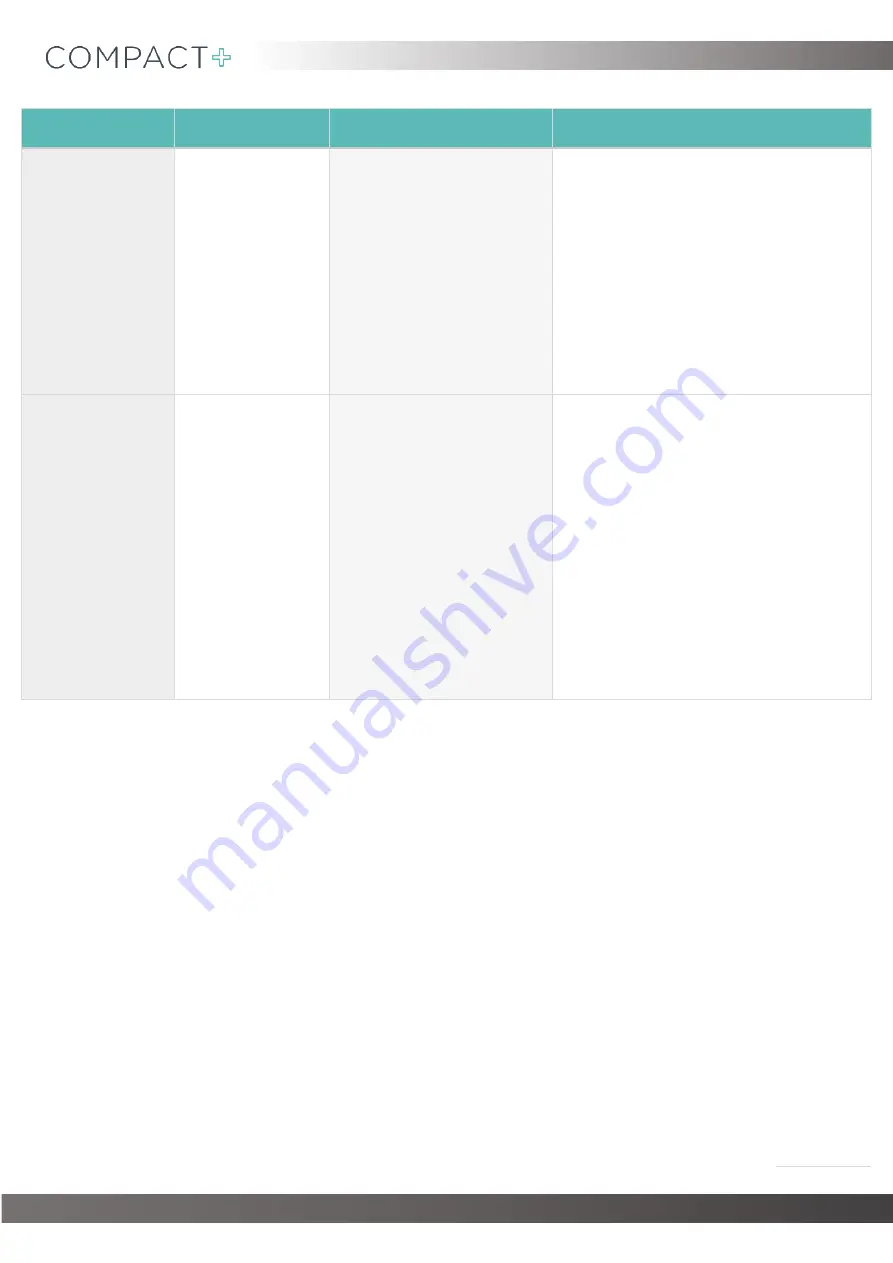
Vernacare Compact Plus Technical Manual-
Revision 2-Issued by N.Shields 14.2.2020
Page | 42
FAULT
EXPLANATION
OPERATOR CORRECTIVE
ACTIONS
MAINTENANCE CORRECTIVE
ACTIONS
Disposable
Products Not
Cut At End of
Cycle
Overloading
machine
Insufficient water
in hopper
Blades not turning
Run another cycle, if issues
persist, call maintenance
Check pump for correct operation (use
engineers function). Check in-line fuse to
pump.
Check pipework for blockages
Check drain valve is sealing correctly
Check if motor turns. Check that safety
switch is operating correctly. Check for
error codes on inverter
Lid Does Not
Move
Foot sensor not
working
Lid interlock stuck
or not working
Lid motor not
working
Magnetic clutch
worn/not working
Drive shaft broken
or damaged
Call maintenance
Check foot sensor operation, recalibrate
if required
The lid can be manually opened by
removing the front cover and manually
withdrawing the lid lock using the lever
beneath the lock. The lid can then be
opened against the magnetic clutch.
Open the small covers next to the hinges
to check operation of the lock, motor,
clutch and to inspect the connection
between motor and lid
Summary of Contents for COMPACT+
Page 1: ......