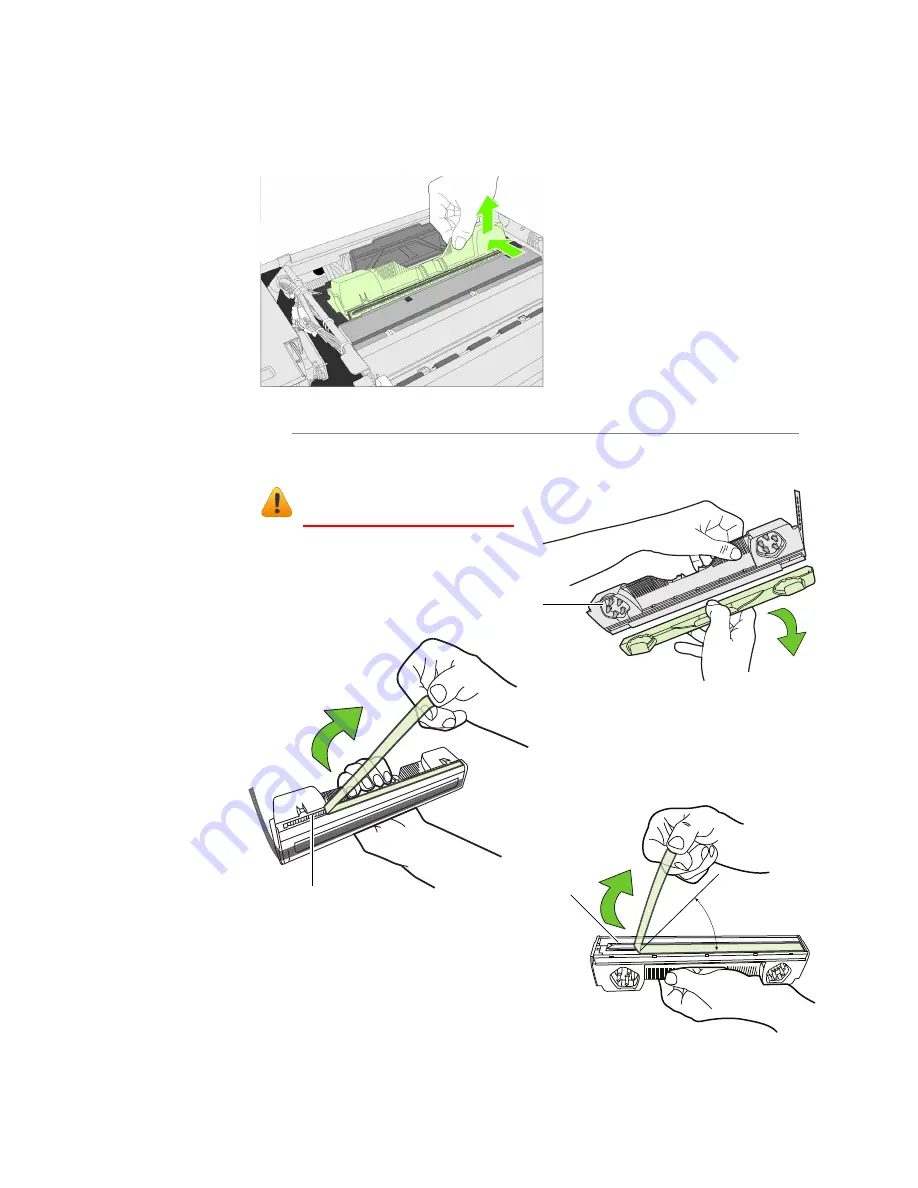
42
Printer Maintenance
4. Hold the printhead by the handle and push it toward the printhead latch. Once
the printhead is released, lift it out of the printer.
NOTE:
Dispose of the old printhead according to local regulations.
5. Remove the new printhead from its packaging.
Do not touch the ink couplings,
electrical contacts, or nozzles.
ink couplings
electrical contacts
nozzles
No less than 45°
NOTE:
Keep the orange cover. You
will need it to cap the printhead if it
is removed from the printer.
Summary of Contents for VP6 Series
Page 1: ...U s e r G u i d e VIPColor VP6xx Printer Series ...
Page 36: ...36 Using the Printer ...
Page 58: ...58 Printer Maintenance ...