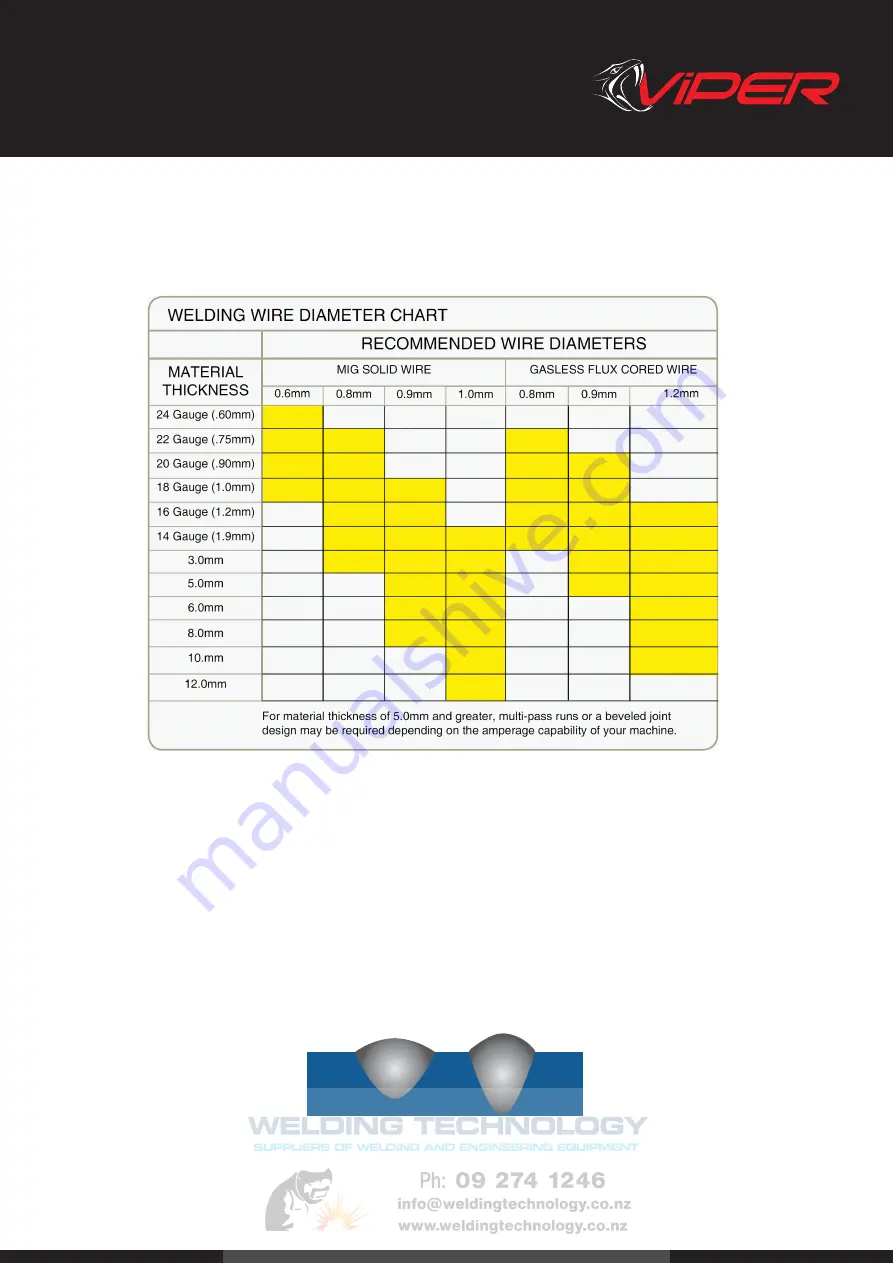
Wire types and sizes
Use the correct wire type for the base metal being welded. Use stainless steel wire for stainless steel, and steel wires for steel.
Use a smaller diameter wire for thin base metals. For thicker materials use a larger wire diameter and larger machine, check the recommended welding
capability of you machine.
As a guide refer to the “Welding Wire Thickness Chart” below.
Gas selection
The purpose of the gas in the MIG process is to protect / shield the wire, the arc and the molten weld metal from the atmosphere. Most metals when
heated to a molten state will react with the air in the atmosphere, without the protection of the shielding gas the weld produced would contain defects
like porosity, lack of fusion and slag inclusions. Additionally some of the gas becomes ionised (electrically charged) and helps the current flow smoothly.
The correct gas flow is also very important in protecting the welding zone from the atmosphere.
Too low flow will give inadequate coverage and result in weld defects and unstable arc conditions.
Too high flow can cause air to be drawn into the gas column and contaminate the weld zone.
Use the correct shielding gas. Co2 is good for steel and offers good penetration characteristics, the weld profile is narrower and slightly more raised
than the weld profile obtained from Argon Co2 mixed gas. Argon Co2 mix gas offers better weld ability for thin metals and has a wider range of setting
tolerance on the machine. Argon 80% Co2 20% is a good all round mix suitable for most applications.
Argon Co2
Co2
Penetration Pattern for Steel
VIPER 120 SYNERGIC MIG Welder |
19
MIG WELDING GUIDE