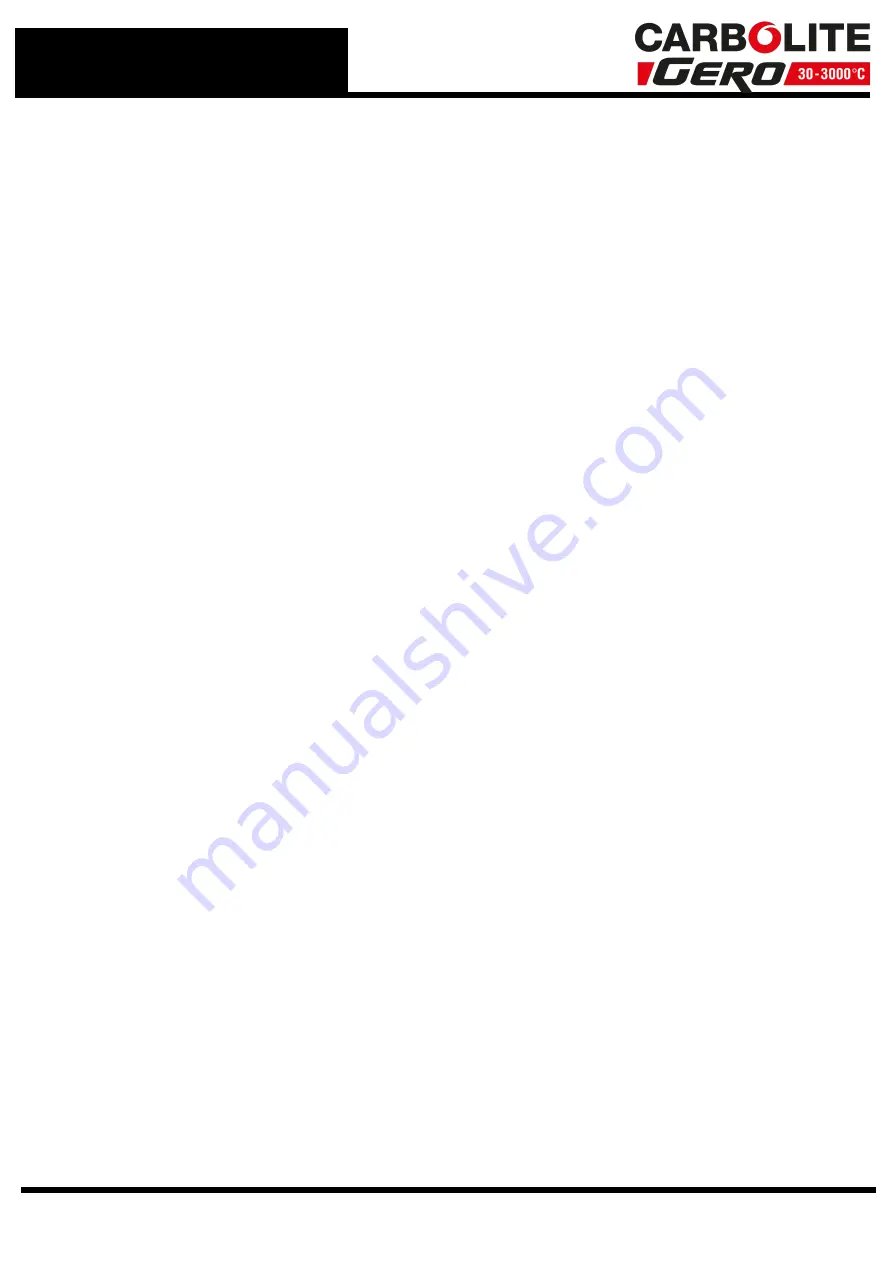
control panel. See fig 11a. This alarm will continue until the furnace is turned off
and the 'purge' gas supply is restored. While the alarm is activated the control sys-
tem will not allow introduction of 'reducing' gas.
3. Switch on the furnace electrical supply, the cooling fans will run. Operate the instru-
ment switch to activate the control system, the furnace will begin to heat up to the
start temperature and the work tube will be purged with 'Purge' gas for 5 minutes.
