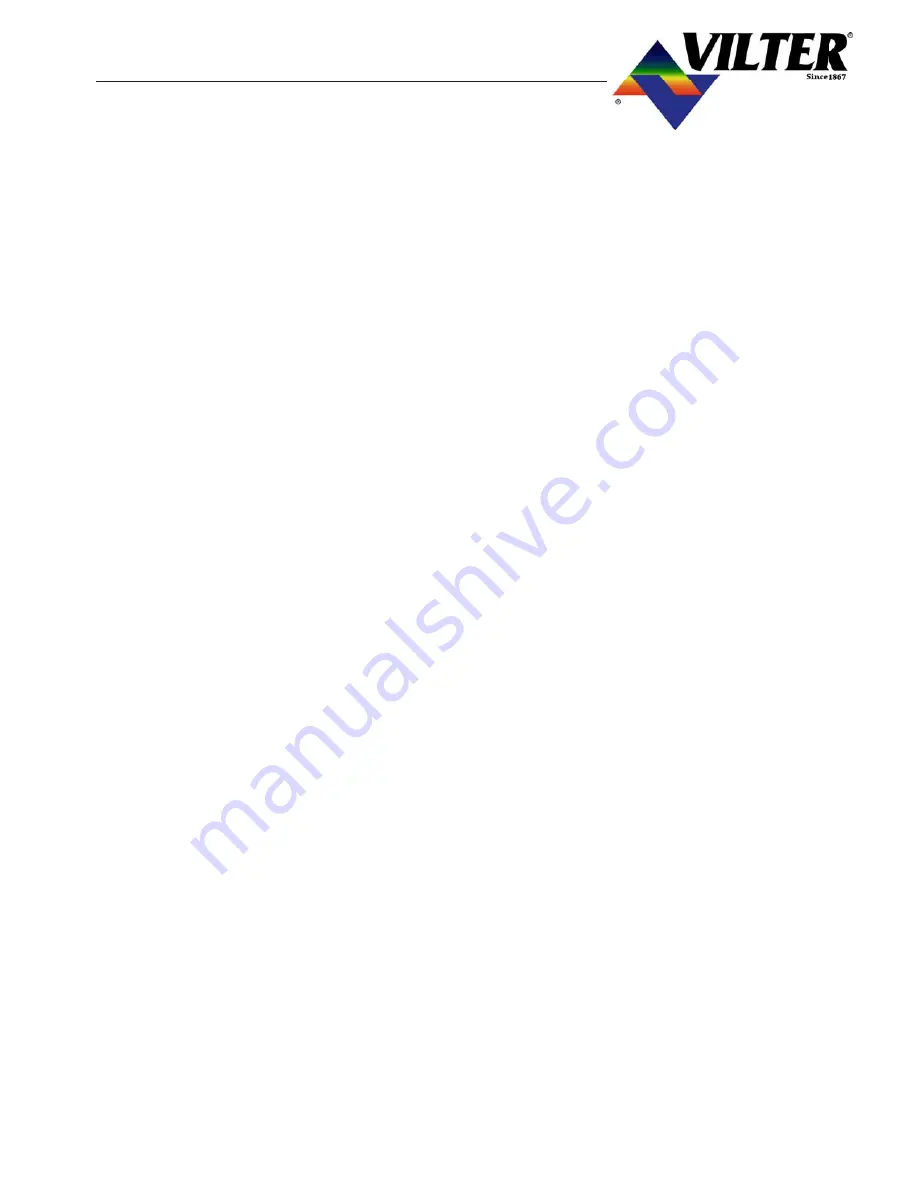
23
Installation
V.
ELECTRICAL CONNECTIONS
The single screw compressor units are shipped
with all package mounted controls wired. The
standard control power is 115 volts 60 Hertz,
single phase. If a 115 volt supply is not available,
a control transformer may be required. The power
source must be connected to the control panel ac-
cording to the electrical diagrams.
The units are shipped without the compressor
motor starter. Field wiring is required between
the field mounted starters and package mounted
motors.
Additional control wiring in the field is also re-
quired. Dry contacts are provided in the control
panel for starting the screw compressor motor.
These contacts are to be wired in series with the
starter coils. A current transformer is supplied
along with the compressor unit, and is located in
the motor junction box. This transformer is to be
installed around one phase of the compressor
motor starter. A normally open auxiliary contact
from the compressor motor starter is also required.
