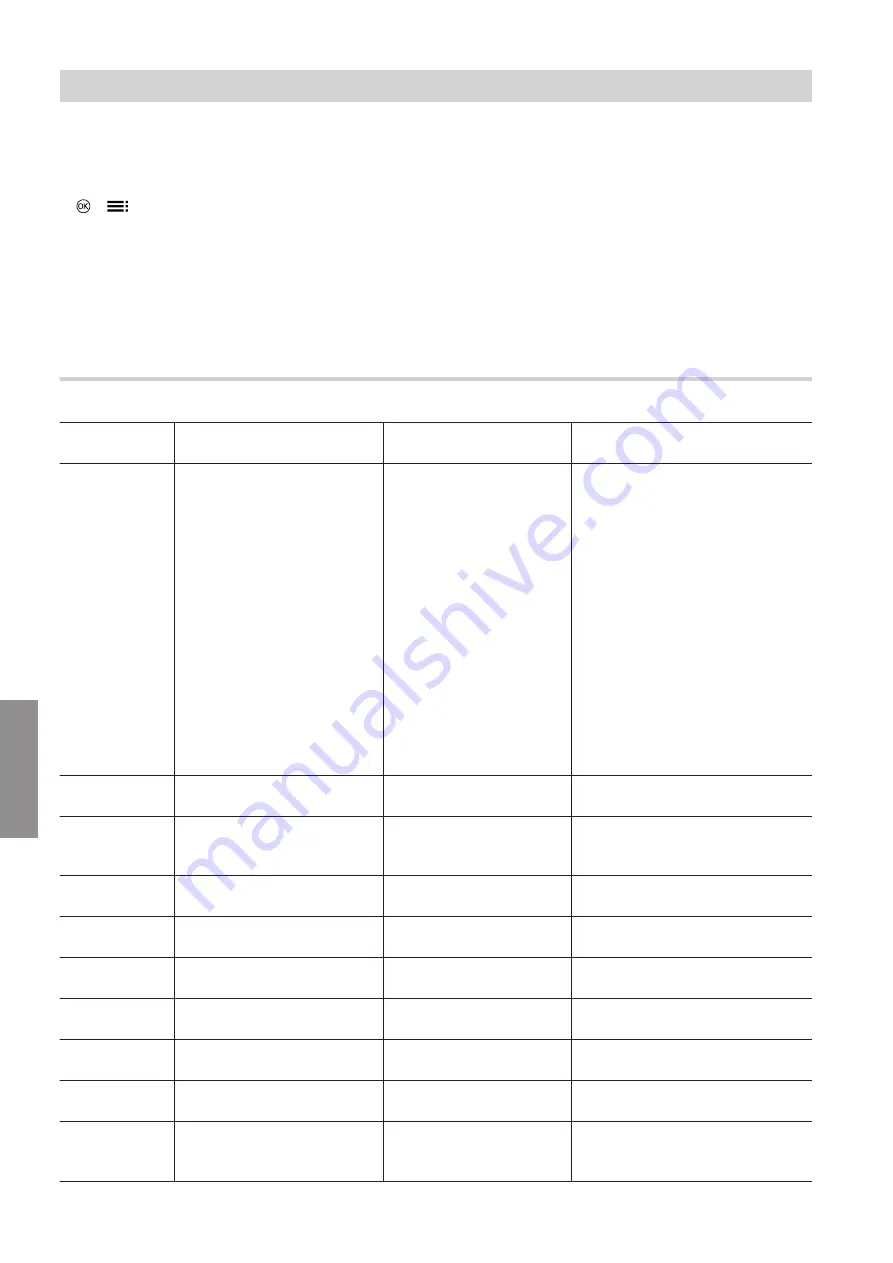
52
Deleting the fault codes from the fault memory
Press the following keys:
1.
+
Simultaneously for approx. 4 s.
The
"Service"
menu appears.
2.
|
/
~
For
"Fault history"
.
3.
d
To confirm.
4.
|
/
~
For
"Delete?"
.
5.
d
To confirm.
6.
|
/
~
for
"Yes"
.
7.
d
To confirm.
8.
ä
repeatedly, until the standard display
is shown.
Fault codes
Fault code dis-
played
System characteristics
Cause
Measures
AA
■
Boiler circuit pump on
■
Valve of return temperature
raising facility open
■
Buffer cylinder control valve
open
■
Too much wood charged
■
Incorrect set value se-
lected at programming
unit
■
Faulty system compo-
nent (boiler circuit pump,
valve of the return tem-
perature raising facility
or temperature sensor)
■
Activate
"Transfer heat"
func-
tion.
■
Check the heating water temper-
ature before heat up and before
recharging fuel. Can the expec-
ted energy be drawn off or stor-
ed?
■
Check the boiler circuit pump,
valve of the return temperature
raising facility and temperature
sensor.
■
Undo the dust cap on the high
limit safety cut-out and press the
reset button (only possible once
the boiler water temperature is
<70 °C) and acknowledge the
fault.
20
Control mode
Short circuit, boiler water
temperature sensor
Check boiler water temperature
sensor.
21
Control mode
Short circuit, return tem-
perature sensor for the
boiler
Check the return temperature sen-
sor for the boiler.
22
Control mode
Short circuit, flue gas tem-
perature sensor
Check flue gas temperature sen-
sor.
24
Control unit set to 0 °C out-
side temperature
Short circuit, outside tem-
perature sensor
Check outside temperature sensor.
25
No DHW heating
Short circuit, top buffer
temperature sensor
Check top buffer temperature sen-
sor.
26
Control mode
Short circuit, centre buffer
temperature sensor
Check centre buffer temperature
sensor.
27
Control mode
Short circuit, bottom buffer
temperature sensor
Check bottom buffer temperature
sensor.
30
Control mode
Lead break, boiler water
temperature sensor
Check boiler water temperature
sensor.
31
Control mode
Lead break, return tem-
perature sensor for the
boiler
Check the return temperature sen-
sor for the boiler.
Troubleshooting
Fault display
(cont.)
5684984
Diagnosis