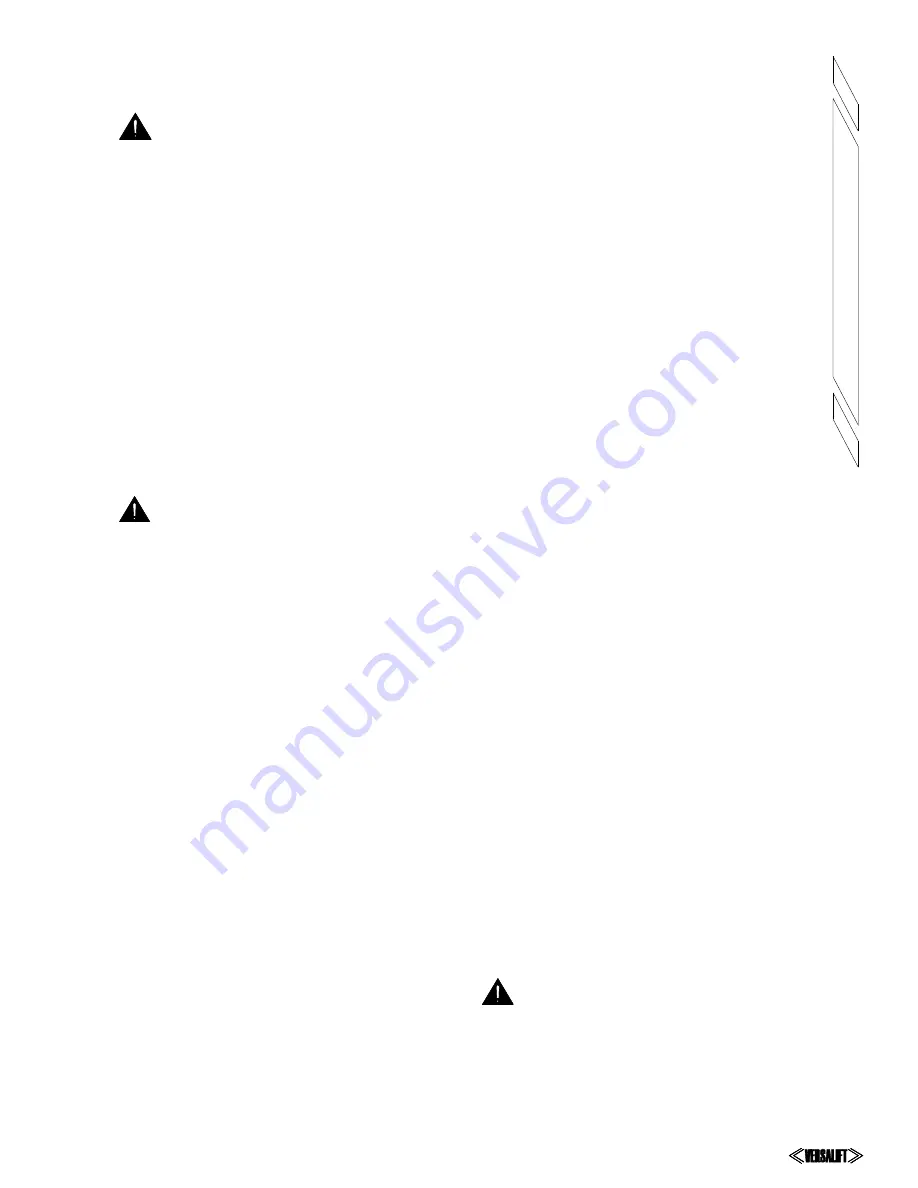
4-3
TEL-29-N/NE
OPERA
TION
WARNING:
WHEN THE BOOM IS
CONTROLLED MANUALLY FROM THE CONTROL
VALVE, THE ELECTRICAL LIMIT SWITCH WILL
NOT PREVENT OVER ROTATION. DO NOT
ROTATE MORE THAN 180° FROM THE STORED
POSITION.
Operating Procedures At The Platform:
Complete the start-up procedure from the ground
before selecting the upper controls. Verify that the
upper-boom tie-down strap is disengaged when
entering the platform. Safety regulations require the
operator be secured with a personnel restraint system
to the lift. The lanyard shall be attached to the safety
belt/harness and the other end connected to an
anchor located on the inner boom. The safety belt
must be rotated so that the lanyard connection is
centered on the back of the operator.