Terminal locations for this wiring can be found
on the wiring diagram supplied with this unit.
Additional aspects of the electrical operation of
the single screw units are covered in the start up
and operation section of this manual.
VI.
TESTING REFRIGERATION
SYSTEM FOR LEAKS
Vilter equipment is tested for leaks at the factory.
One the most important steps in putting a refrig-
eration system into operation is field testing for
leaks. This must be done to assure a tight system
that will operate without any appreciable loss of
refrigerant. To test for leaks, the system pressure
must be built up. Test pressures for various re-
frigerants are listed in ANSI B9.1-1971 code bro-
chure entitle “Safety Code for Mechanical Refrig-
eration”. These pressures will usually suffice,
however, it is advisable to check local codes as
they may differ. Before testing may proceed, sev-
eral things must be done.
First, if test pressures exceed the settings of the
system, relief valves or safety devices, they must
be removed and the connection plugged during
the test. Secondly, all valves should be opened
except those leading to the atmosphere. Then,
open all solenoids and pressure regulators by the
manual lifting stems. All bypass arrangements
must also be opened. Because of differences in
characteristics of the various refrigerants, two
different testing methods are necessary.
A.
Ammonia Systems
Dry nitrogen may be used to raise the pressure
in an ammonia system to the proper level for the
test. The gas may be put into the system through
the charging valve or any other suitable open-
ing. Adjust the pressure regulator on the bottle
to prevent over-pressurization. Do not exceed
the pressure rating on the vessel with the lowest
pressure rating.
Carbon Dioxide should NOT be used as a test-
ing gas in a system where ammonia is already
dissolved in any moisture remaining. This will
cause ammonium carbonate to precipitate when
the CO
2
is added. If heavy enough, this precipi-
tate may cause the machine to freeze and clog
the strainer.
A mixture of four parts water to one part liquid
soap, with a few drops of glycerin added, makes
a good solution. Apply this mixture with a one
inch round brush at all flanges, threaded joints,
and welds. Repair all visible leaks. If possible,
leave the pressure on over night. A small pres-
sure drop of 5 lbs. Over this period indicates a
very tight system.
Remember to note the ambient temperature, as a
change in temperature will cause a change in
pressure.
After the system is thoroughly tested, open all
valves on the lowest part of the system so the gas
will float away from the compressor. This pre-
vents any dirt or foreign particles from entering
the compressor and contaminating the working
parts. The oil should then be charged into the
compressor.
Summary of Contents for VSM 71-701
Page 1: ...1 VPN 35391S February 2006 Rev 05 Price 60 00...
Page 2: ...2...
Page 20: ...20...
Page 52: ...53 Pre Start Up Check List...
Page 99: ...99 Recommended Spare Parts List...
Page 104: ...104 Gate Rotor...
Page 110: ...110 Main Rotor VSS...
Page 112: ...112 Main Rotor VSR...
Page 114: ...114 Slide Valve Cross Shafts and End Plate...
Page 118: ...118 Capacity Slide Volume Slide Carriage Assembly Slide Valve Carriage Assembly...
Page 134: ...134 Miscellaneous Frame Components VSS Screw Compressor VSR Mini Screw Compressor...
Page 138: ...138 C FlangeAdapter Components 630 620 610 640 601 641 630 601 620 610 640 641 642 650 651...
Page 140: ...140 Replacement Parts Tools...
Page 144: ...144 GaterotorAssembly...
Page 148: ...148 Main Rotor Slide Valve Cross Shafts and End Plate Models 71 401 Only Counter clockwise...
Page 152: ...152 Main Rotor Slide Valve Cross Shafts and End Plate Model 501 701 Only Clockwise...
Page 154: ...154 Volume Ratio Capacity Slide Carriage Assembly Slide Valve Carriage Assembly...
Page 158: ...158 Miscellaneous Frame Components Model VSM 501 701 Model VSM 71 401...
Page 160: ...160 Replacement Parts Accessories Housing Accessories C Flange Assembly...
Page 166: ...166 Haight Pumps...
Page 170: ...3 Refrigerating Specialties Division...
Page 236: ......
Page 237: ......
Page 238: ......
Page 243: ......
Page 244: ...168...