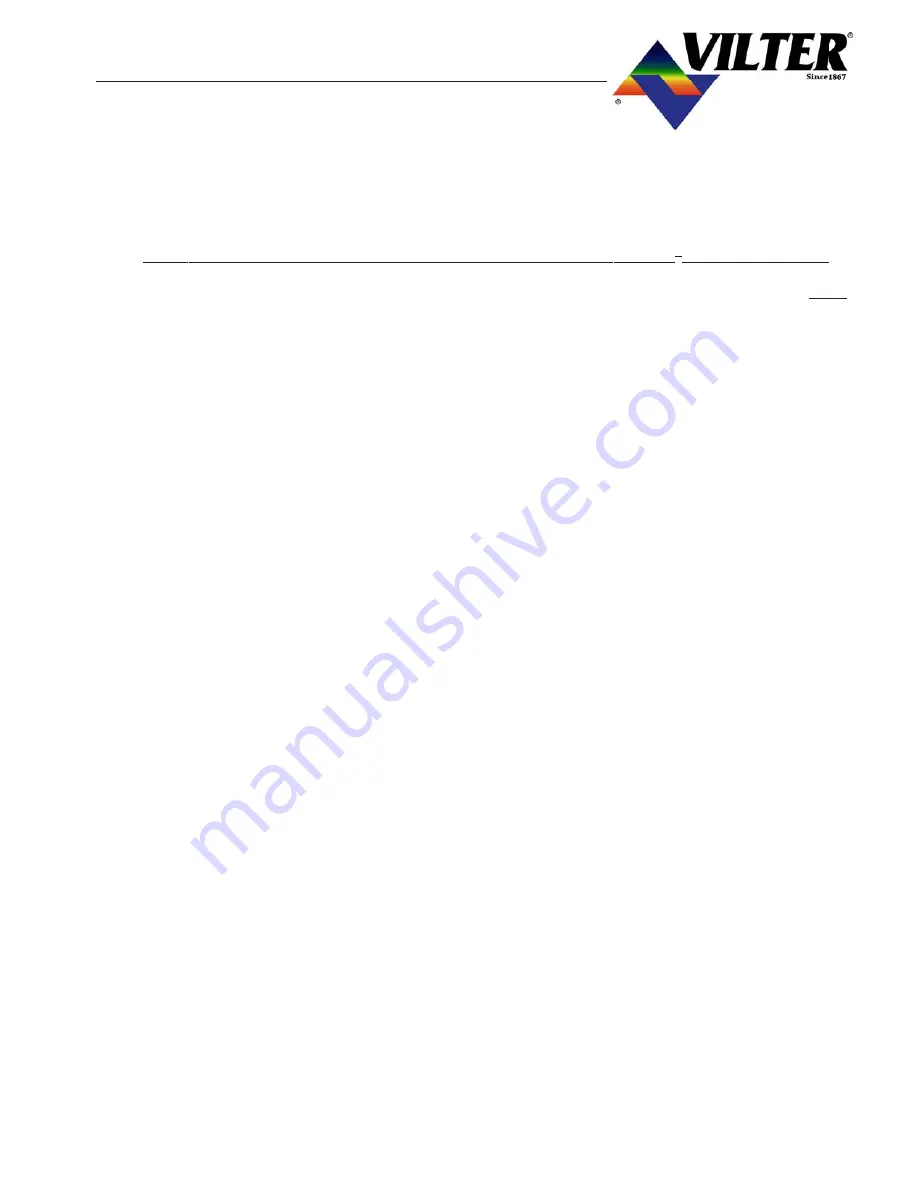
55
PRE START-UP CHECKLIST
FIELD WIRING REQUIREMENTS
VILTER MANUFACTURING CORPORATION
VRS SCREW COMPRESSOR, VSS/VSM SINGLE SCREW COMPRESSOR UNITS
PRESTART-UP CHECKLIST
FIELD WIRING REQUIREMENTS FOR UNITS WITH FACTORY WIRED
VISSION
®
MICROPROCESSORS
NOTE:
If startup service has been purchased, to save time and money, the following items should be completed
before
the startup technician arrives.
The unit is pre-wired at the factory. The necessary field wiring connections are described below.
1.