DANGER:
NEVER OPERATE ANY
AERIAL EQUIPMENT WITHOUT WEARING AN
APPROVED PERSONNEL RESTRAINT SYSTEM
ATTACHED TO THE SPECIFIED ANCHOR.
FAILURE TO SECURE THE SAFETY BELT AND
LANYARD MAY RESULT IN DEATH OR SERIOUS
INJURY IN THE EVENT OF A FALL FROM THE
P
LATFORM.
PLATFORM LOCK -
Versalifts with gravity leveling
are equipped with a positive platform locking pin
which prevents movement of the platform. This
feature is not to be used while the lift is being
raised
or lowered
, but is to be used as a way to eliminate
platform swing while the lift is stationary. The locking
mechanism is located on the upper telescoping
section of the boom, just above the platform pivot
point. The platform locking pin has two positions.
When the pin is fully engaged in the “platform locked”
position, the platform will not swing. When the pin is
pulled out and locked, the bucket will gravity level
itself.
To lock the platform in position
, rotate the pin
counter-clockwise until the spring pulls the pin into
the boom. The pin should catch one of the locking
holes. If the platform still swings, it may be necessary
to rock the platform until the pin fully engages. In
this position, the platform will not level when the
boom is moved.
To deactivate the platform lock
, pull the pin out of
the boom and rotate it clockwise until the pin stays
disengaged. If the pin is under load, it may be
necessary to rock the platform in the opposite
direction to pull the pin freely. In this position, the
platform will be free to level when the boom is moved.
The platform lock should always be disengaged
while
raising or lowering
the lift.
To activate lift movement,
the master control switch
must be activated in conjunction with the desired lift
function control switch. See this section for further
details and a diagram of the upper control panel.
To terminate any lift movement,
allow the control
switch to return to the centered or neutral position.
The upper controls have been designed to provide
convenient and comfortable access for the operator.
These controls are also carefully protected from
damage. Two or three controls may be operated
simultaneously, depending on the platform load and
which functions are being operated. If the platform
is heavily loaded and the two controls being operated
require high pressure (e.g. “extend” and “raise”) the
total system pressure may exceed the setting of the
relief valve. This causes oil to bypass the relief valve.
This is not detrimental to the aerial lift but results in
noise and reduced operating speeds and should not
be done. Practice and experience will prove
invaluable in becoming proficient with the aerial lift
controls.
Operating Where Electrical Hazards Are Present:
It is imperative that the operator of the aerial device
understand the dangers associated with operating
near electrical hazards. Due to the work involved,
the ordinary uses of aerial lifts often place the
operator, others in the platform, and ground crew in
the vicinity of electrical lines and equipment where
grave danger exists. These dangers can only be
avoided by the constant care of an operator who is
aware of these dangers, knows the limitations of the
aerial lift, and knows how to protect himself and the
crew from these dangers. Maintain safe clearances
from electrical power lines in accordance with
applicable government regulations. Allow clearance
for boom, platform, electrical line, and load line sway
and deflection.
DANGER:
ALL COMPONENTS IN
THE PLATFORM AREA, INCLUDING THE
CONTROLS, JIB POLE, COVERS, ETC. SHALL
BE CONSIDERED ELECTRICALLY CONNECTED,
AND NOT INSULATED OR ISOLATED. THESE
COMPONENTS MAY CONDUCT ELECTRICITY
RESULTING IN DEATH OR SERIOUS INJURY.
Summary of Contents for TEL-29-N
Page 2: ......
Page 4: ......
Page 6: ......
Page 8: ...1 2 TEL 29 N NE INTRODUCTION Figure 1 1 Model TEL 29 N NE Nomenclature ...
Page 11: ...2 3 TEL 29 N NE RESPONSIBILITIES SAFETY ...
Page 20: ...3 6 TEL 29 N NE SPECIFICATIONS ...
Page 22: ...3 8 TEL 29 N NE SPECIFICATIONS ...
Page 24: ...3 10 TEL 29 N NE SPECIFICATIONS ...
Page 25: ...3 11 TEL 29 N NE SPECIFICATIONS ...
Page 26: ......
Page 34: ......
Page 38: ......
Page 42: ...6 4 TEL 29 N NE DAILY VISUAL INSPECTION ...
Page 44: ...6 6 TEL 29 N NE DAILY VISUAL INSPECTION ...