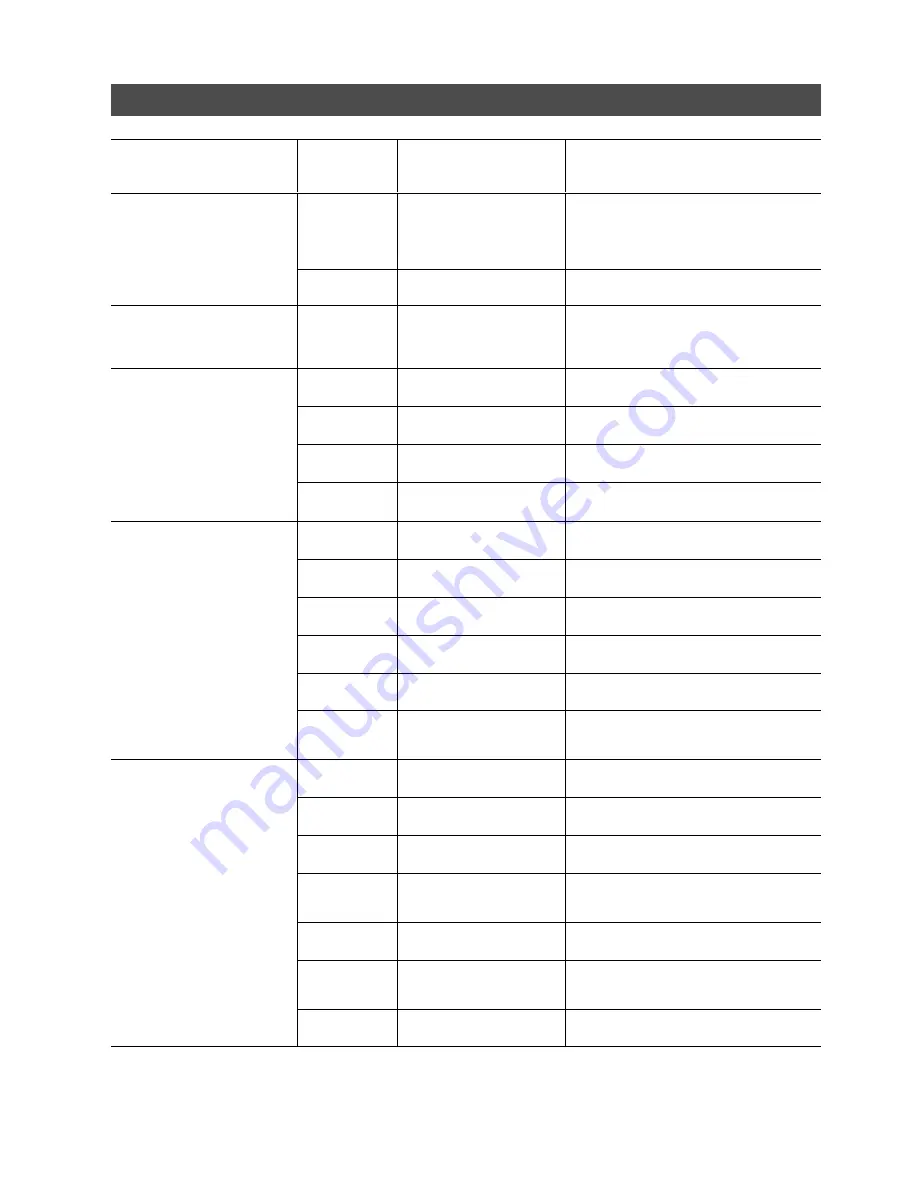
Troubleshooting
19
Diagnosis
Fault/system characteristics
Flashing code
red
at LMO14
Cause of fault
Check
Burner does not start (no fault
display), signal lamp does not
illuminate
No voltage
Check fuse or connector
aBÖ
in control
unit, or check electrical connections,
setting of heating system on/off switch
on control unit and mains electrical
isolator
High limit safety cut−out
activated
Press reset button on boiler control unit
Burner does not start (no fault
display), signal lamp
illuminates
10× flashes
DDDDDDDDDD
Faulty electrical
connection, wires"L1"
and "N" interchanged or
faulty burner control unit
Check electrical connection
If phases are correctly connected,
replace burner control unit
Burner does not start up (with
fault)
2× flashes
DD
Motor faulty
Replace motor
2× flashes
DD
Coupler between motor
and oil pump faulty
Replace coupler
2× flashes
DD
Oil pump seized or stiff
Clean or, if necessary, replace oil pump
8× flashes
DDDDDDDD
Oil pre−heater faulty
Replace oil pre−heater
Burner starts up, but no flame
is formed
2× flashes
DD
Ignition electrodes
incorrectly adjusted
Adjust correctly (see page12)
2× flashes
DD
Ignition electrodes damp
and contaminated
Clean ignition electrode block
2× flashes
DD
Insulation of ignition
electrode cracked
Replace ignition electrode block
2× flashes
DD
Ignition transformer faulty Replace ignition transformer
2× flashes
DD
Ignition cable faulty
Replace ignition cable
2× flashes
DD
Pump does not feed oil
Install pressure and vacuum gauges on
pump and check build−up of pressure
(see following paragraph)
Pump does not feed oil
2× flashes
DD
Shut−off valves closed at
filter or in oil pipe
Open valves
2× flashes
DD
Filter blocked
Clean filter (pre−filter and pump filter)
2× flashes
DD
Coupler between motor
and pump faulty
Replace coupler
2× flashes
DD
Leak in suction line or
filter cup
Tighten connections
Check oil pipes and connections for leaks
and tighten if necessary
2× flashes
DD
Oil flow and return hoses
interchanged
Connect correctly acc. to instructions on
pump
2× flashes
DD
Vacuum in suction line too
high (higher than 0.35bar)
Check cross−section of oil pipes. Replace
filter
Check external fuel oil valve
2× flashes
DD
External fuel oil valve
faulty
Check and, if necessary, replace external
oil valve
5692452 GB