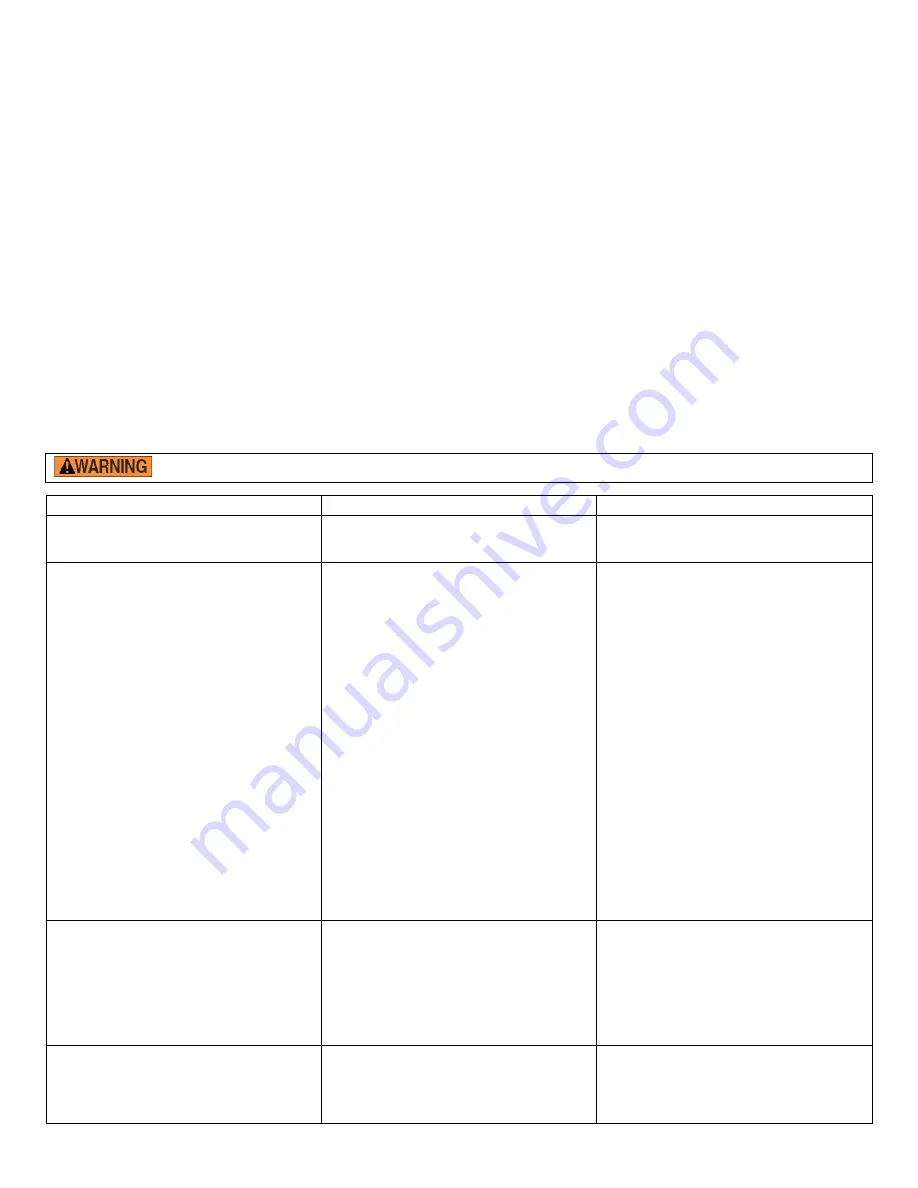
rev. 11/1/2016
CB-PMPS, manual.doc
Copyright 2016 Vestil Manufacturing Corp. Page 18 of 23
VELOCITY FUSE:
There is a brass velocity fuse with a stainless steel spring in the base of each cylinder. In the event of a hydraulic hose
or fitting failure, the platform starts to lower at a fast rate. As soon as the descent speed exceeds the preset speed, the
Velocity Fuse will shut off the oil flow and the platform will remain nearly stationary until pressure is reapplied. This safety
feature reduces the possibility of accidental personal injury or damage to the pallet handler or load
If air enters the system, the velocity fuse might activate although no failure occurs. To reset the velocity fuse, activate
the pump by jogging the
UP
button. Immediately after resetting the velocity fuse, fully lower the carriage and remove the
load from the forks. Cycle the carriage all the way to the top of the mast and back down several times to purge air from
the system.
