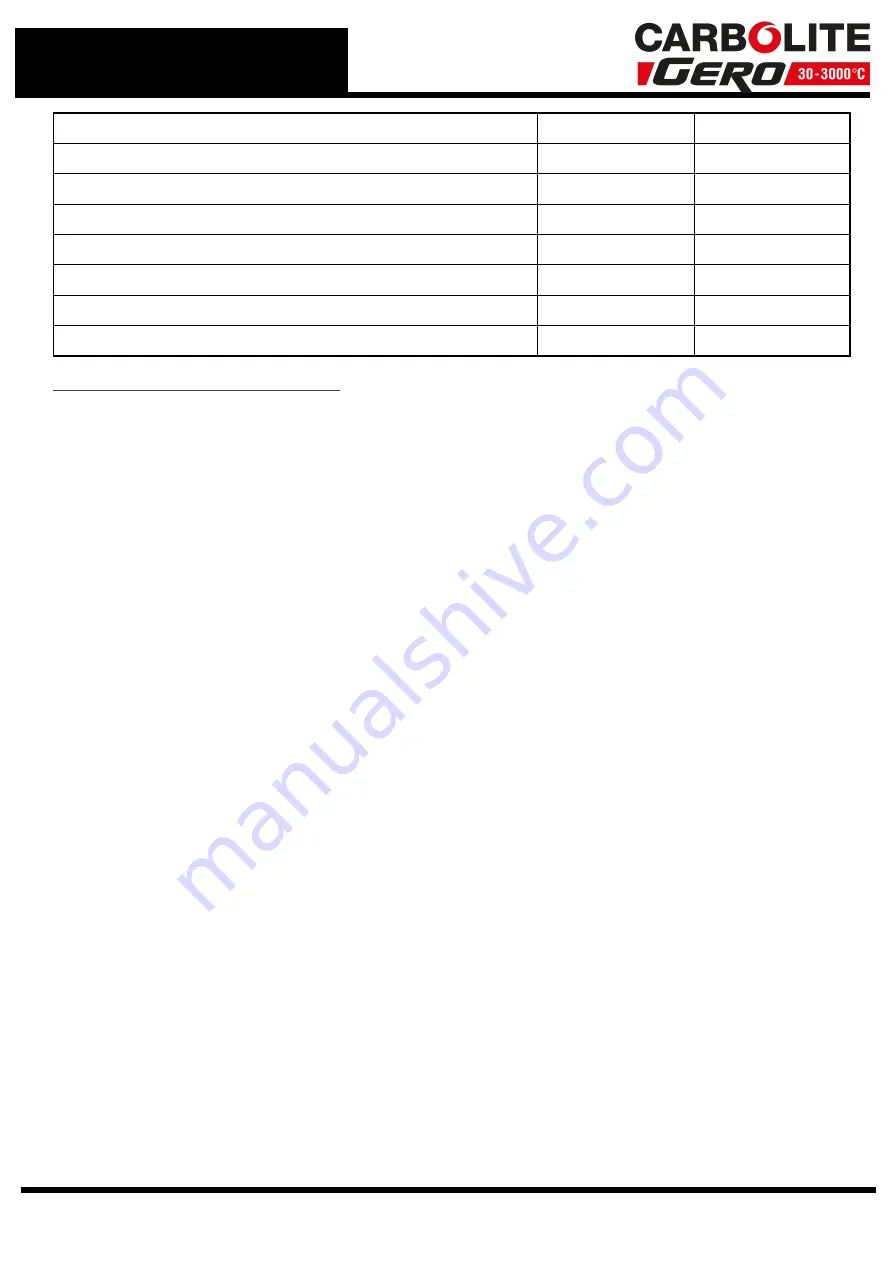
Furnace in °C
Furnace in °F
Actual Gold Melt (ball) temp
1063 °C
1945 °F
Min. permissible Gold Melt (ball) temp
1057.5 °C
1935 °F
Max. permissible Gold Melt (ball) temp
1068.5 °C
1955 °F
Actual Palladium Melt (ball) temp
1554 °C
2829 °F
Min. permissible Palladium Melt (ball) temp
1548.5 °C
2819 °F
Max. permissible Palladium Melt (ball) temp
1559.5 °C
2839 °F
Max. permissible spread (both wire types)
11 °C
20 °F
5.6.4.4
Deviations from Limits
If some or all of the recorded individual melt temperature fall outside the maximum or
minimum permissible temperatures for the relevant material, but the spread is within
the maximum permissible spread, then it is possible to correct the temperature
displayed by the control instrument set-up; see section 5.7.
