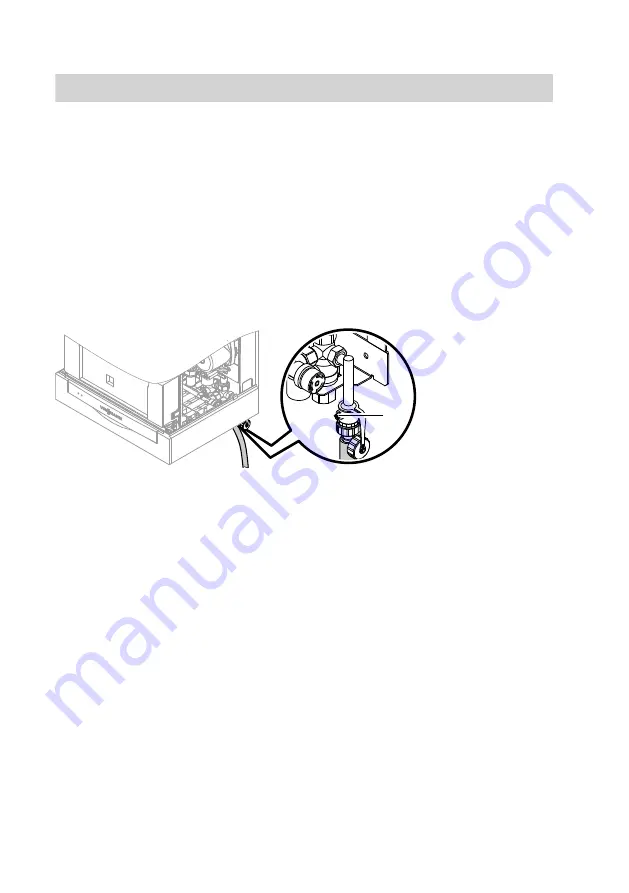
8
Filling the heating system
!
Please note
Unsuitable fill water increases the level of deposits and corrosion and may
lead to boiler damage.
■ Thoroughly flush the entire heating system prior to filling it with water.
■ Only use fill water of potable quality.
■ Soften fill water with hardness exceeding 3.0 mol/m
3
, e.g. using a small
softening system for heating water (see Viessmann Vitoset price list).
■ An antifreeze additive suitable for heating systems can be mixed with the
fill water. The antifreeze manufacturer must verify its suitability.
A
1.
Check the pre-charge pressure of the
diaphragm expansion vessel.
2.
Fill the heating system via boiler fill &
drain valve
A
in the heating return
(at the connection set or on site).
(Minimum system pressure
0.8 bar).
Note
If the control unit has not been
switched ON prior to filling the sys-
tem, then the servomotor of the
diverter valve will still be in its central
position, and the system will be com-
pletely filled.
3.
If the control unit had already been
switched ON before filling began:
Switch ON the control unit and acti-
vate the fill program via coding
address "2F:2".
Note
To call up code 1 and for setting the
coding address, see page 36.
4.
Close boiler fill & drain valve
A
.
5.
Close the shut-off valves on the heat-
ing water side.
Commissioning, inspection, maintenance
Further details regarding the individual steps
5692 799 GB
Summary of Contents for VITOLADENS 300-W
Page 5: ...5 Keyword index 104 Index Index cont 5692 799 GB ...
Page 106: ...106 5692 799 GB ...
Page 107: ...107 5692 799 GB ...