AIR BLEED PROCEDURE:
If the forks descend very slowly or fail to lower at all, air probably is trapped in the hydraulic circuit and must be bled
from the system. The Pallet Server utilizes a bleeder screw at the top of the cylinder. To bleed air from the hydraulic
circuit, follow these directions.
1.) Completely unload the forks.
2.) Loosen the bleeder screw at the top of the cylinder with approximately a 1/4 to 1/2 turn to allow trapped air to escape.
Jog the motor to push air out of the system.
4.) When the cylinder is free of air only clear hydraulic fluid will flow from the bleeder screw fitting. When you observe only
oil flowing from the bleeder, retighten the bleeder screw.
DC-POWERED HYDRAULIC SYSTEM TROUBLESHOOTING GUIDE
Before performing maintenance on this product, unload the forks and completely lower the carriage.
Observation
Possible Cause
Remedy
1.
Unit does not raise, motor does not run
a. Low battery voltage
.
(Check light)
b. All chassis connections to negative post
of battery not made well.
a. Recharge battery
b
.
Check and tighten or clean connections
if necessary.
2. Unit does not raise but motor is running
or humming.
c.
Voltage at motor terminals might be too
low to run pump at existing load.
d. Fluid level in reservoir is low.
e. Load exceeds capacity requirements
.
Relief valve is allowing hydraulic fluid to
flow back into the reservoir
.
f. Suction filter is clogged, starving pump.
g
.
Suction line may be leaking air, due to
loose fittings.
h. Filter/Breather cap on tank might be
clogged.
i. Lowering solenoid valve might be
energized by faulty wiring or might be stuck
open
.
j
.
Hydraulic pump might be inoperative.
c. Measure voltage at motor terminals or
as near as possible, while pump is running
under load. Check for loose connections.
d
.
Add fluid. Refer to Owner's Manual for
proper fluid levels
.
e. DO NOT CHANGE RELIEF VALVE
SETTING. Instead, reduce the load to
rated capacity.
f. Remove and clean.
g. Inspect all fittings for proper tightness.
h. Remove and clean
.
i.
Remove lowering solenoid valve. Check
and clean.
(Refer
to “Lowering Solenoid
Valves”.)
j. Disconnect hydraulic line at power unit.
Put pressure line in a large container and
operate
the
pump. If no output
,
check the
pump motor coupling which may be
defective, and correct as necessary
.
If
pump is worn
,
consult factory for
replacement parts.
3.
Unit rises too slowly
.
k
.
Foreign material stuck in down solenoid
valve, causing some fluid to flow back into
the reservoir.
l. Foreign material clogging suction filter, or
breather cap, or a hose is pinched.
m. Low motor voltage
.
n. Unit overloaded.
o. Inoperative pump.
k. Lower the deck
.
Remove the down
solenoid valve and clean
.
(Refer to
Hydraulic Section of Owners Manual).
l
.
Correct as necessary. (See also
,
2(f),
(h)).
m
.
See 2 (b)
n
.
See 2 (e)
o. See 2 (j)
4.
Motor labors or is excessively hot.
p. Voltage may be low.
q. Oil starvation causing pump to bind &
high internal heat develops. If this occurs,
pump can be permanently damaged.
r. Binding cylinders.
p. See 2 (b)
q
.
See 2 (d), (f)
,
(g)
,
(h), (j)
r
.
Align cylinders correctly.