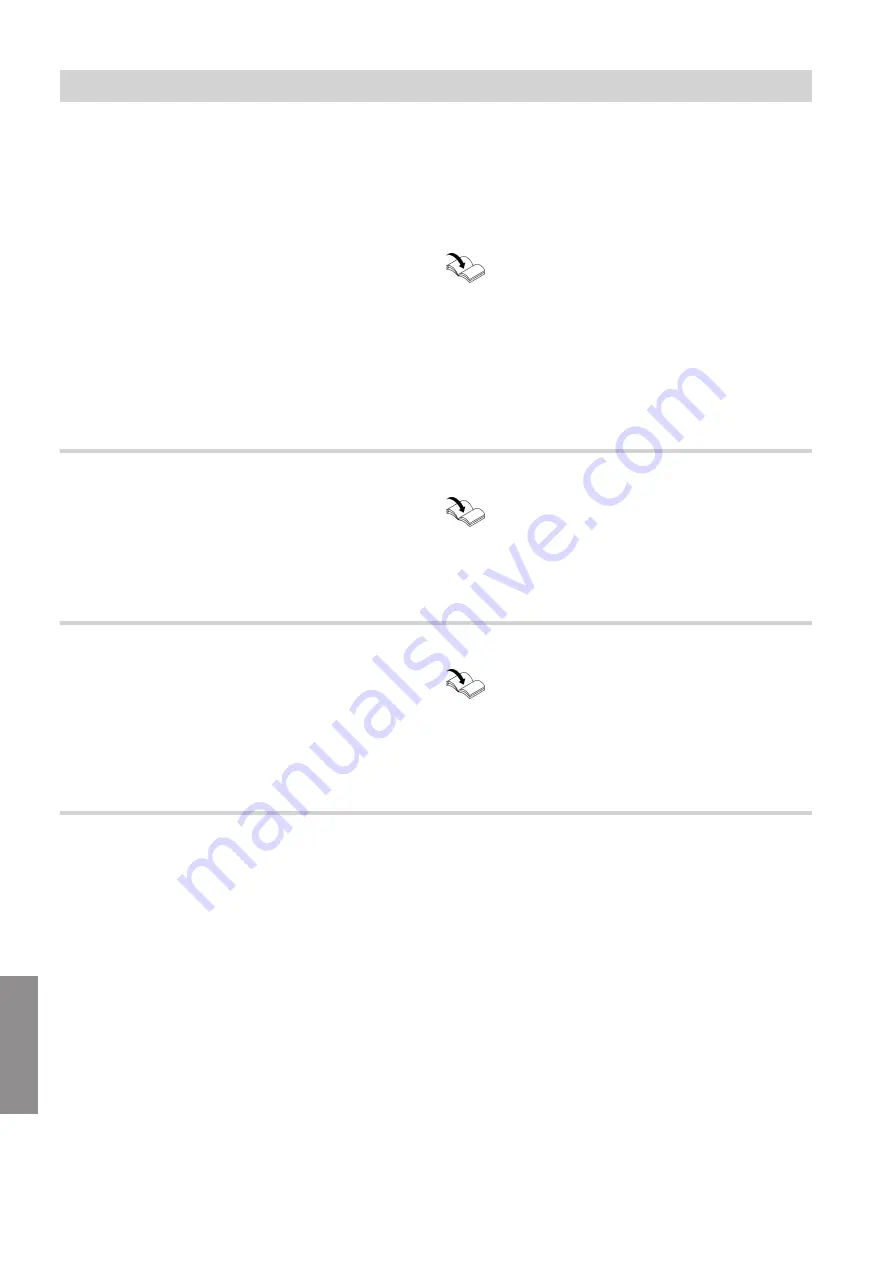
98
Heating mode
The control unit determines a set flow temperature for
the heat generator, subject to the outside temperature
or the room temperature and the slope/level of the
heating curve.
The determined set flow temperature is transferred to
the burner control unit. The burner control unit calcu-
lates the modulation level from the set and actual flow
temperatures and regulates the burner accordingly.
The electronic temperature limiter inside the burner
control unit limits the flow temperature.
Heating circuit pump connection for heating circuit
without mixer
Only for systems with several heating circuits.
If a heating circuit without mixer is connected down-
stream of the low loss header, the circulation pump
can be connected to output P2. The function of the
output is set in the commissioning assistant.
To start the commissioning assistant: See "Com-
missioning, inspection and maintenance".
If output P2 is being used for another function, the cir-
culation pump can be connected to an EM-P1 exten-
sion (accessories).
Venting program
During the venting program, the circulation pump will
be alternately switched on and off for 30 s over a
period of 20 min.
The diverter valve alternates between heating and
DHW heating for a given time. The burner is switched
off during the venting program.
Activate venting program: See "Commissioning,
inspection and maintenance".
Filling program
In the delivered condition, the diverter valve is set to its
central position, so the system can be filled completely.
After the control unit has been switched on, the
diverter valve no longer goes into its central position.
If the system is to be filled with the control unit
switched on, the diverter valve is moved in the filling
program to its central position and the pump is started.
Activate filling program: See "Commissioning,
inspection and maintenance".
In this position, the control unit can be switched off and
the system can be filled completely. When the function
is enabled, the burner shuts down. The program auto-
matically becomes inactive after 20 min.
Heating curve
The heating curves represent the relationship between
the outside temperature and the flow temperature.
Simplified: The lower the outdoor temperature, the
higher the flow temperature must be in order to reach
the room temperature set point.
Factory settings:
■
Slope = 1.4
■
Level = 0
Note
If heating circuits with mixer are present in the heating
system: The flow temperature of the heat generator is
one differential temperature higher than the flow tem-
perature for the heating circuits with mixer. Differential
temperature in delivered condition set to 8 K.
The differential temperature can be adjusted using the
following parameters:
■
Heating circuit 2: Parameter 934.5
■
Heating circuit 3: Parameter 935.5
■
Heating circuit 4 (if installed): Parameter 936.5
Function description
Control functions
6130884
Functions