Control power of 115 VAC 50/60 HZ must be wired to the left side terminals of the digital I/O board inside the
ViSSion
®
cabinet. Line power (L1) is brought in to a 10-amp fuse via the terminal marked “L1” on the appro-
priate connector. The neutral (L1A) is brought in and connected to any of the “N” terminals located on left
connectors. Two separate line power feeds for the oil heaters are brought to two additional 10 amp fuses via the
terminals marked “L2” and “L3” on the same connector just below the “L1” terminal. The neutrals for these
circuits (L2A and L3A) are also connected to any of the “N” terminals. For units with V-PLUS
®
oil cooling, L1
must also be brought to the fuse in the V-PLUS® panel, and L1A must also be brought to the terminal #2B in the
V-PLUS
®
panel.
2.
An auxiliary contact from the compressor motor starter is required. This isolated contact is connected to the K-
1 input relay using any of the “L” terminals on the strip of connectors, and returned to the terminal marked
“Motor Starter Aux. Safety” at the very top connector.
3.
A dry contact from control relay K-22 must be wired to the compressor motor starter coil. This dry contact is
wired to terminals marked “Compressor Start – N.O. #1A” and “Compressor Start – N.O. #1B”. Control power
for this coil should come from a source, which will be de-energized with the compressor disconnect.
4.
A dry contact from control relay K-19 must be wired to the oil pump motor starter coil. This dry contact is wired
to the two terminals marked “Oil Pump Starter”. Control power for this coil should come from a source, which
will be de-energized with the compressor disconnect.
5.
An auxiliary safety cutout is available to shut down the compressor package using the K-2 input relay. A dry
contact must be supplied and wired to one of the “L” terminals on any of the connectors, and returned to the
terminal marked “Auxiliary #1 Safety” at the top connector. The jumper to the “Auxiliary #1 Safety” terminal
must be removed to use this cutout. The contact, if closed, will allow the compressor to run. If this contact
opens at any time, the compressor will shut down.
6.
Indication of the compressor alarm or shutdown status is also available via two control relays. Relay K-20 is
provided for remote trip indication and relay K-21 is provided for remote alarm indication. Each relay has three
terminals available: a common input, a normally open contact, and a normally closed contact. For both relays,
the energized state represents a “trip” or “alarm” condition. Loss of voltage to the relay coil and the resultant
return to normal state indicates “safe” condition.
7.
The current transformer supplied in the compressor motor conduit box should be checked to insure that the
motor leads of one leg are pulled through the transformer. Note that there is a dot on one side of the current
transformer. This dot must face away from the motor. Typically, a wye delta started motor should have leads 1
and 6 pulled through this transformer for a 6 lead motor. However, this should always be checked as different
motors and starting methods will require different leads to be used.
Order #_______________________________Compressor Serial #________________________
Summary of Contents for VSM 71-701
Page 1: ...1 VPN 35391S February 2006 Rev 05 Price 60 00...
Page 2: ...2...
Page 20: ...20...
Page 52: ...53 Pre Start Up Check List...
Page 99: ...99 Recommended Spare Parts List...
Page 104: ...104 Gate Rotor...
Page 110: ...110 Main Rotor VSS...
Page 112: ...112 Main Rotor VSR...
Page 114: ...114 Slide Valve Cross Shafts and End Plate...
Page 118: ...118 Capacity Slide Volume Slide Carriage Assembly Slide Valve Carriage Assembly...
Page 134: ...134 Miscellaneous Frame Components VSS Screw Compressor VSR Mini Screw Compressor...
Page 138: ...138 C FlangeAdapter Components 630 620 610 640 601 641 630 601 620 610 640 641 642 650 651...
Page 140: ...140 Replacement Parts Tools...
Page 144: ...144 GaterotorAssembly...
Page 148: ...148 Main Rotor Slide Valve Cross Shafts and End Plate Models 71 401 Only Counter clockwise...
Page 152: ...152 Main Rotor Slide Valve Cross Shafts and End Plate Model 501 701 Only Clockwise...
Page 154: ...154 Volume Ratio Capacity Slide Carriage Assembly Slide Valve Carriage Assembly...
Page 158: ...158 Miscellaneous Frame Components Model VSM 501 701 Model VSM 71 401...
Page 160: ...160 Replacement Parts Accessories Housing Accessories C Flange Assembly...
Page 166: ...166 Haight Pumps...
Page 170: ...3 Refrigerating Specialties Division...
Page 236: ......
Page 237: ......
Page 238: ......
Page 243: ......
Page 244: ...168...