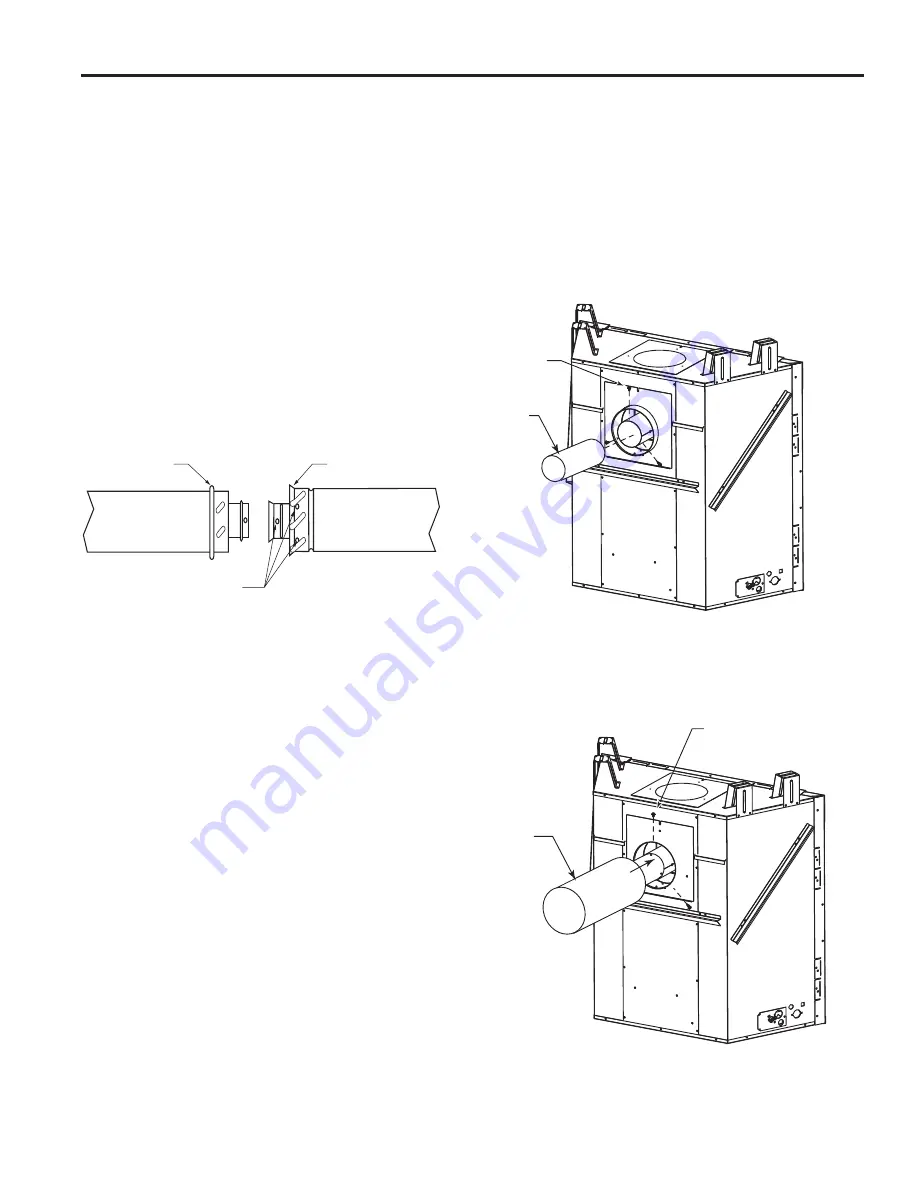
CFDV Series Gas Fireplace
20306739
15
TWIST LOCK PIPE
When using twist lock pipe it is not necessary to use seal-
ant on the joints.
To join twist lock pipes together, simply align the beads of
the male end with the grooves of the female end, twisting
the pipe until the fl ange on the female end contacts exter-
nal fl ange on the male end. It is recommended that you
secure the joints with three (3) sheet metal screws, how-
ever, this is not mandatory with twist lock pipe.
Figure 18
NOTE: Sealant is not required to assemble fi replace
venting. Do not use silicone sealant at the inner fl ue
exhaust connections.
To make it easier to assembly the joints, we suggest put-
ting a lubricant (Vaseline or similar) on the male end of the
twist lock pipe prior to assembly.
Male End
Female End
Screw Holes
TWL100
Figure 18 –
Twist-lock Pipe Joints
VENTING INSTALLATION
REAR VENT INSTALLATION ONLY
Install the 4" (102 mm) inner vent pipe to the appliance
inner collar and secure with three (3) stainless steel sheet
metal screws.
Figure 19.
Install the 7" (178 mm) outer
vent pipe to the appliance outer collar. Secure pipe to the
rear cover plate using the tabs and three (3) sheet metal
screws.
Figure 20.
If a 45° or 90° elbow is being used, at-
tach the elbow to the appliance in the same manner then
attach the venting to the elbow.
Sheet Metal
Screws
4" Inner
Pipe
Figure 20 –
Install 7" Outer Vent Pipe
FP3001a
Figure 19 –
Install 4" Inner Vent Pipe
FP3031
Sheet Metal Screw
7" Outer
Pipe