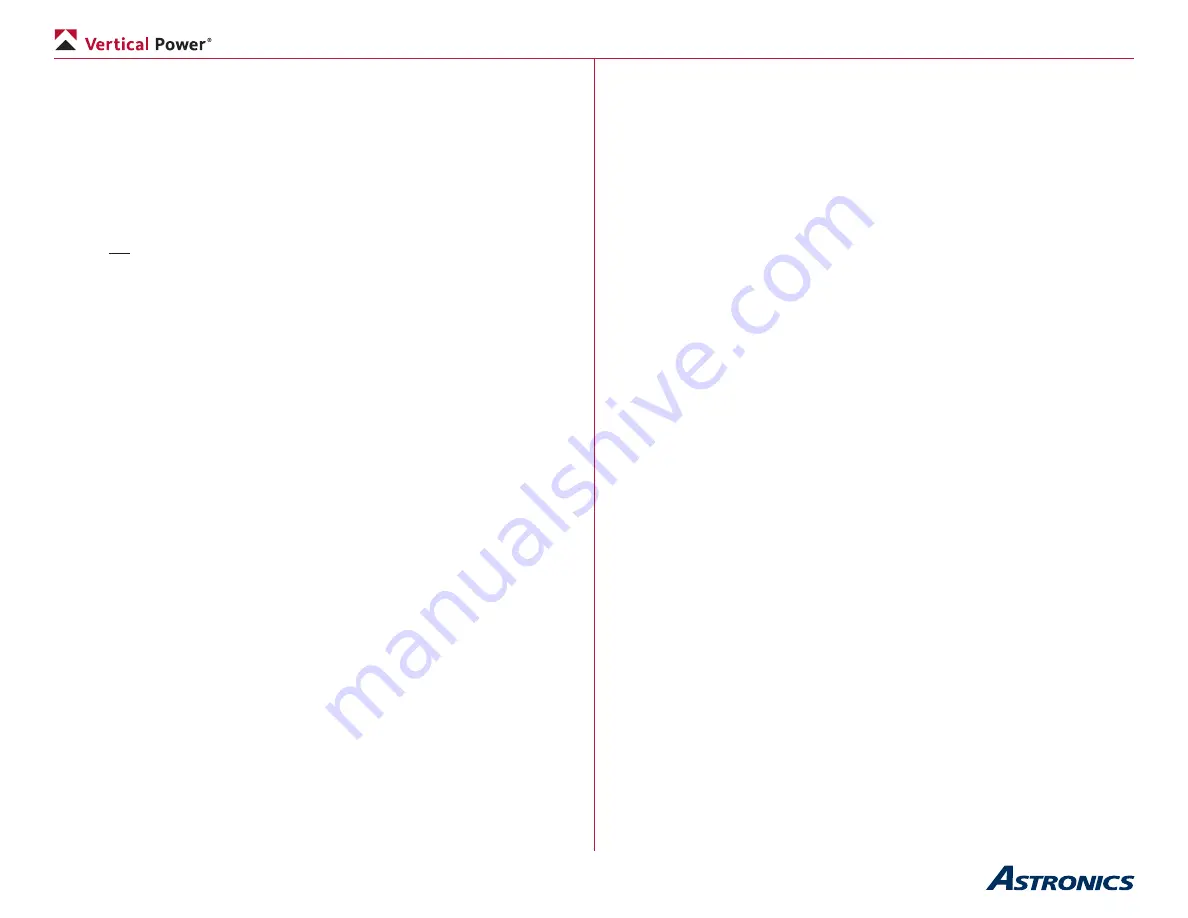
Page 70
VP-X Installation and Operating Manual
Rev. D (August 5, 2020)
10.5f Continuous Flaps
When enabled, you can command flaps past the next flap down stop before
the flaps stop.
For example, if you have flaps 0, 20, and 40 degrees and the flaps are up,
you can press the flap down switch twice (push - push) and the flaps will go
all the way to 40 degrees. The first time you press the flap down switch, the
flaps are commanded to go to 20 degrees. The next time you press it the
flaps are commanded to go to 40 degrees.
If this is not
enabled, you must wait until the flaps reach the next stop before
pressing the flap down switch to go to the next one.
10.6 Landing Light Wig-Wag
If enabled, the forward lights (landing and/or taxi) can be configured to wig-
wag (pulse) when turned on. The wig-wag system incorporates the following
features:
•
Pulsing starts automatically above a specified airspeed, so the lights
are steady on the ground but pulsing in the air for increased visibility.
• Warm-up before pulsing. The lights will remain on steady for the
specified period of time before pulsing begins. There is a minimum
five-second warm-up period to allow the system to detect any circuit
faults.
• Pulsing can be manually stopped by pressing WIG-WAG STEADY
soft key on the EFIS. Press WIG-WAG AUTO to set back to
automatic control. Consult the EFIS manual for specific instructions.
The landing and or taxi lights must be turned on to wig wag. The lights only
wig wag if the device(s) is turned.
10.7 Circuit Faults
A circuit fault can be caused by the following conditions:
1. Short circuit: the wire is grounded, either momentarily or permanently
2. Over-current: the electrical load exceeds the circuit breaker value
3. Current fault: the device is drawing no current for three seconds
when turned on. This is user-configurable on all circuits except trim,
flaps, and starter.
When a fault occurs, the VP-X turns off the circuit. It remains OFF until the
fault is manually reset using the EFIS screen. Consult the EFIS manual for
specific instructions related to clearing the fault.
10.8
Starter Disable
The starter circuit is normally on, meaning the starter switch has power at all
times when the engine is not running.
The starter circuit is automatically turned OFF whenever the engine RPM is
valid and is above 600 RPM. You cannot manually turn the starter circuit on
and off.
10.9
Low-Voltage Alarm
A low voltage condition is detected and reported by the EFIS.
10.10
Over-Voltage Alarm
The VP-X detects an over-voltage condition, which generally occurs because
either the voltage regulator or alternator has failed in a manner that allows
the alternator to produce higher voltage levels than normal.
When an over-voltage condition is detected, the active alternator (either the
primary or backup) is turned OFF and an alarm is displayed on the EFIS
screen.
You can reset the faulted alternator circuit in the same way you reset any
other faulted circuit. The alternator switch cannot turn the alternator back on
until the fault is cleared.
Because the alternator circuit is disconnected, you will shortly get a low-
voltage alarm. When this happens you can switch to the backup alternator.
10.11 Battery Contactor Failure
If the battery contactor fails, power is lost to the main bus and therefore the
VP-X. Turn on the backup circuits to provide power to devices wired with
backup circuits.
10.12
Backup Circuits
The VP-X allows an unlimited number of backup circuits. Each backup circuit
is wired directly to the battery bus through a separate and independent fuse
and switch. If a backup switch is turned off, the VP-X controls power to the
device. Turning on a backup switch powers the device independently of the
VP-X.
The backup switches provide power to their respective devices even after
the VP-X shuts off. Remember to turn off backup power after it is no longer
needed or when shutting down the aircraft.