If the spread lies outside the permissible limit, then the furnace will require rectification
of its temperature uniformity; contact Carbolite Gero for further advice.
Any servicing or modifications to the furnace or controls may affect the calibration of the
furnace and will require a re-test.
5.7
Instrument Calibration Adjustment
A two point calibration function within the furnace controller allows adjustment of the
displayed value at both the Gold and Palladium melt temperatures. Proceed as follows:
l
Calculate the lower calibration temperature (displayed Gold melt temperature) cor-
rection factor:
l
Calculate the lower calibration temperature (displayed Gold melt temperature) cor-
rection factor:
Calculate the Gold mid melt temperature from the results obtained, as given in sec-
tion 5.6.4.
Calculate the lower calibration temperature correction factor as the difference
between the Gold actual melt temperature and the Gold mid melt temperature:
Gold:
actual melt temperature - mid melt temperature = lower calibration temperature
correction factor
For
example:
actual melt temperature = 1063 °C (from table)
mid melt temperature = 1060 °C (calculated from test)
(1063 °C - 1060 °C) = 3.
52
Summary of Contents for CARBOLITE GERO CAF G5
Page 63: ...Fig 3 Front Tube Seal Assembly Fig 4 Door Arm Assembly 63 ...
Page 64: ...Fig 5a Camera Mounting Bracket Fig 5b Lens and Camera Assembly 64 ...
Page 65: ...Fig 5c Sliding the Camera Mounting Bracket Assembly onto the Door Arm 65 ...
Page 66: ...Fig 5d Securing the Camera Mounting Bracket Assembly to the Door Arm 66 ...
Page 67: ...Fig 5e Mounting the Lens and Camera Assembly 67 ...
Page 68: ...Fig 5f Lens and Camera Assembly in Position 68 ...
Page 69: ...Fig 6a Rear View of the Standard CAF G5 Furnace Showing Brick Box Assembly 69 ...
Page 71: ...Fig 7 Front Tube Seal Position 71 ...
Page 72: ...Fig 8 Tube End Seal Assembly Tightening Sequence Fig 9 Work Tube Front Support 72 ...
Page 73: ...Fig 10 Fitting the Door Arm Assembly Fig 10a Adjusting the Door Arm Assembly 73 ...
Page 74: ...Fig 11a Furnace Case and Controls 74 ...
Page 75: ...Fig 11b Gas Inlet Pipe Fig 12 Positioning the Furnace 75 ...
Page 77: ...Fig 13c Loading Samples into the Work Tube 77 ...
Page 78: ...Fig 16 File Folder 78 ...
Page 79: ...Fig 17 Door Arm Assembly Exploded View 79 ...
Page 82: ...SST DT HT FT Fig 18 Report Sheet Page 2 Side View Plan View Fig 19 Formed Wire Sample 82 ...
Page 83: ...Fig 20 Sample Carrier Sample Tiles and Sample Positions 83 ...
Page 84: ...Fig 21a Coal and Coke Test Piece Mould Fig 21b Biomass Test Piece Mould and Hand Press 84 ...
Page 85: ...Fig 22 Sample Loading Tool Fig 23 Camera Ethernet Connection 85 ...
Page 86: ...Fig 24 LED Driver Connection 86 ...
Page 87: ...Notes Service Record Engineer Name Date Record of Work ...