The standby temperature is adjustable using the software, see section 4.7.2.2.
Note:
Initial heat up of the furnace may create a strong odour from the binders in the
new insulation materials; it is therefore recommended that the furnace is located where
there is adequate extraction during the first heating phase. The fumes from the binders
may also cause interference with the internal CO sensor during initial heat up (see fault
analysis in section 6.0).
For furnaces constructed to use CO/ CO
2
and Air test gases with N
2
'Purge' gas,
(compatible with ASTM D1857/ D1857M -04 (2010) & BS ISO 540: 2008 & DDCEN/ TS
15370-1:2006 & PD CEN/ TR 15404:2002) the start temperature is adjustable from 400
°C.
For furnaces constructed to use H
2
and CO
2
test gases with CO
2
'Purge' gas,
(compatible with BS ISO 540: 2008) the start temperature is adjustable from 815 °C.
To switch the furnace off, set the instrument switch to off, see fig 11a. The case cooling
fans remain on. Leave the fans on until the furnace cools to below 300 °C. If the
furnace is to be left off unattended, isolate it from the electrical supply.
Note
: It is not recommended to operate the furnace continuously at temperatures
above 1500°C. The furnace is designed to operate to a programmed ramp; continuous
operation at elevated temperatures will shorten the life of the elements, insulation and
tube end seals.
4.2
Eurotherm Controller
The Eurotherm controller is configured to control the furnace and provide the other
signals necessary to switch gas flows, rear lighting (if fitted) and communicate with the
CAF Test Software. All the Eurotherm controls required for ash fusion testing are
accessed through the software.
4.3
Computer Start-Up
The computer is set up by Carbolite Gero to run the following software:
Microsoft Windows 7 embedded.
Carbolite Gero Ash Fusibility Test Software:
Although the software is already installed, an installation memory stick is supplied for
system support.
22
Summary of Contents for CARBOLITE GERO CAF G5
Page 63: ...Fig 3 Front Tube Seal Assembly Fig 4 Door Arm Assembly 63 ...
Page 64: ...Fig 5a Camera Mounting Bracket Fig 5b Lens and Camera Assembly 64 ...
Page 65: ...Fig 5c Sliding the Camera Mounting Bracket Assembly onto the Door Arm 65 ...
Page 66: ...Fig 5d Securing the Camera Mounting Bracket Assembly to the Door Arm 66 ...
Page 67: ...Fig 5e Mounting the Lens and Camera Assembly 67 ...
Page 68: ...Fig 5f Lens and Camera Assembly in Position 68 ...
Page 69: ...Fig 6a Rear View of the Standard CAF G5 Furnace Showing Brick Box Assembly 69 ...
Page 71: ...Fig 7 Front Tube Seal Position 71 ...
Page 72: ...Fig 8 Tube End Seal Assembly Tightening Sequence Fig 9 Work Tube Front Support 72 ...
Page 73: ...Fig 10 Fitting the Door Arm Assembly Fig 10a Adjusting the Door Arm Assembly 73 ...
Page 74: ...Fig 11a Furnace Case and Controls 74 ...
Page 75: ...Fig 11b Gas Inlet Pipe Fig 12 Positioning the Furnace 75 ...
Page 77: ...Fig 13c Loading Samples into the Work Tube 77 ...
Page 78: ...Fig 16 File Folder 78 ...
Page 79: ...Fig 17 Door Arm Assembly Exploded View 79 ...
Page 82: ...SST DT HT FT Fig 18 Report Sheet Page 2 Side View Plan View Fig 19 Formed Wire Sample 82 ...
Page 83: ...Fig 20 Sample Carrier Sample Tiles and Sample Positions 83 ...
Page 84: ...Fig 21a Coal and Coke Test Piece Mould Fig 21b Biomass Test Piece Mould and Hand Press 84 ...
Page 85: ...Fig 22 Sample Loading Tool Fig 23 Camera Ethernet Connection 85 ...
Page 86: ...Fig 24 LED Driver Connection 86 ...
Page 87: ...Notes Service Record Engineer Name Date Record of Work ...