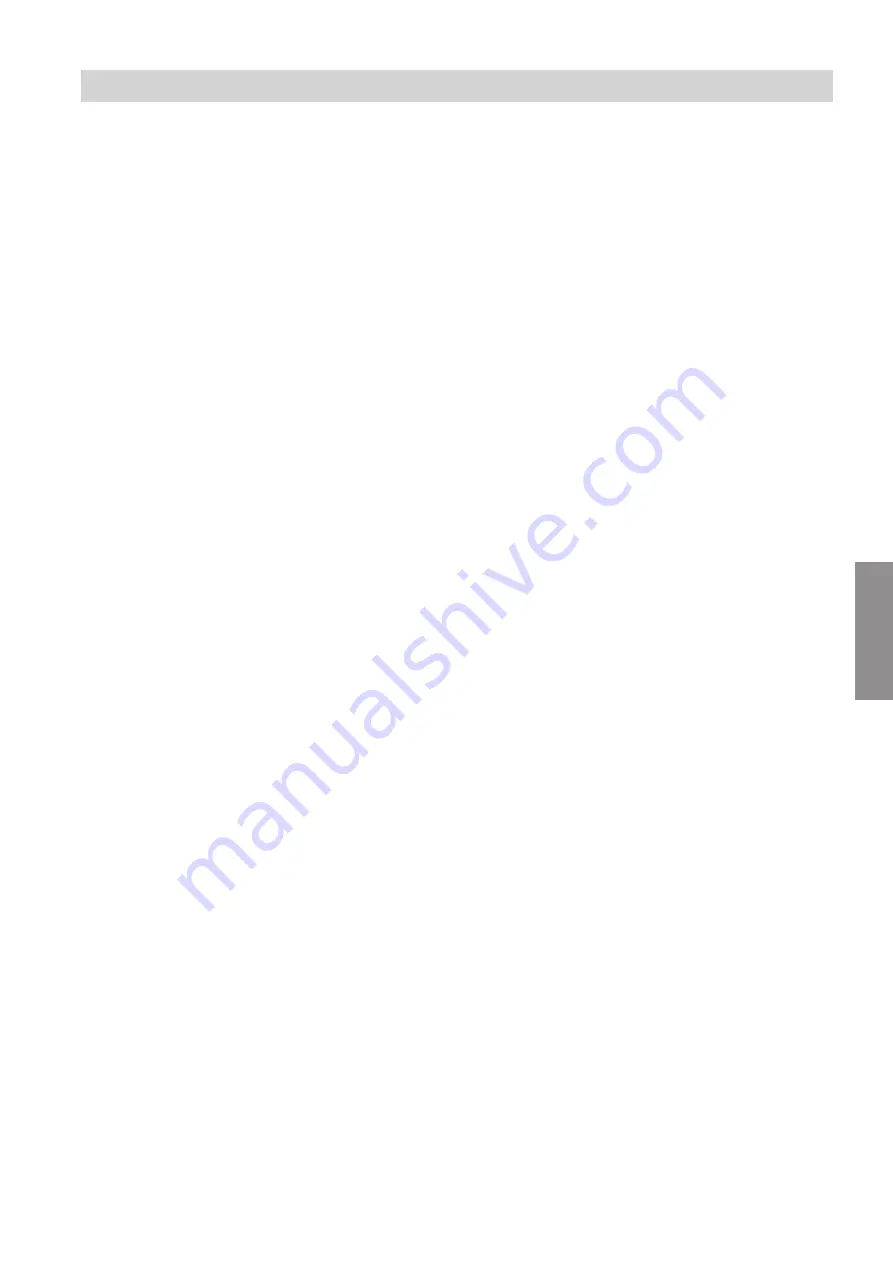
27
Viessmann products can be recycled. Components
and substances from the system are not part of ordi-
nary household waste.
For decommissioning the system, isolate the system
from the power supply and allow components to cool
down where appropriate.
All components must be disposed of correctly.
Decommissioning and disposal
Final decommissioning and disposal
5461424
Appendix