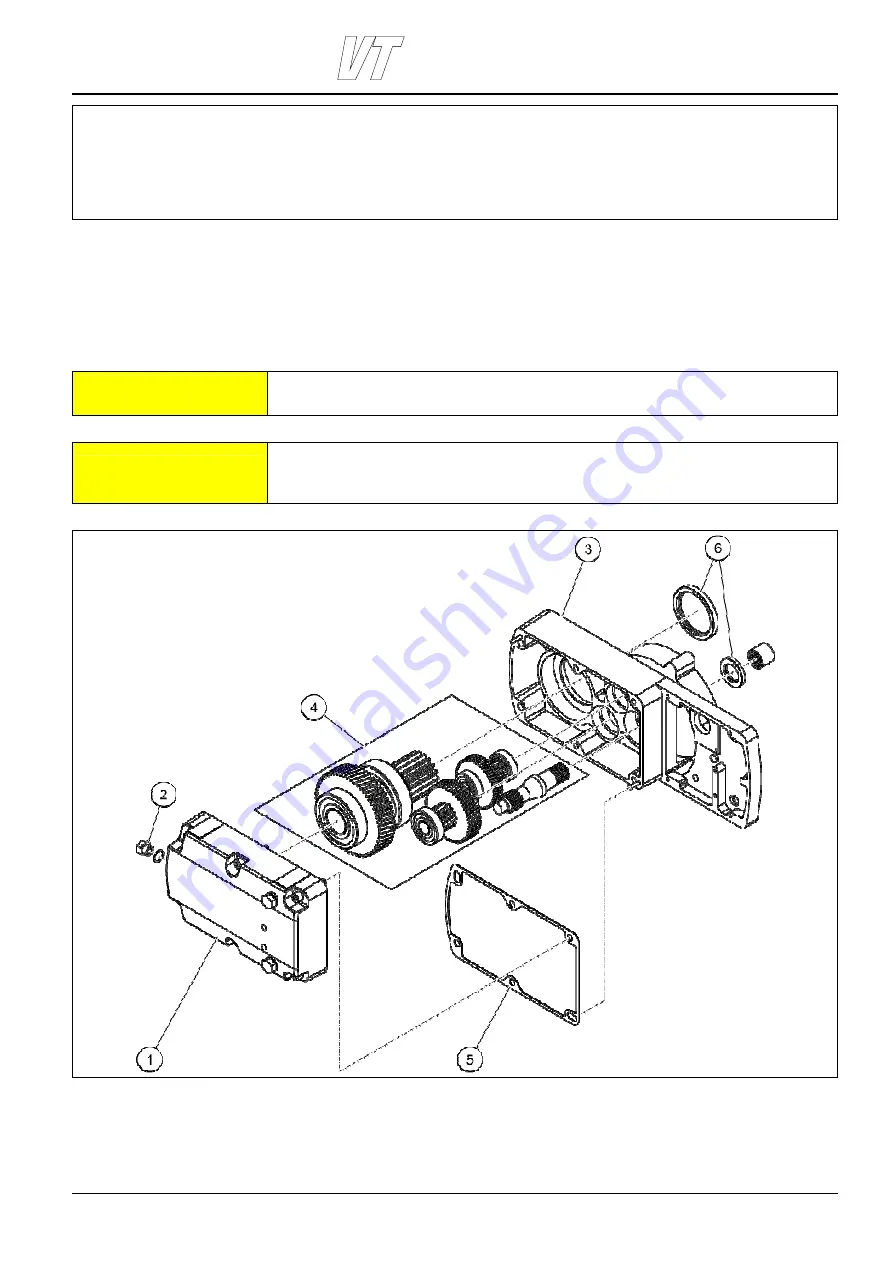
EUROBLOC
SERVICE MANUAL FOR HOIST
81/212
This document and the information contained herein, is the exclusive property of Verlinde S.A.S. and represents a non-public, confidential and proprietary trade secret that
may not be reproduced, disclosed to third parties, altered or otherwise employed in any manner whatsoever without the express written consent of Verlinde S.A.S.
Copyright © (2013) Verlinde S.A.S. All rights reserved.
06/2015
1. Breather plug
2. Fixing screws for hoisting motor
3. Fixing screws for gearbox cover
4. Gearbox cover
5. Fixing screws for gearbox
6. Fixing plate for gearbox
7. Gearbox plug
8. Coupling
7.1.5.1 Replacement of a sealing set for the hoisting gearbox of frame size VTs, VT1, VT2,
VT3
If the gearbox shows signs of excessive lubrication leakage, you must replace the sealings in the gearbox. In this
context, you may also need to change the lubrication inside the gearbox.
CAUTION
Be careful when opening the gearbox and replacing the sealings. There is also a risk
for damaging the equipment or the sealings in the reassembly phase.
CAUTION
Ensure that the lubrication does not leak to the breather plug. Before disassembling
the gearbox from the hoist, replace the breather plug with a blind plug to keep the
breather plug clean.