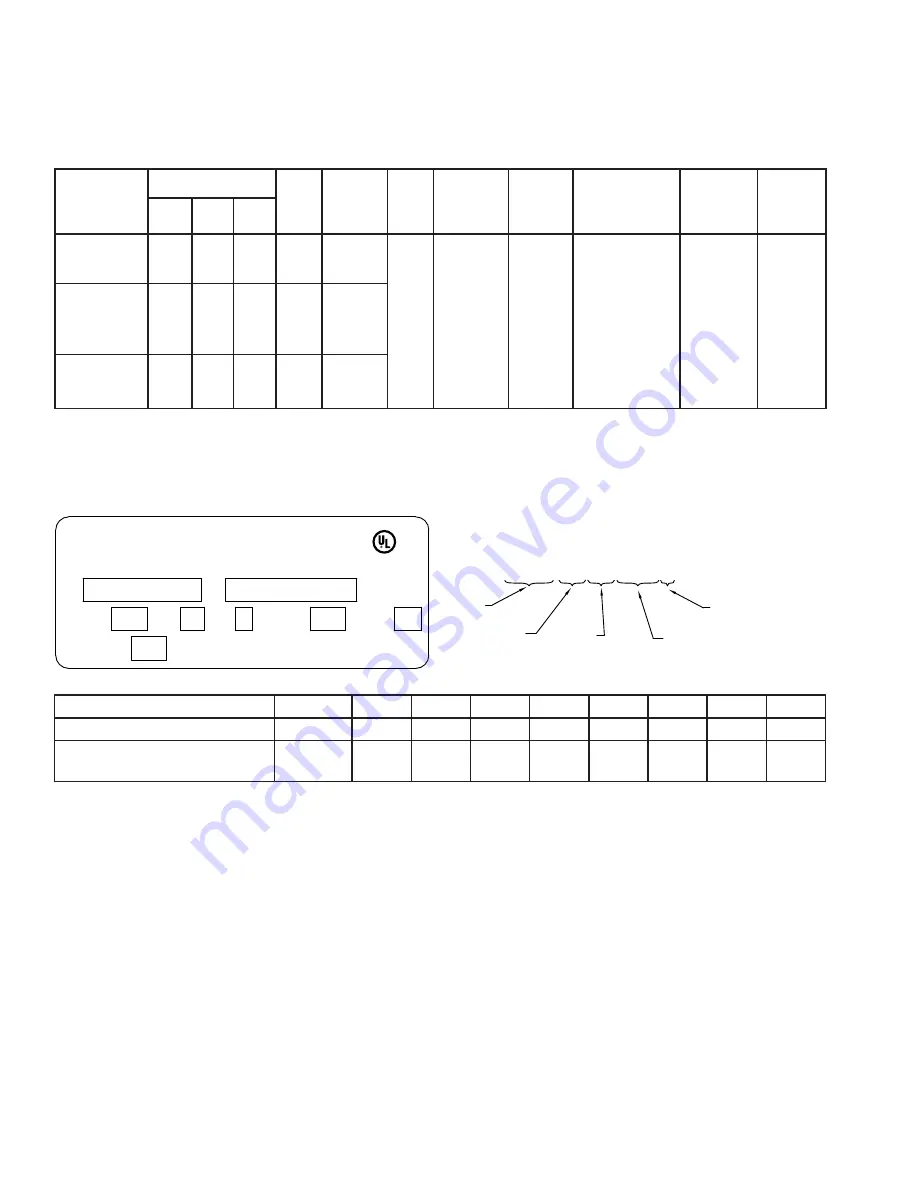
General Information
4
SMR-0003
© Viking Range Corporation
Use an appropriate work area and location when
•
performing repairs. You will find that it is easier to
repair undercounter units if they are set on a raised
platform or workbench.
Always wear protective safety glasses and gloves
•
when working on any Viking product.
Any refrigerant, whether CFC, HCFC, or HFC (R-12,
•
R-22, or R-134a), must be recovered. Federal
regulations prohibit the intentional venting or release
of refrigerants during the service repair or disposal
of an appliance.
Before Servicing
Always disconnect power to any Viking product
•
before attempting to service it. Always verify that
power has been disconnected.
If the unit has been running, use caution around the
•
condenser and copper tubing. These areas may be
very hot.
Use caution around the condenser fins and
•
baseplate edges. These areas are sharp.
Refrigerant is under high pressure. Always evacuate
•
any system before attempting to open it.
Reasonable care and safe work methods should
•
be practiced when working on any Viking product.
Never work with energized electrical equipment in
wet or damp areas.
Unit Specifications
The unit specifications will vary among the models listed in this service manual. See chart below for unit
specifications related to the model that you are servicing.
Wine Cellar, Beverage Center & Refrigerated Drawers Unit Specifications
Model
Cabinet Dimensions (in)
Weight
(lbs)
Refrigerant
Charge
(oz)
Power
Cord
Length
(ft)
Compressor
Type
System
Refrigerant
Control
Temperature
Control
Condenser
Fan Motor
Evaporator
Fan Motor
Height
Width
Depth
DFUW144
DUWC144
VUWC144
34
23 ⅝
24 ¼
166
2.8
7
Piston type
Capillary
tube
Electronic Control
with LED display,
thermistor input,
and Tru Protect™
2.3 W 1300
RPM
12VDC
DFUR143/144
DUAR143/144
VUAR143/144
34
23 ⅝
24 ¼
166
3.6
DFRD144
DURD144
VURD144
34
23 ⅞
24 ¼
170
3.6
Serial Nameplate
The serial nameplate is located inside of the unit on the upper left hand wall. The serial number will need to be given
when inquiring about the unit or ordering parts. See illustration below for a sample serial tag with manufacturing date
code logic.
YYYYMMDDSSSA
DETAIL "B"
YEAR
MONTH
DAY
SERIAL
ASSEMBLY SITE
MODEL NO.
SERIAL NO.
BTU/HR
R134A
OZ
TEST PRESSURE
"J" PSI LOW SIDE
"K" PSI HIGH SIDE
905L
LISTED
HOUSEHOLD
C
"A"
AMPS
PH
HZ
VOLTS
DETAIL "B"
"C"
"D"
"E"
"F"
"G"
"H"
REFRIGERATOR
GREENWOOD, MISSISSIPPI 38930 USA
VIKING RANGE CORPORATION
A
B
C
D
E
F
G
H
J
K
DFUW, DUWC, VUWC 144
Detail B
115
60
1
440
3.3
2.8
140
300
DFUR, DUAR, VUAR 143/144
DFRD, DURD, VURD 144
Detail B
115
60
1
440
3.3
3.6
140
300