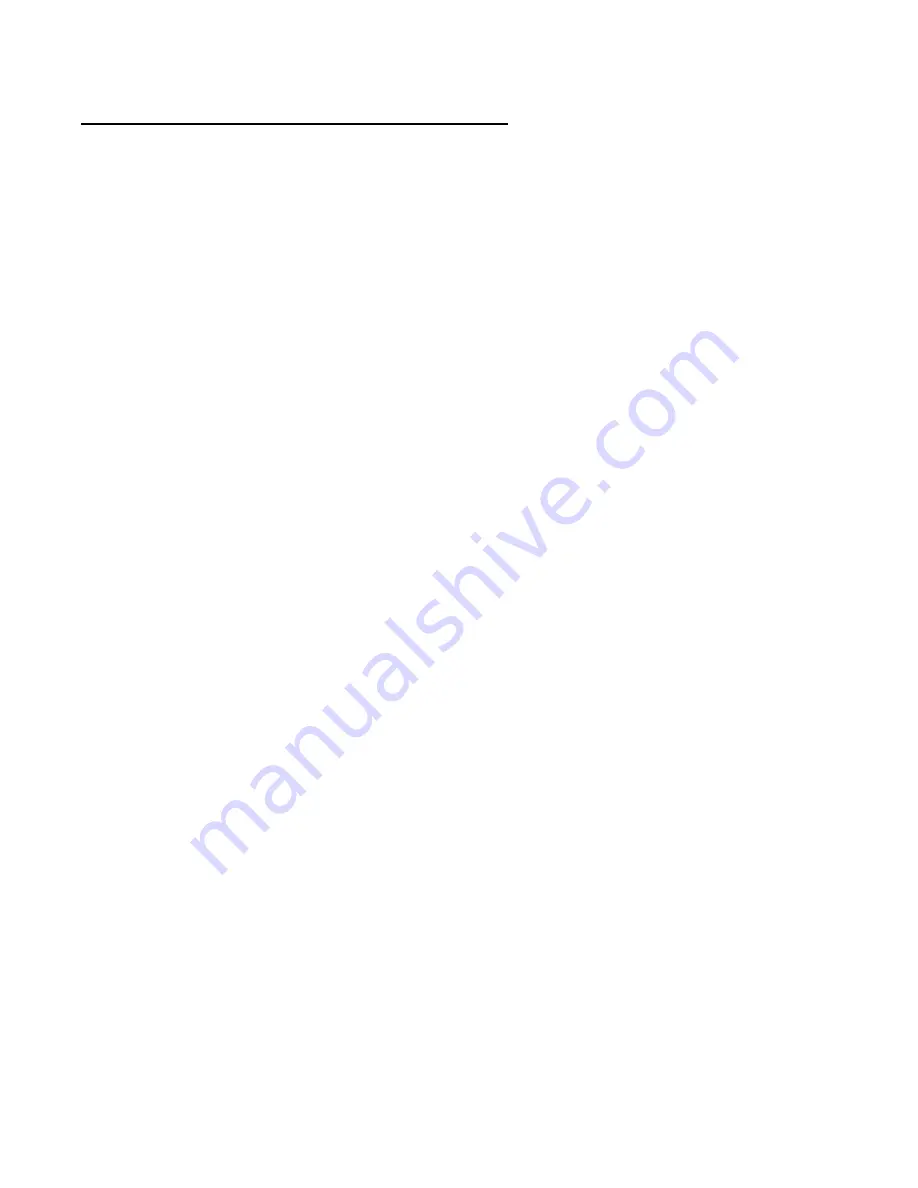
Procedures for adjusting hydraulic valves and pressure switches:
1. Install pressure gauges in ports GA and UL GA (see FIGS. 6 & 7 respectively on p. 7D):
[NOTE: Hose fittings and adaptors might be necessary to connect the gauges to these ports.]
a. Remove the cap plugs from port GA and install a 3000psi gauge into the port. The port is located
under the directional valve; then
b. Remove the cap plug from port UL-GA and install a 3000psi gauge into the port, which is located
under the sequence valve (pointed towards the motor).
2. Prepare the pressure switches:
a. Using a standard (flathead) screw-driver, loosen the set-screws through the knurled knobs on
both of the pressure switches (see FIG. 6, p. 7B); then
b. Turn the knurled ring of each pressure switch clockwise until they can turn no farther.
3. Turn the adjustment hex flats on the relief valve (See FIG. 7 on p. 7D; labeled RV) out all the way, by
turning it counterclockwise.
4. Turn the selector-switch on the control box to “COMPACT”.
5. Press the cycle start button on the control box.
a. Hold the button until the motor engages.
b. While the motor operates, the hydraulic cylinder extends and the platen descends towards the
bottom of the enclosure.
6. Adjust the unload valve:
a. When the cylinder is fully extended and while the motor continues to run, adjust the unload valve
(in port SV) until the UL GA pressure gauge reads 1000 psi. Typically, adjustment requires
turning the valve clockwise rather than counterclockwise.
7. Adjust the relief valve:
a. With the motor running, observe the reading on the gauge connected to the GA port.
b. Begin turning the adjustment hex of the relief-valve (“RV”) clockwise. [Note: As pressure
approaches 1000 psi, you will hear a change in sound as the unload valve--adjusted in step 6--
shifts into the unloaded position.]
c. Continue to increase the RV setting until the GA gauge displays 1500 psi.
8. Adjust the upper pressure switch (in port PS2):
a. With the power unit now adjusted and operating at 1500 psi pressure, decrease the setting on
PS2;
b. Rotate the knurled knob counterclockwise until it clicks. The click indicates that the directional
valve shifted. Consequently, the cylinder will retract and lift the platen to the raised position and
the power unit will turn off.
9. Adjust the lower pressure switch (PS1):
a. Turn the selector switch on the control box to “CRUSH”.
b. Press the cycle start button and hold it until the motor engages.
c. While the power unit runs,
i. Increase the RV valve setting until the gauge displays 3000 psi.
ii. Turn the knurled knob on the pressure switch in port PS1 (lower pressure switch)
counter-clockwise until it clicks. The click indicates that the switch is open.
Simultaneously, the valve shifts and the platen will rise.
iii. Turn the knob counter-clockwise an additional 1/8 turn.
10. Return the crusher to service:
a. Run the crusher through a complete cycle in each mode (COMPACT and CRUSH) to confirm
that the machine is functioning normally.
b. Remove the pressure gauges and reinstall the cap plugs into ports GA and UL GA.
c. Tighten the set screws to fix the positions of the knurled knobs
of PS1 and PS2
.
Page
7D
Summary of Contents for HDC-900
Page 8: ...6 33 72 35 6 17 Page 7A SORGHG 3DUWV LDJUDP RI 3RZHU 8QLW...
Page 13: ...Page 8 FIG 9 Electrical system diagram...
Page 15: ...M 14 2 4 3 1 12 11 7 8 13 15 9 6 10 5 16 Page 10 FIG 10 Hydraulic System Diagram...
Page 16: ...Data Label 221 305 206 220 248 251 By Oil Fill 300 203 2 Page 11 Label placement diagram...