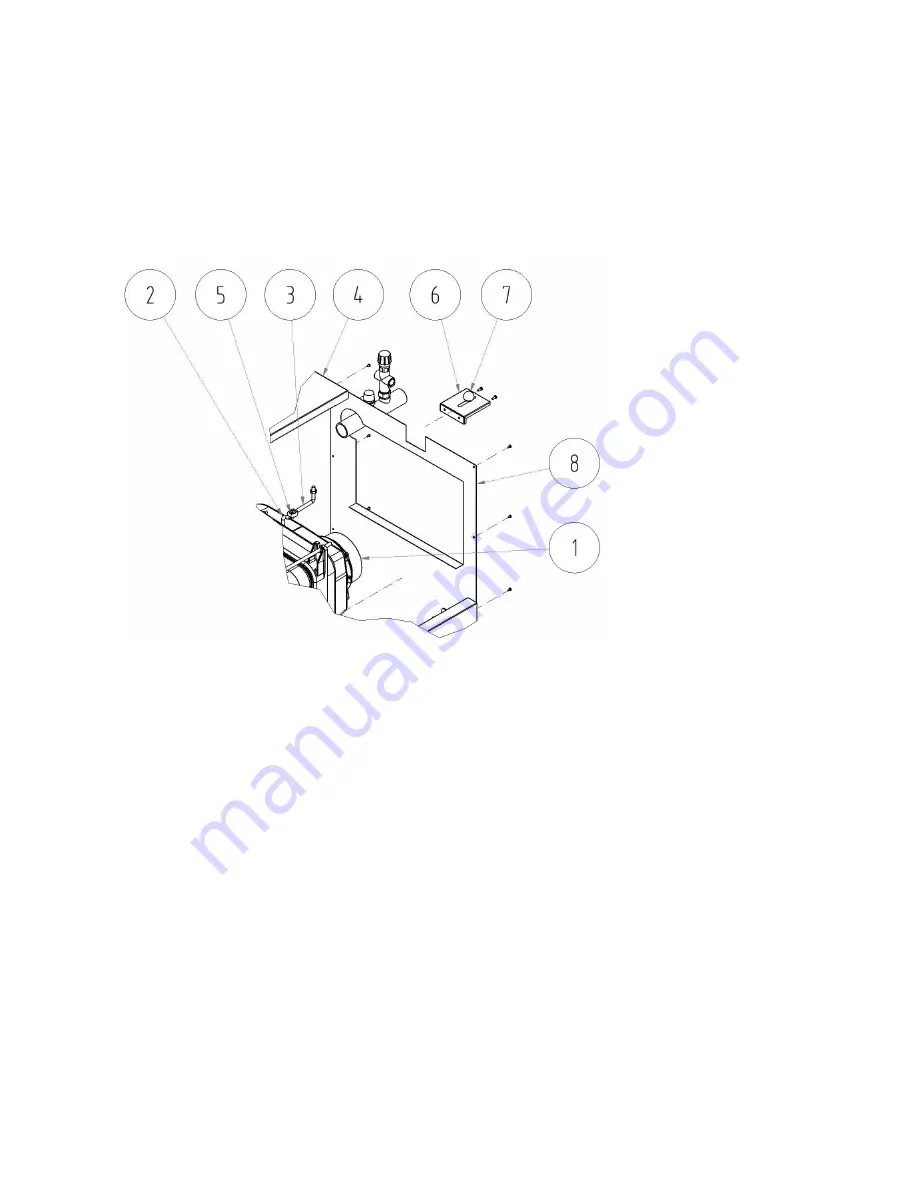
16
To insert the keeper pin and to fit the washer 10,5 into the partition of the smoke extension piece. To
mount the pull rod on the partition of the smoke extension piece and to secure it with the washer 10,5
and the keeper pin - To screw up the nut M 10 on the pull rod.
13. To equip the upper cover part with 4 pcs of spring clips and to fit them on the side cover part.
14. To screw up the rear cover part with use of 10 pcs screws ST 4, 2x9, 5.
15. To screw up to the upper cover part the pull rod console with use of 2 pcs of screws M5x12. To locate
the pull rod of the smoke control into the oval opening into console and to secure with the plastic ball
M10.
16. To fit on the draught regulator the pull rod with chain let (in accordance with attached Manual of draught
regulator).
17. To locate ash pan and small ash pan according to the Fig. no. 3.
Fig. no. 8
Installation of the smoke control pull rod
Note: Before stoking it is necessary to open the partition in smoke adaptor by means of the draw
bar of smoke control. Thus the flue gases are discharged through the shorting opening into
the chimney.
Assembly tools for brush
Use the leather gloves and common assembly tools for mounting or dismounting of the brush and the spike
point (if they are included in the delivery)
.
Filling the heating system with water:
The water hardness must correspond to
Č
SN 07 7401 and it is inevitable to treat the water according
to Chap. no. 5.1. in case the water hardness is unsatisfactory.
The heating systems with an open expansion tank allow the direct contact between the heating water and
the atmosphere. During the heating season the water expanding in the tank absorbs the oxygen, which
increases its corrosive effects and at the same time the water evaporates heavily. Only the water treated to
the values according to
Č
SN 07 7401 can be used for refilling.
The heating system must be thoroughly flushed out in order to wash out all impurities.
During the heating season it is necessary to keep a constant volume of heating water in heating system and
be particular about bleeding the heating system to avoid the air suction into the system. Water from the
boilers and heating system must never be discharged or taken for usage except in cases of emergency like
the repairs etc. Water discharge and filling with new water increases the danger of corrosion and scale
development. In case we have to refill the heating system with water we only do this operation when
the boiler is cold in order to prevent its sections from getting broken.
After boiler and heating system refilling operation the all joints must be tested for tightness.
When using the two way safety vent DBV 1 - 02 the cooling water is added gradually to the to the
reverse water.
The assembly and stoking test completion must be recorded in the “Guarantee certificate”.
1
Smoke extension piece
2
Partition of the smoke
extension piece
3
Pull rod of smoke control
4
Upper cover part
5
Keeper pin
6
Console of pull rod
7
Plastic ball M10
8
Rear cover part
Summary of Contents for Hercules U 24
Page 30: ...30 ...
Page 32: ...32 Updating date 6 2013 GB ...