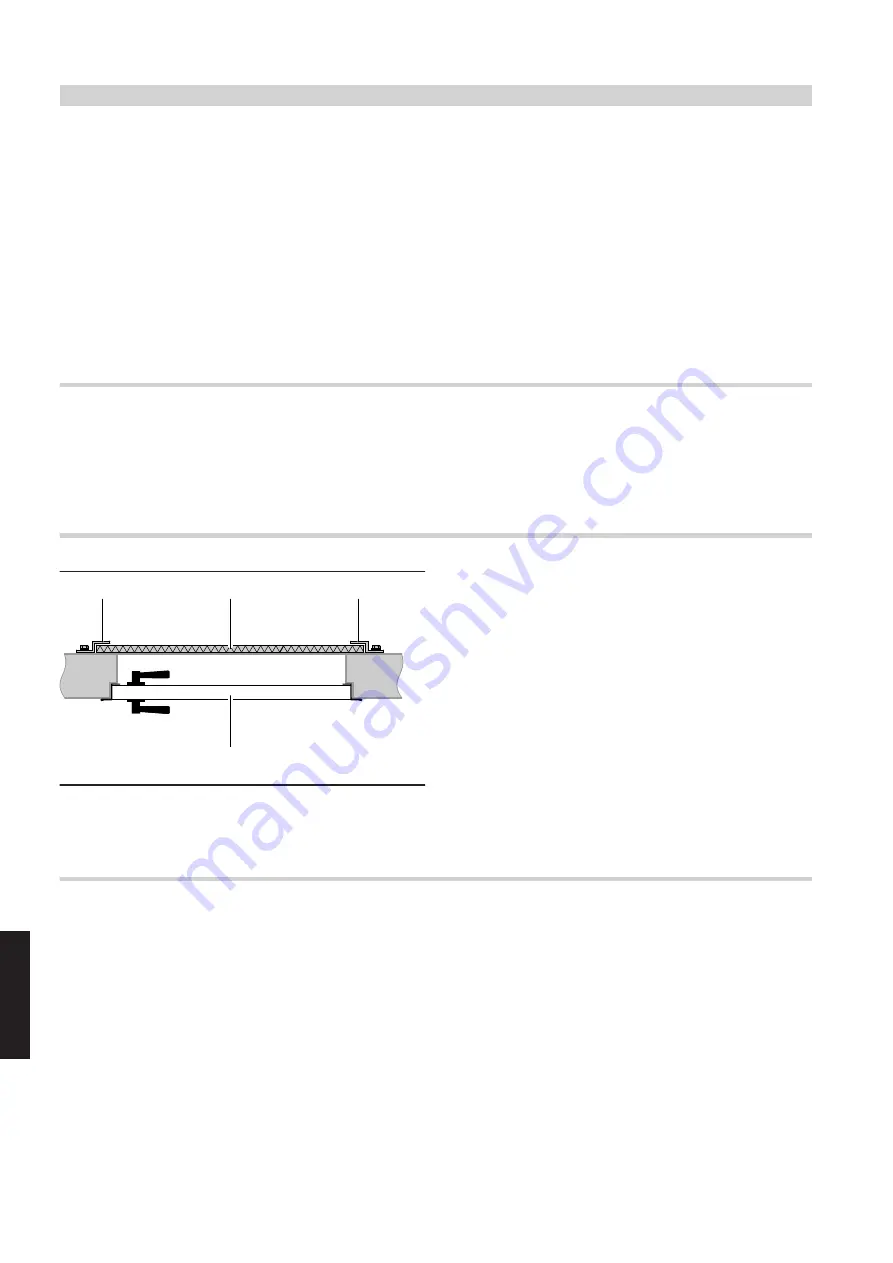
■ The pellet storage room must be inaccessible to children. The pel-
let boiler should be shut down approximately one hour before the
storage room is filled. The storage room should be sufficiently ven-
ted before anyone enters.
■ The sloping floor in the pellet storage room should preferably be
made from wood-based materials and have a smooth surface.
Three-ply shuttering panels and multi-layer plywood boards have
proven useful in practice. Plain chipboard is not suitable however.
Note
To ensure a permanent fault-free fuel supply to the boiler, the fuel
store must be cleaned regularly. This includes carefully removing
fines in the fuel store. After two to three deliveries, the fuel store
should be cleaned prior to the next pellet delivery. Over time, pellet
dust accumulates in the lower part of the fuel store and can cause
faults in the fuel supply. Wood pellets of inferior quality with an
increased percentage of fines cause increased accumulations of
dust in the storage room. However, fines are also produced by the
mechanical stresses that wood pellets are subjected to during trans-
port and injection (injection pressure, installations, etc.) into the stor-
age room. With its strict requirements for wood pellets, the ENplus
certificate ensures flawless pellet quality. This involves monitoring
the entire value chain from production to delivery. Manufacturers and
suppliers of high quality wood pellets as well as further information
can be found at www.enplus-pellets.de.
Additional safety instructions for pellet stores
■ Access by unauthorised persons is forbidden and doors must be
kept locked.
■ Smoking, fires and other sources of ignition are prohibited.
■ Risk to life due to odourless carbon monoxide (CO) and a lack of
oxygen
■ Before entering, ensure sufficient ventilation is in place – keep
door open while inside.
■ Entry is only permitted under the supervision of a person standing
outside the storage room
■ Risk of injury caused by moving parts
■ Ensure filling is carried out under the conditions stipulated by the
heating system installer and pellet supplier
■ Protect the wood pellets from moisture.
Protective boards with Z brackets
A
B
A
C
A
Z bracket (length 2000 mm)
B
Protective board (30 mm thick; on-site)
C
Door to the storage room
Z brackets are available as accessories for installation of the protec-
tive boards.
To facilitate the addition or removal of protective boards, do not
install Z brackets up to the ceiling.
Fill connector and return air connector
■ Arrange the connectors so that no overpressure can develop in the
pellet storage room during the filling process. The return air con-
nector must remain free from blockage at all times.
■ The connectors should be located high up inside the pellet storage
room to enable the room to be filled to the maximum. To prevent
pellets hitting the ceiling, the fill connector must be at least 20 cm
below the ceiling. (Fit a protective panel if the ceiling is plastered.)
■ Ideally, the connectors should be located on the narrow side of the
storage room.
■ With straight fill connectors, the fill width is approx. 4 - 5 m.
■ If 2 x 45° bends are located before the inlet into the storage room,
fit a straight pipe of at least 0.5 m length on the other side to pro-
trude into the storage room. This enables the pellets to reach the
required filling velocity and therefore the required fill width.
Earth
The connectors must be earthed to prevent static charging during
the filling process. We recommend connecting each pipe element to
the equipotential bonding of the building. At the very least, connect
each pipe element securely to the brickwork, either by setting the
pipe into the brickwork (without thermal insulation) or by means of
pipe clips anchored into the brickwork.
Fuel storage
(cont.)
72
Viesmann
VITOFLEX 300-UF
7
5682428